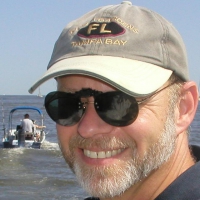
My letter sent in response to the email received asking for feedback to the Investor Update:
- we need to transform Processor #1 into a revenue center, even if it’s not the ‘workhorse’ that Processor #2 is.
- The technology behind Processor #2 is sound; however, we have to continue to reduce the downtime between runs.
- we need to get Processor #3 operational, producing fuel and revenue as quickly as possible.
- We are making good, albeit slow, progress with RockTenn ... there is a master agreement in place and there will be addendums for each site. We are currently negotiating the fine points relative to the Jacksonville site.
- With regards to future financings, to date it has been appropriate to sell equity in private placements to high net worth individuals. We believe we are moving into a stage of development where we also will be attractive to institutional investors.
- Our primary challenge at JBI is in reducing downtime. Our Plastic2Oil technology is sound. The downtime that we experience is primarily driven by operational and engineering issues, not issues related with the technology.
- Our main opportunity for improvement is reducing the time it takes between runs and this is something that we feel we are addressing through engineering improvements, system standardization, operator controls and changes to our plant management structure.
- Ideally, we want “processor-ready” feedstock at reasonable pricing. Paying for material that is “processor-ready”, that doesn’t require any pre-processing such as shredding, many times, will be more economically viable than less expensive plastic that requires pre-processing before it can be fed into the P2O processors.
- Processor #1 will be used for production and R&D without affecting the production of the other two processors.
- Uptime is dependent on the amount of time in which residue accumulates. Even as residue accumulates, the inside of Processor #2 stays extremely clean, with little to no petcoke stuck to the walls.
- the main reactor in Processor #2 accumulates residue until the feed has to be stopped and the reactor emptied, resulting in downtime.
- The solution to this problem was to add a third, half-sized kiln to condition and continuously extract the residue from the processor in real time. So, Processor #3 is now a 3-kiln machine.
- The isolated cost to run Processor #2 with staff, utilities and depreciation included is minimal, at $0.11 per gallon of fuel produced.
- much of the costs incurred and the cost reduction that needs to take place is before the feedstock even gets to the machine.
- Since Fall 2012, processor #2 has been successfully operating in its final production state.
- Processors #4 and #5 are being constructed at this time.
- the team of 3 – the chemical engineer, the operator and the materials handler – work together to manage the process. Their 3 timelines and perspectives overlap and create a synergistic response.
- we are excited to be almost finished hiring to fill out 7 days a week, 3 shifts a day for the cluster of processors at the Niagara Falls plant.
- Heat transfer fluid is any hydrocarbon-based liquid, including waste oil, hydraulic oil, cutting fluids, off-spec lubricants and monomers and waste fuels derived from oil water separators. The benefits of combining the HTF with the plastic are:
1. | Densification and Heat Transfer – This is important because the waste oil used as heat transfer fluid acts as a natural densifier for the plastic. Also, because melting plastic is very endothermic by nature, using HTF allows us to transfer a lot of heat into large chunks of solid plastic and melt them much more quickly than large chunks by themselves. |
| Throughput Increase – Using heat transfer fluid reduces the residence time of the plastic in the system. In addition, pumping liquids into the system is much easier than handling solids or raw materials. Also, the HTF requires little or no pre-processing before hand. |
- We must amend our simple air permit and solid waste 360 permit before we can use heat transfer fluid in production.
- The issue of the wet plastic and "residual downtime experienced in Q1 2013" for testing HTF being the reasons for Q1 revenues now being forecast to be less than the meager revenues seen in Q4 has left all investors scratching their heads. How could a quarter previously forecast to be CFP have gone so wrong? Two functioning processors and so little revenue? Is it all due to "operational and engineering issues, not issues related with the technology"? Does this mean procuring the right feedstock and having the right engineering processes in place to process that feedstock? It sounded like there was plenty of feedstock
- Will P1 be used for generating revenue or will it continue to be an R&D unit? There seems to be some disagreement here.
- John said that P2 stays extremely clean, but also said that it "accumulates residue until the feed has to be stopped and the reactor emptied, resulting in downtime." How long can P2 run without being brought down?
- How long is P3 expected to be able to run without being brought down given the addition of the "half-sized kiln to condition and continuously extract the residue from the processor in real time"? Are there any plans to retrofit P2 with the half-sized kiln?
- Will P4 & P5 go into the new building with P3? Is there any outlook for when they will be ready for production? How will their assembly impact the production of P3?
- How long is it expected to take to "amend our simple air permit and solid waste 360 permit before we can use heat transfer fluid in production"? We were waiting a long time the last time we needed to amend the "simple air permit".
- Based on what has been said it seems the company is at the point of securing reliable sources of processor-ready feedstock and running at full production once P3 is in place? Is there any reason not to expect Q3 to be CFP? Could the installation of P4 & P5 prevent that?
- Is there any outlook for when processors will begin to be constructed for the RockTenn Jacksonville site? How will the issues seen in Q1 with wet plastic be addressed when processing RockTenn plastic, especially RockTenn's monofilled raggertail?


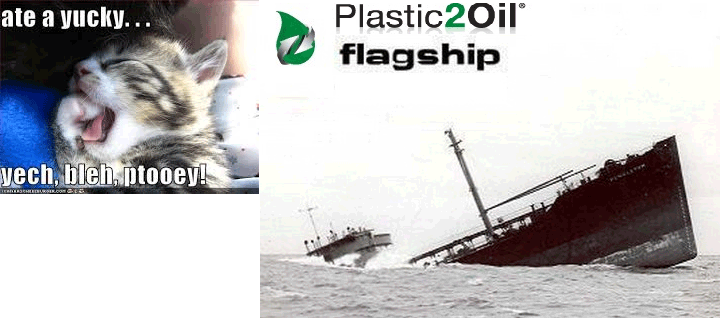