Reducing Ergonomic Claims: A Path to Business Savings
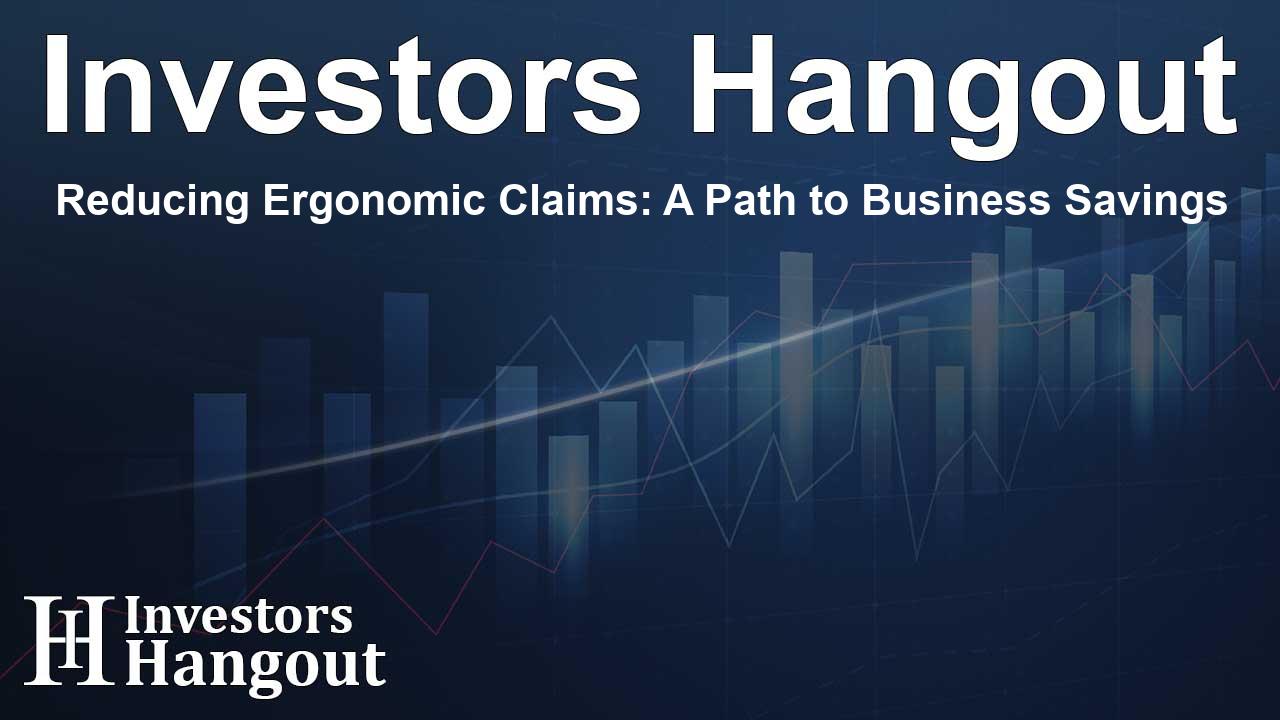
The Financial Impact of Ergonomic Claims
Musculoskeletal disorders (MSDs) are a significant concern in many industries, particularly those involving manual labor. These injuries lead to nearly 400,000 incidents each year and contribute to around one-third of workers' compensation expenses. The financial burden of these claims is staggering, reaching an estimated $60 to $80 billion annually. This figure highlights the importance of addressing ergonomic issues in the workplace.
Understanding Direct and Indirect Costs
The average cost of a cumulative trauma claim stands at approximately $29,000. However, when factoring in indirect costs like lost productivity and product defects, the total expense can escalate dramatically. Research shows that for every dollar spent on direct costs, employers are likely to incur an additional $2.12 due to these indirect expenses. This illustrates the critical need for companies to focus on reducing these costs through effective ergonomic strategies.
Industries at Risk
Certain sectors experience higher rates of ergonomic claims. Industries heavily reliant on manual material handling, particularly warehousing and manufacturing, are prime culprits. In recent years, the transportation and warehousing sector reported the highest rates of serious injuries and illnesses, with an alarming 3.8 cases per 100 workers. Companies embracing ergonomic improvements have reaped significant benefits. For instance, some firms have cut costs by up to 80% after implementing ergonomic best practices.
Strategies for Prevention
To mitigate the risks associated with ergonomic claims, manufacturers must implement a proactive ergonomic process. This process should include the following key steps:
1. Management Support
Secure commitment from management to prioritize ergonomic initiatives. This sets the tone for a workplace culture focused on safety and employee well-being.
2. Worker Involvement
Encourage workers to participate in identifying hazards. Their hands-on experience can lead to valuable insights regarding potential ergonomic issues.
3. Training and Awareness
Provide comprehensive training on ergonomics and injury prevention to employees. This empowers them to recognize risks and take appropriate actions in their workspaces.
4. Assessment of Ergonomic Problems
Regularly evaluate workstations and procedures to identify ergonomic problems. This assessment should be ongoing to keep pace with any changes in workflows.
5. Hazard Control Solutions
Once problems are identified, implement appropriate solutions to mitigate hazards. This could involve redesigning workspaces or providing ergonomic tools and equipment.
6. Early Reporting of Symptoms
Encourage employees to report symptoms of MSDs early. Prompt action can help prevent the escalation of injuries and reduce long-term absenteeism.
7. Evaluating Effectiveness
Continuously assess the effectiveness of the ergonomic process. Gather feedback and make necessary adjustments to ensure sustained improvements.
By implementing these strategies, manufacturers not only protect their workforce but also create a dynamic workplace that promotes productivity and minimizes turnover rates.
About Flexible Assembly Systems
Flexible Assembly Systems specializes in supplying ergonomic solutions aimed at enhancing workplace safety and efficiency in manufacturing sectors such as automotive, aerospace, and electronics. With a commitment to innovating ergonomics, the company empowers businesses to create safer work environments.
Frequently Asked Questions
What is the main issue with ergonomic claims in businesses?
Ergonomic claims lead to numerous injuries and significant financial costs for employers, affecting productivity and worker health.
How much do ergonomic claims cost annually?
Ergonomic claims cost businesses an estimated $60 to $80 billion each year due to direct and indirect expenses.
What industries are most affected by ergonomic injuries?
Industries involving manual labor, especially warehousing and manufacturing, face the highest rates of ergonomic-related injuries.
What steps can businesses take to reduce ergonomic injuries?
Implementing comprehensive ergonomic assessment processes, involving workers, and providing training can significantly lower injury rates.
How can early reporting benefit employers and employees?
Encouraging early reporting of symptoms can prevent serious injuries from developing, benefiting both employees' health and reducing long-term costs for employers.
About The Author
Contact Evelyn Baker privately here. Or send an email with ATTN: Evelyn Baker as the subject to contact@investorshangout.com.
About Investors Hangout
Investors Hangout is a leading online stock forum for financial discussion and learning, offering a wide range of free tools and resources. It draws in traders of all levels, who exchange market knowledge, investigate trading tactics, and keep an eye on industry developments in real time. Featuring financial articles, stock message boards, quotes, charts, company profiles, and live news updates. Through cooperative learning and a wealth of informational resources, it helps users from novices creating their first portfolios to experts honing their techniques. Join Investors Hangout today: https://investorshangout.com/
The content of this article is based on factual, publicly available information and does not represent legal, financial, or investment advice. Investors Hangout does not offer financial advice, and the author is not a licensed financial advisor. Consult a qualified advisor before making any financial or investment decisions based on this article. This article should not be considered advice to purchase, sell, or hold any securities or other investments. If any of the material provided here is inaccurate, please contact us for corrections.