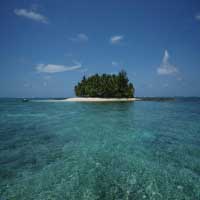

Iron ore pelletizing
Metso grate-kiln systems
Iron ore is upgraded to a higher iron content through concentration. The concentrate must be pelletized in order to feed a blast furnace or a DRI plant.
Metso designs and supplies Grate-Kiln systems. These plants produce pellets at a lower cost and higher quality than other types of pelletizing systems.
Metso has designed and supplied the most modern and largest grate-kiln systems in the world. These plants produce pellets at a lower cost and higher quality than other types of pelletizing systems, such as shaft furnaces or straight grates.
What
Pellets are indurated, spheres of ore with a high iron content and uniform quality.
Pellet plants can produce two varieties of pellets: blast furnace pellets and direct reduction pellets (DR pellets). Blast furnace pellets are used in the coke-based blast furnace process, which is the most common method of producing hot metal (molten iron for steelmaking). Blast furnace pellets are delivered mainly to steel mills.
DR pellets are used in the direct reduction processes to produce sponge iron, which is an alternative process route, as an initial stage from iron to steel. The DR process is primarily based on the use of natural gas and has become increasingly common in countries with access to inexpensive natural gas.
Process
The object of the process is to transform the pelletized concentrate into hardened pellets that can be used as blast furnace feed or direct reduction furnace feed. The transformation is achieved by the traveling grate and kiln. The traveling grate transports the pelletized concentrate through a series of controlled temperature zones to produce a preheated pellet of 800-900°C, which is dropped into the rotary kiln. The rotary kiln finishes the induration and is operated at 1200-1350°C. The indurated pellets are now dropped into an annular cooler where the pellets are cooled to a suitable temperature for transporting on a belt to load out facilities. The gases from the cooler are recycled to the kiln and the grate, resulting in the Grate-Kiln being the most energy efficient system for producing indurated pellets.
Equipment
An iron ore plant contains many pieces of equipment. The major areas or process are the concentrator, balling, induration and handling. The concentrator is where the ore is ground to a fine size typically 80% - 45 micron powder and separated from other impurities by magnetic separation and flotation. The balling area is where the powdered ore is mixed with water, binder and rolled in rotating drums to create spherical balls. The induration area actually can be broken down into three areas: grate, kiln, cooler. The grate area is where the pellets are dried and the induration process is started. The pellets at this stage are becoming stable and can be dropped into the kiln without braking. The kiln is used to drive heat into the pellets to force the reaction throughout the pellet. In an effort to recoup all the heat that is currently in the pellet after the kiln, the pellets fall into a cooler. The Grate-Kiln System is basically a counter-flow heat exchanger; that is, the material (green pellets and indurated pellets) moves in a direction opposite to that of the process gas flow.
For more detail see individual equipment.
>See also Control Systems for iron ore pellet plants
Attachments:
Brochure Grate Kiln for Iron Ore Pelletizing EN (723 kB)
Brochure Grate Kiln for Iron Ore Pelletizing CH (2540 kB)

