A Manufacturing Revolution in the Making Digi
Post# of 63839
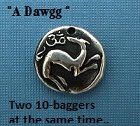
A Manufacturing Revolution in the Making
Digital technology is transforming manufacturing, making it leaner and smarter—and raising the prospect of an American industrial revival
On a dark and stormy night two weeks ago in Schenectady, N.Y., Ken Hislop was relaxing at home when his cellphone suddenly began buzzing in his pocket. It was an urgent text message—from the General Electric Co. GE -0.34% factory where he works.
Soon, a second message arrived. And then another, and another. The texts were being sent by tiny sensors embedded inside a series of machines, some of which look like enormous upside-down cement mixers. A violent thunderstorm passing through the area had caused something to go wrong.
"I knew right away we'd lost power at the plant," says Mr. Hislop, a manufacturing engineer. He quickly switched on his iPad and accessed animated schematic maps that signaled everything happening at the $170 million facility, which makes massive batteries for things like cellphone towers and power plants. Though the outage had been momentary, much of the equipment at the factory had to, in effect, reboot, and any blip could mean costly lost production time.
"I was getting a first-person, real-time account," says Mr. Hislop, who also could watch video of the storm from the plant's roof. The information allowed him to ensure that the machinery restarted in proper sequence and that the sensitive battery material hadn't been damaged.
Welcome to the New Industrial Revolution—a wave of technologies and ideas that are creating a computer-driven manufacturing environment that bears little resemblance to the gritty and grimy shop floors of the past. The revolution threatens to shatter long-standing business models, upend global trade patterns and revive American industry.
Impacts Big and Small
For big companies, it means a swath of new tools to build smarter, leaner factories and explore innovative new products, materials and techniques that weren't possible before. And thanks to plummeting prices, small companies have access to better, cheaper manufacturing equipment and design tools—giving even one-person startups the chance to create market-shaking innovations. Many people liken the era we're in to the early days of computing, where upstart hobbyists in their garages came up with huge advances that changed the industry. (See "Build a Better Mousetrap—Fast" on page R7.)
"Manufacturing is undergoing a change that is every bit as significant as the introduction of interchangeable parts or the production line, maybe even more so," says Michael Idelchik, who heads up advanced technologies at GE's global research lab, located about 15 minutes away from the battery plant. "The future is not going to be about stretched-out global supply chains connected to a web of distant giant factories. It's about small, nimble manufacturing operations using highly sophisticated new tools and new materials."
There's no question that a coinage like the New Industrial Revolution sounds magisterial, given the profound impact that the original Industrial Revolution had not just on business but on living standards around the world. And there's also no question that for all the big talk and big forecasts, many things will go on being produced using techniques that were all but perfected long ago.
But the big label is far from unwarranted. The upheaval, still in an early stage, is accelerating now thanks to the convergence of a number of trends: the low cost and accessibility of Big Data associated with cloud computing; the plummeting cost of electronic sensors, microprocessors and other components that can be used to make machines more adept; and advances in software and communications technology that make it possible to manage manufacturing with a whole new level of precision and enable new forms of collaboration.
A new wave of supercheap electronic sensors, microprocessors and other components means that facilities like Mr. Hislop's need almost no human help to do their jobs and can collect huge amounts of data along the way. Managers can get instant alerts about potential problems or study the numbers to find ways to boost efficiency and improve performance.
Flexible Fabricating
At the same time, technological advances now allow manufacturers to invent new ways of fabricating things that represent an extreme departure from the classic production-line model. By far the most significant of these steps forward is additive manufacturing—a process of making a three-dimensional object of virtually any shape from a digital model.
These exotic machines can use a range of materials—everything from wood pulp to cobalt—and create things as varied as sneakers, fuel nozzles for airplanes and, ultimately, even human organs. And a single piece of manufacturing equipment, rather than being custom-designed to perform a single function, can be programed to fabricate a virtually limitless array of objects.
And, of course, that includes making more machines. On a tour of a laboratory of advanced manufacturing equipment that Autodesk Inc. ADSK -1.86% is building on a pier in downtown San Francisco, Chief Executive Carl Bass points to some masking tape on the ground that marks the spot where a sophisticated computer-controlled milling machine will be housed.
"The Japanese company Mori Seiki is making that in Sacramento in an automated factory," says Mr. Bass, whose company creates computer-aided-design software. "The factory is so advanced that you almost don't need to turn on the lights because the machines are doing everything, and what they are making is other machines." In fact, a 3-D printer has replicated itself at a university in England.
Still, manufacturers will have to navigate big new challenges in this era, too. For one thing, because additive manufacturing works from digital models of objects, companies are much more vulnerable to intellectual-property theft—the same way that easily copied music and movies have shaken the entertainment business.
The Sole of a New Machine
To get an up-close look at how the new technologies are already disrupting the old ways of doing things, consider Nike Inc.'s NKE +0.46% Flyknit shoe
As high tech as some sneakers may be in materials and appearance, almost all of them are still made on assembly lines that put a shockingly heavy emphasis on human labor. Workers sit side by side in enormous facilities, cutting material and stitching and gluing shoe components together. But, starting last year, Nike began making the Flyknit a whole new way.
The company's engineers modified a machine used to make sweaters into a shoe-making contraption that knits the entire upper portion of the shoe in a single cocoon-like piece that is then attached to the tongue and to the sole. As the shoe is stitched, proprietary software instructs the machine to alter the materials being used—a bit more polyester thread here, a bit more there—to add strength or flexibility where needed.
Most important, it makes all these refinements at no added cost. The technology allowed Nike to make a shoe with just a few parts instead of dozens and with up to 80% less waste. "The Nike Flyknit is the world's first mass-produced consumer product made using additive manufacturing," says Maurice Conti, director of strategic innovation at Autodesk, which worked with Nike on the Flyknit project. "It's a hugely significant advance, not the least because, once you start doing things this way it obviously takes a lot of the labor cost out of the equation."
The implications for this are as obvious as they are profound: Almost seemingly out of the blue, the reason for making shoes in low-wage countries begins to evaporate and the advantages of locating the machine closer to the customer—in part for faster delivery—begin to loom much larger. Already, Adidas AG ADDYY +0.50% is knitting a shoe, the Primeknit, in its home country, Germany.
Last year, Boston Consulting Group published a report predicting that as much as 30% of America's exports from China could be domestically produced by 2020. President Obama gave a nod to this hope in his State of the Union address in February when he said that the popular additive-manufacturing technique called 3-D printing "has the potential to revolutionize the way we make just about everything."
Last year the president proposed a $1 billion addition to his fiscal 2013 budget to create a network of as many as 15 manufacturing-innovation institutes around the country. One is already up and running in Youngstown, Ohio, the setting of the Bruce Springsteen song about the rise and fall of the steel industry. Three more are in the works under the supervision of the Department of Energy and the Defense Department. Congress has yet to approve spending for the others.
Not So Fast
But the jury is out on whether a boost in manufacturing will create a resurgence in U.S. manufacturing employment, which peaked at around 19.5 million in 1979 and today totals around 12 million, according to the Bureau of Labor Statistics. (Economists attribute the recent modest increase in U.S. manufacturing employment to a rebound in the business cycle, and have found no evidence yet of an employment rebound connected to advanced manufacturing or the return of jobs from overseas.)
Almost certainly, it won't mean creating jobs the old way—building large factories that employ thousands of people. The real opportunity is in the growth of highly specialized, highly advanced microfactories and in legions of small entrepreneurial ventures making old things in new ways, as well as producing new products and custom-made items. An important sign of the times: the largest U.S. maker of 3-D printers, 3D Systems Corp., DDD +3.99% introduced a slick push-button model for $1,299 last year—putting it within range of the smallest businesses and home users. Kits to make a printer powered by software from the open-source RepRap project run as low as $400.
Experts envision bike shops that print custom frames and assemble bikes on demand; made-to-order shops or websites that offer one-off or personally designed jewelry; and more sophisticated production shops that crank out all manner of high-end products. Already, a company called Bespoke Products, a unit of 3D Systems, is making artificial limbs. Another, Organovo ONVO +2.25% Holdings Inc., is using 3-D printing to create human tissue for use in medical labs. At a recent conference, the company showed off a piece of raw meat it had made in a printer. Over time, this "democratization of manufacturing," as some refer to it, is expected to accelerate, and one day could mean that your local auto dealer or maybe even your neighbor (or you) will be able print out a replacement part for your car or make you a new cup holder sized perfectly for that enormous thermos you carry around.
New Ways of Making
Additive manufacturing may bring other changes that are just as dramatic as "factories" run out of somebody's garage. Additive manufacturing makes it possible to create designs or structures that weren't feasible using the two traditional ways of making things: milling (sculpting material out of a solid block) and casting (pouring liquid material that hardens into a mold). Both of these techniques are greatly enhanced by mass production because quality typically rises and costs fall as volume increases. Making a lot of something also means it's not so painful to discard defective units.
Mataerial, a prototype 3-D printer that can make curved objects.
But additive manufacturing enables the creation of materials with multiple parts and moving components without assembly. And because the process is entirely controlled by computers, following precise digital instructions, the very first piece that's manufactured is just as good as the last one. The incremental cost of producing a part becomes strictly a function of time and materials.
All of which means manufacturers can scan further afield for inspiration. Designers and engineers at General Electric have begun looking at ancient objects and prehistoric bird skeletons, and delving anew into topology, for inspiration on new forms of design. Their thinking: Centuries of making things under the constraints of old methods may have caused their predecessors to discard innovative structures simply because there was no practical way to produce them through milling or casting. But what was impractical in the past may be quite feasible today.
There's another big change playing out that isn't so obvious but could have a huge impact on the world of manufacturing. The rise of the 3-D printer has coincided with the digitization of the physical world through the use of 3-D scanners and, increasingly, two-dimensional photos that can be stitched together digitally using software to create precise 3-D renditions of anything made of atoms.
That affects everyone who works with manufacturers and who participates in the creative process: designers, engineers, materials specialists, machine makers and supply managers, among others. It's much easier to collaborate on a model if it is stored on a computer, because lots of digital hands can be working on it at the same time.
"The big untold story in all of this is the way the digitization of manufacturing compresses everything—from the early design of a product to its final assembly," says Ping Fu, who founded a company called Geomagic that makes 3-D modeling software and is now in charge of strategy at 3D Systems. "Everyone can now work together simultaneously. The software makes it possible, and you get much better results than when all of these activities were being done in different silos."
Still, this new environment leaves manufacturers facing big new challenges, as digital files of physical objects show up in huge numbers on websites like Thingiverse and Physibles, and manufacturing instructions appear online, too.
"I give a lot of speeches about this topic to manufacturing groups, and people are usually quiet during the Q&A," says Christine Furstoss, who oversees a staff of 450 engineers and scientists working on materials, energy strategy and processing technology at GE's research center. "But afterward, they come up to me in private and want to talk about how frightened they are. People get a glimpse of how this could change the game in their business, and they are just not sure what to do about it."
The Road Forward
For an idea of how the New Industrial Revolution might play out on a large scale, look at GE. Its footprints are everywhere in the advanced-manufacturing community. It is a highly visible participant in the federal government's efforts to boost additive manufacturing, as well as university programs focusing on the topic. Partners include the Massachusetts Institute of Technology, Amazon.com's AMZN +1.49% Web-services department and the Defense Advanced Research Projects Agency, which are collaborating with GE on a new crowdsourcing platform for product design and development.
High-tech batteries from GE.
The company also is latching onto the technique in-house. For instance, it is making a big bet on additive manufacturing as a way to create engine parts that weigh less, cost less and employ more intricate designs. Last year, it bought one of the largest additive manufacturers in the U.S., Morris Technologies, and plans to use the company to make the sophisticated fuel nozzle for its next-generation jet engine, the LEAP. (The Morris family has a long industrial pedigree: It once supplied steel tubing to the Wright Brothers' bicycle shop.)
The new nozzle will be 3-D printed as a single part rather than assembled from 18 pieces, and it will be up to five times more durable. GE is also running its own 3-D metal printers, testing the procedure out on as many parts as possible for both the LEAP and the GE 9x, its next-generation 777 engine. This week, GE plans to announce a major investment in an another new additive-manufacturing factory that will mass-produce ceramic engine shrouds.
All told, the company projects it will spend $3.5 billion on aviation-related advanced manufacturing in the next five years and will produce 100,000 end-use parts for its engines annually by 2020 using additive techniques.
One of GE's most creative initiatives is an arrangement that will begin to make its more than 30,000 patents available to inventors and entrepreneurs who use the website Quirky—which employs crowdsourcing to evaluate ideas for products. "It's a whole new paradigm for innovation," says Ben Kaufman, the founder of Quirky, an industrial-design company in New York.
Starting this month, inventors and their ilk will be able to sift through the first 200 of GE's patents posted on Quirky, with more than 1,000 expected to be available by the end of the year. People who think they can use the technology without infringing on GE's own use will be able to click a button and begin a process enabling them to license use of the patent for whatever application they've dreamed up.
GE's efforts also offer a look at how data can be leveraged in this new era. One of the take-aways from a visit to GE's battery plant back in Schenectady, located adjacent to a parcel that housed Thomas Edison's machine works, is the sheer volume of data it generates—information that allows plant engineers to continually improve the production process and head off problems before they become serious.
The company can trace a product's entire genealogy, from containers of dirt, sand and salt to a bank of high-tech batteries supporting a nation's electric grid. The data not only improve quality control—if a defect shows up at any point, GE can trace it back to its original source—but in the end give GE a powerful competitive weapon that's virtually impossible to duplicate.
The Schenectady plant, nestled in a valley alongside the Mohawk River, is so extensively networked and connected, in fact, that it might just as easily be thought of as a single machine rather than a collection of them. And, of course, because it is so automated, it doesn't require a whole lot of human assistance. GE's Schenectady campus once had so many employees it was given its own ZIP Code, 12345. Yet even when it reaches full production—GE expects its output to exceed $1 billion in annual sales by 2020—the showcase battery plant won't employ more than 450 people.
Mr. Hislop, who confesses to using his iPad to check in on the factory during a recent camping trip, describes his experience on the night of the storm in the tones of an anxious parent. Yet in the midst of the howling winds and thunderclaps, the technology meant he could remain intimately in touch with everything that was happening across town. Despite the beating the plant was taking, he says he felt "reassured."

