The Chloride Copper Mine is a fully developed oxid
Post# of 4018
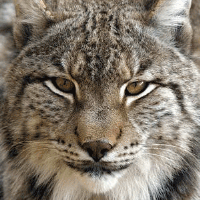
The Chloride Copper Mine is a fully developed oxidized copper ore body with complete solvent extraction and electro-winning plants. The copper deposit is classified as an exotic oxide copper where the copper mineral Tenorite acts a cement binding fragments in basal pediment conglomerate.
The geological reserve (proven, probable and possible) is 2.6 million tons grading 0.56% copper in-situ. The project also has 1.2 million tons of tailings grading 0.22% copper. The proven and probable reserve at the site, including tailings hosts 22.3 million pounds of copper using a 70% recovery factor in year one, 10% in year two and 5% in year three. The mining method used is open pit and the stripping ratio is 1.3:1, waste to ore. The project is currently on care and maintenance. The first two years of stripping will be minimal since the pit hosts approximately 860,000 tons of pre-stripped ore, the bulk of which has already been drilled and blasted, ready for mining.
Of the 22.3 million pounds of recoverable copper, 15 million pounds is considered to be easily recoverable and includes approximately 5 million pounds contained in tailings. The processing plants are designed to produce 8,000 pounds of premium grade cathode copper per day, grading 99.99% purity. Approximately 75% of the equipment required to expand the plant capacity to 15,000 pounds per day has been purchased and is on site, ready for installation. The cost of this expansion is included in the Capital Cost Section of this study.
The Chloride ore body hosts approximately 15 million pounds of easily recoverable copper in ore in the fully developed pit. The operation will commence by mining pre-stripped ore in the pit bottom, using the 825 series mine plans which contemplate the mining of 900,000 tons without major push-backs in the pit.
The 825 mine plan is included in the section titled ‘Mine Plans’. Year One and Two will focus on mining 586,ooo tons in the pit bottom which has zero stripping, has already been drilled, blasted and acidified. The availability of this ore will significantly decrease operating costs during the first two years of operations.
At approximately mid-Year Two, the limited push-backs in the 825 Mine Plan will commence to expose additional ore without significant stripping costs. Upon completion of the 825 Mine Plan, the mining will shift to the $1.15 pit with stripping ratio increasing to 3:1, waste to ore, exposing approximately 1.5 million additional tons of ore, depending on future prices.
Ore will be mined, crushed, agglomerated, acid cured and trucked to the new 350,000 square feet area to accommodate the remaining ore. Oxidized copper contained in the ore will be leached using a dilute solution of sulfuric acid, containing approximately 10 grams of sulfuric acid per liter of solution.
The acid reacts with the copper in the rock to produce a soluble copper sulfate which discharges to a lined collection ditch and runs to a pregnant leach solution (PLS) pond. This pond feeds the Solvent Extraction Plant. The copper is extracted using a commercial organic reagent in a kerosene organic solvent at approximately 7% reagent. This step is followed by a stripping step whereby the loaded organic is stripped using strong acid from the Electro-winning Plant. The Solvent Extraction step increases copper concentration from 1.5 grams of copper per liter in the PLS to 34 grams per liter in strong electrolyte.
The rich electrolyte is then pumped to the Electro-winning Plant where copper is electroplated from solution to form 99.99% pure copper cathode as the final product. Copper is stripped manually from stainless steel starter sheets, stacked, weighed and banded for shipment. For each pound of copper produced in electro-winning, 1.5 pounds of sulfuric acid is regenerated for subsequent use in leaching. This technology is proven and widely used with 30% of world copper production being generated in this way.
The Chloride Copper mine is located in northwestern Arizona approximately 15 miles northwest of Kingman. It is reached by following Highway 93 northwest from Kingman and then turning east just south of the town of Santa Claus and following a gravel road to the mine.
The Project is fully developed for operation. Approximately $2.6 million worth of infrastructure is in place at the mine, and processing facilities. Prior to restart of operations, additional capital will be required to complete rehabilitation of existing facilities to ‘like new’ condition and to expand the existing solvent extraction and electro-winning plants to produce 15,000 pounds per day of cathode copper.
This estimate assumes that the project will be mined by Desert Construction of Kingman, miner will receive a fixed payment per ton of material mined and they will furnish the required equipment for mining at his cost. Currently, the project has installed a lined PLS collection pond, a lined raffinate pond, solvent extraction and electro-winning plants, office, shop, warehouse and laboratory.
Ample water is available for operations. The company has right-of-way permits to three water wells and may lease more. This lease may be renewed in perpetuity.
The Chloride Copper property consists of 7 unpatented lode claims and 15 mill-site claims and 3 well site claims in sections 22 and 27, Townships 23N, R18W, Wallipai District, Mohave County, Arizona. The total area owned by SGV Resources at the Chloride Copper property amounts to approximately 154 acres.
There are no royalties or other residual interests to any third parties.
The U.S. Bureau of Mines reports indicate that a total of 1,400,000 tons were mined grading 1.0% copper during its ownership of the property. They reported copper recovery of 80% which correlates with the copper grade and tonnage of the tailings pile. An additional 235,000 pounds of copper as cathode copper was produced by TSC Enterprises following completion of the SX/EW plants.
The tailings produced by El Paso/U.S. Bureau of Mines are stored on site and contain 0.2% copper, or four pounds of copper per ton of tailings.
The Chloride copper deposit is located in the Sacramento Valley, half a mile from the west face of the Cerbat Range. Its geologic setting is an alluvium covered, gradually sloping pediment. The relief is low and undulating due to protruding bedrock and erosional dissection. This dissection, which is recent, is caused by ephemeral stream action commencing on the slopes of the Cerbat Range at the alluvium-bedrock contact and winding west and southwest into the Sacramento Valley.
The terrace beds and dissected portions of the apron reveal poorly sorted, mixed deposits of angular to sub-angular sand, pebbles, cobbles and boulder (up to 15 ft), representing all the rock units in the Cerbat Range. Crude stratification exists in some places, but the bulk of the apron flanking the range is largely mixed and unconsolidated.
The alluvial veneer at the Chloride deposit has been consolidated by mineralizing solutions to form the blanket of copper mineralization. The salts and clays eroded from the Ithaca Peak porphyry alteration halo surely contributed to the bonding of this detrital material. The U.S. Bureau of Mines refers to the mineralized portion of the consolidated veneer at Emerald Isle Mine (“EIM”) as the Gila Conglomerate, while everything above it is referred to as alluvium.
The source of the EIM mineralization is the low grade porphyry type mineralization at the head of Alum Wash, 1-1/2 miles NE of the deposit. Tenorite (CuO) is common and minor cuprite (Cu2O) and dioptase (CuSiO2(OH)2 have been identified. The copper mineralization occurs in fractures and as an interstitial cementing medium along with fine sand and clay. Oxides of iron and manganese are also frequently found in many fractures. All of the copper mineralization is secondary and the ore body is considered to be “exotic” in nature.
The most obvious structural feature at the mine site is the Chloride Copper fault. The fault is normal and has a vertical displacement of about 105 feet and an unknown horizontal displacement. The fault is arcuate to the west. In the NE corner of the pit, the strike is N60E, while on the south side of the pit near an old adit, the strike is N10E. The dip varies from -45 degrees West to -70 degrees West. The fault is young since both the pediment and overlying alluvium are faulted.
An unseen major structural feature in the area is the Sacramento Fault, which, according to projections from the nearby Chloride Mining District, must lie about 2,000 feel west of the pit. It is a normal fault with an estimated vertical displacement of 3,165 feet and a horizontal displacement of 1,830 feet.
The restart of operations at the Chloride Copper Mine is predicated on the readily available copper in the blasted pit bottom, supplemented by pre-stripped reserves in other areas of the fully developed pit as outlined in the 825 series of mine plans, attached. These reserves host an estimated 11 million pounds of recoverable copper.
Following completion of the 825 pit, a second series of plans based on a $3.50 copper price will be activated, which will entail a major push back on the west/southwest side of the pit to expose another 978,231 tons of copper ore grading 0.67% copper. This material is exposed presently in the west face of the open pit and extends to the west of the pit where it is covered by approximately 125 ft of overburden.

SIRG is in the process of updating plans and transferring the permits.
Aquifer Protection Permit #P-101846 (ADEQ) issued June 4, 1993 for life of the project
Air Quality pending Class II Source (ADEQ) filed Dec.5, 1995, amended December 21, 1995
ADEQ-Mining Plan of Operations MPO 388-K-03 issued Dec., 1988, Life of Mine Revised October 15, 1993
Notice of Restart
ADEQ Air Quality (pending) Dec. 5, 1995 (most probably not required)
ADEQ APP Dec. 22, 1995
BLM Dec. 5, 1995
NPDES Storm water runoff discharge AZR00B094 issued April 4, 1996 (US E.P.A.)
Empty haul trucks will be loaded by a front end loader from the pit.
Truck loading and heap building will be accomplished on the same schedule as the mine operations. Three 55 ton capacity trucks will work a three shift, five days per week schedule to haul 15,000 tons per week of ore to the leach pads .
We anticipates that only two of the three trucks will be required for the transfer of cured ore to the pads and one will be held in reserve as a spare.
Ore will be placed on existing and newly constructed leach pads. The new pads will have an impermeable plastic liner (60 mil HDPE) underlain by a graded and compacted base. Engineered fill will be necessary to level the site to provide proper drainage from the heaps to the pregnant solution pond.
Ore will be stacked five days a week at a rate of 15,000 tons per week. Ore will be stacked to a depth of 20 feet and assuming a bulk density of 100 lbs/ft3 will cover an area of 120 ft x 120 ft. The surface of stacked ore will be leveled by dozer. When a panel is completed, the ore will be irrigated with raffinate (barren leach solution) containing 9-10 grams of sulfuric acid per liter.
Leach solution application will be based on a cell irrigation concept using drip emitters to minimize evaporation. A completed panel will measure approximately 120 feet across and will cover the full width of the pad. It is estimated that each panel will hold approximately two weeks of ore production, or 30,000 tons.
Raffinate solution containing 9-10 grams of sulfuric acid per liter will be applied to the ore. Leach solution application will be at the rate of 0.005 gallons per square foot per minute. It is most important to control flows to insure that optimal grade of copper is contained in the pregnant solutions which discharge from the heap to allow maximum copper production in solvent extraction and electro-winning segments of the process.
The plant is designed to process 1.6 grams of copper per liter of pregnant leach solution (“PLS”) at a discharge flow rate of 900 gallons per minute. The initial discharge from a new panel will be significantly higher grade than this, however, as the ore leaches over its 45 day leach cycle, grade in the PLS begins to decline lowering the average grade from the entire heap.
The project will have a number of panels leaching at the same time at various stages of their cycle. However, the objective is to carefully control the discharge grade to average 1.6 grams per liter of copper, the optimal design.
The ore will consume six pounds of sulfuric acid per pound of copper produced. The first 586,000 tons of ore to be mined from the pit is already blasted and has been acid exposed some years ago. It has been flooded for the last few years and we expect acid consumption to be significantly less during the first 18 months of the operation, and thus significantly improving operating costs during this period.
Leach solution will be pumped through a main header along the perimeter of the leach pad to lateral lines which distribute the solution to a series of drip emitters on each individual panel. The main header is installed as a permanent line designed to handle the maximum anticipated pressure and flow. The remainder of the application piping and drip emitter lines will be installed as a temporary system to be moved as new lifts are added to any individual panel. High density polyethylene (HDPE) pipe is used for irrigation piping. Primary leach line spacing is 25 feet apart. Drip emitters are spaced every four feet and cover the entire panel.
Pregnant leach solution (PLS) flows from the toe of the leach heap to a lined pond and will contain an average of 1.6 grams of copper per liter when the acid cure system commences operation. Approximately 0.3 grams per liter of copper is contained in the raffinate and is re-circulated to the heap. In the solvent extraction process, for each pound of copper extracted, 1.5 pounds of sulfuric acid is re-generated for re-use in leaching. The PLS becomes the feed to the solvent extraction plant. It flows to the plant by gravity at the rate of 900 gallons per minute.
The solvent extraction plant operation concentrates copper values from the pregnant leach solution (PLS) containing approximately 1.6 grams of copper per liter into a high purity solution containing approximately 43 grams of copper per liter, known as strong electrolyte. This is the final product of solvent extraction and is the feed to the electro-winning plant.
The leach solution percolates through the leach heap and dissolves the copper as a soluble copper sulfate in water. The primary leaching of the copper will occur in the acid cure step in the mine prior to moving the ore to the pads. When the raffinate is then applied to the ore, it dissolves the copper and it discharges to the PLS pond. The impounded PLS flows by gravity to the extraction step of the solvent extraction plant. Following filtration, it is mixed with an organ oxime reagent suspended a kerosene at a ratio of one part PLS (aqueous) to one part organic. The organic contains a concentration of 6%-7% reagent in kerosene.
The copper in the aqueous phase replaces two protons in the organic phase causing the copper to be transferred to the organic phase. The proton or acid is transferred to the copper stripped aqueous phase and is returned to the leach cycle as raffinate. Again, for each mole of copper extracted, 1.5 moles of sulfuric acid is re-generated. The copper extraction phase takes place in two parallel mixer-settler units. The organic and aqueous phases are separated by gravity in a settling tank and the organic is skimmed off into a launder and flows to a loaded organic holding tank. From this tank, it is pumped to the second stage of solvent extraction, the stripping circuit.
In the stripper mixer box, the loaded organic is mixed with a lean, acid rich electrolyte that comes from the electro-winning plant after copper has been electro-plated from the solution. In the stripping circuit, two protons from the electrolyte replace copper on the organic reagent and the copper transfers from the organic phase to the aqueous phase to re-generate rich electrolyte which is the feed to the electro-winning plant.
The rich electrolyte flows by gravity to a strong electrolyte tank where air is blown through the solution to remove entrained organic by frothing and skimming. Recovered organic is returned to the organic tank for re-use. The stripped organic is skimmed off the stripper settler and flows by gravity to the two extractors for re-use. The strong electrolyte is then pumped through an anthracite/garnet filter as a final cleansing stage before being pumped to the electro-winning plant for copper plating.
The ‘polished’ electrolyte from filtration will feed an electrolyte surge tank. The rich electrolyte is combined with lean electrolyte return from the tank-house to form the re-circulating electrolyte or strong electrolyte feed to the electro-winning plant.
The strong electrolyte is pumped to the electro-winning plant and feeds equally to 16 polymer concrete electro-winning cells. Each cell contains 37 rolled lead-calcium anodes and 36 316-L stainless steel cathodes. Each cell is connected in series and the cathodes connected in parallel to a rectifier capable of maintaining 24 to 25 amps per square foot of cathode area. A voltage drop of 2.1 to 2.3 volts per cell is experienced. Cobalt sulfate levels of about 100 ppm will be maintained in the electrolyte to prevent excessive spalling of the lead anodes.
The leaching, solvent extraction and electro-winning process continue un-interrupted year round. Electro-deposition of copper is continuous and cathode growth to maturity is a seven day cycle.
At the end of the cycle, or once every seven days, the cathode is pulled from the cell using an overhead crane, taken to a stripping bay where the copper is removed from the stainless sheet as a sheet of copper weighing approximately 100 pounds and containing 99.998% purity. The cathode sheet is manually removed from the stainless sheet, falls to a transfer conveyor and is transported to a stacker. The copper sheets are stacked into bundles weighing approximately 3,000 pounds of copper per bundle, strapped, sampled and prepared for shipment. One cathode from each bundle is sampled to verify purity.
When a shipment of 48,000 pounds has been accumulated, the bundles are loaded onto a flatbed truck for shipment.
The Chloride Copper Mine Project is designed and constructed to Best Available Demonstrated Control Technology (BADCAT). All pads and ponds will be lined and have leak detection for early warning in the event of leakage.
The SX/EW plant is constructed with secondary containment as is the tank farm. Settlers are constructed of concrete with stainless steel liners as is the tank farm. All settlers and tanks have leak detection every four feet. The electro-winning cells are constructed of polymer concrete and sit on pedestals so that leakage is readily apparent. The electro-winning floor is contoured to a sump where any spilled solutions can be pumped back to the raffinate pond for re-circulation.
The Project will be permitted and with some minor modifications is ready for re-start. Since it is not a point source for air bourn contaminants, an air quality permit is not required.
A revised plan of Operations was filed in FEb of 2012 with BLM, Kingman and a Reclamation Plan and reclamation bond is anticipated prior to start of operations.
The following positions at the mine will be filled.
Plant Superintendent, Misc. Equipment Operator, 2 mechanics, 2 equipment servicemen, 1 repairman, 1 plant operator and 4 plant helpers.
Desert Construction will supply their own employees to operate their equipment.
After year one, waste stripping will add $0.10 per pound of copper, however, this will be somewhat offset by the processing of 350,000 tons of stockpiles grading 0.34% copper.
Following year one, when the 589,000 tons of ore in the pit bottom and the 350,000 tons of stockpiles are mined out, drilling and blasting will add another $0.20 per ton of ore mined, or another $12,000 per month and $0.027 per pound of copper produced.
If costs are carefully controlled, the operating cost should hold for the life of the project, resulting in a profit margin of approximately $2.00 per pound of copper at $3.30 sales price per pound.

