Squeezing fuel out of plastic waste
Post# of 43066
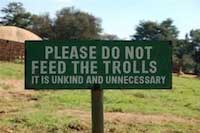
R BALAJI
Paterson Energy produces a cheaper alternative to diesel that can fire generators, kilns...
A business born out of commitment to a clean environment, a technology honed over years, scaled up to commercial levels and proven in the field — that is Paterson Energy for you.
The company builds plants that can process plastic waste to produce liquid fuel that is cheaper than diesel and a substitute to fuel generators, industrial boilers, kilns, furnaces diesel-powered engines and other such equipment.
Paterson Energy’s plants deliver the double benefit of tackling plastic waste and producing a useful product from waste.
Even waste such as shopping bags and miscellaneous plastic stuff that are not normally picked up by rag pickers for recycling can be used as a raw material. Plastics are the bane of urban development, they do not degrade, they clog drains, choke livestock, mar the environment and are piling up by the day. But now there is a solution, and “it is environment-friendly and bankable,” says Vidya Amarnath, Director, Paterson Energy.
In-house tech
The technology developed in-house involves thermochemical depolymerisation – essentially breaking down plastic at 300-500 degrees Centigrade in the absence of oxygen to get the liquid fuel. Some gases generated during the process are reused for heating. Any solid residue in the final stage is much like carbon black, can be used in diverse ways including as hollow blocks. So it is a “zero-discharge, zero-effluent plant,” she says.
Initially, the whole concept was kicked off as a social cause to rid cities of plastic waste. But with the potential to expand the scope of the project and the company recently bagging a contract from Engineers India Ltd to set up a 5-tonne-a-day waste-to-fuel project at Mathura in Uttar Pradesh, Paterson Energy has crossed a critical threshold. It hopes to tap the emerging opportunities in this line, she says.
This is a sector that is opening up. The project is one of many planned by the government as part of the Swachh Bharat initiative to clean up temple towns and tourist centres. Companies such as Paterson Energy can look forward to exploiting such opportunities.
K Venkatesh, President, Paterson Energy, says the proposed plant in Mathura is part of a ₹9.5-crore contract with ₹5.5 crore coming in as a viability gap funding, ₹2.5-3-crore plant cost and the balance being operational cost. The company will set up the plant and handle the operation and maintenance for 15 years. Paterson Energy gets to sell the plastic oil and retain the revenue. The plant will generate about 2,500 litres of oil per day with the average price estimated at about ₹40 a litre.
Increasingly, as local administrations move towards more stringent waste management, Paterson Energy sees a growing demand for its solution. Look at any major urban centre or industrial hub and plastic waste will be a significant issue, he points out. For instance, the Centre’s Waste Management Rules 2016 dictate tough guidelines for industries that generate plastic and holds them responsible for safe disposal.
But, Venkatesh emphasises, the primary objective of a plastic fuel plant is waste management. Oil is only the icing on the cake. Citing possible instances where the solution can be applied, he points out the Sriperumbudur belt, a major automobile hub near Chennai, generates about 70-80 tonnes of plastic waste daily. Paper manufacturers using recycled paper as raw material generate huge plastic waste from multi-layered and coated paper. A 300 tonne-per-day de-inking plant that converts used paper to paper pulp will generate about 15-20 tonnes of waste plastic.
The first of Paterson Energy’s 3-tpd plant was put up at its own cost at Valarpuram in Sriperumbudur. It has now been expanded to about 7.5 tonnes.
Some of these industries are keen to use this option to deal with plastic wastes. This method of plastic disposal can also come under CSR activity of the corporate sector, he says.
A viable option
Vidya points out that with industries stuck with huge volumes of plastic, Paterson Energy’s solution is a viable option. The technology has been fine tuned in-house. The company has the support of experts from IITs, Central Institute of Plastics Engineering & Technology. It has standardised production of plants of 3–20 tpd capacity based on thermochemical depolymerisation. It is recognised as a start-up by the Department of Industrial Policy & Promotion of the Commerce Ministry.
The company is keen to infuse funds for the next level of expansion and is looking to tap various sources including private equity, Vidya says.
www.thehindubusinessline.com/specials/emerging-entrepreneurs/squeezing-fuel-out-of-plastic-waste/article9932542.ece

