How 3-D Printing Works The process turns conventi
Post# of 63838
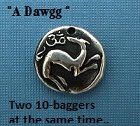
How 3-D Printing Works
The process turns conventional manufacturing on its head, producing objects from the bottom up
People have traditionally made things—from doorknobs to scalpels to engine cylinders—in one of two ways. They start with a solid block or sheet of metal, wood or other material and cut, stamp, drill or shave it to create a desired shape. Or they use a mold made of metal or sand, pour liquefied plastic or metal into it and let it cool to create a metal casting or molded plastic part.
Now for something completely different.
Three-dimensional printing and other forms of what is known as additive manufacturing use neither machining nor molds. They build an object from the bottom up by piling razor-thin layers of material on top of each other until a three-dimensional shape emerges. The computer-guided technologies enables individuals to create objects, particularly prototypes, without a shop full of metal presses, cutting lathes or plastic injection molds.
There are a variety of processes for 3-D printing. Some of the most widely used rely on a printer that makes objects from powdered material. A 3-D printer bears little resemblance to a document printer in an office. It has two major parts: a "build box" that contains a smooth, thin bed of finely ground material such as pulverized stainless steel or powdered plastic; and a printing head. Depending on the type of printer, the head contains either a heat source, such as a laser or an electron beam, that melts the powdered material or jets that spray binder over the powder in a precise pattern. The binder functions as a glue for the material as an object is built.
The world-wide market for 3-D printing, which includes materials, machines and service, totaled $2.2 billion last year, up 29% from 2011, according to industry estimates. But the process has some limitations. For high-volume jobs, 3-D printing can't yet match the speed and efficiency of traditional fabrication methods and machinery. Not all materials are suitable for powder-based additive manufacturing, and not all objects, particularly those made of metal, are able to stand up to high-stress use. For manufacturers of 3-D equipment, the future of their nascent industry depends on broadening the appeal of their equipment by expanding its uses and versatility.

