MPO for the mine 10-16-2012 - READ IT SO YOU KNO
Post# of 4018
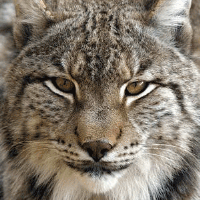
MPO for the mine 10-16-2012 - READ IT SO YOU KNOW AND UNDERSTAND - We don't know the revisions but this is probably the MPO that was accepted in July. Buzz says now it is 95 pages and this is only 30 pages!
THE BIG QUESTION IS WHY IS IT ONLY GOOD FOR THREE YEARS??
List of Figures
1-1 Location Map
1-2 Claims Map
1-3 Pre-1955 Status Claims
1-4 Generalized Regional Geology Map
1-5 Site Area Geology Map
1-6 Groundwater Contour Map for Chloride Copper Project Area
1-7 Locations of Monitoring Wells and Private Wells
1-8 Right-of-Ways
1-9 T.23 N., R18 W., of GLA and Salt River Meridian, Arizona
2-1 Historical Mining Footprint
2-2 Limits of Planned Mining
2-3 General SX/EW Flow Chart
2-4 Conceptual of SX/EW Plant Process
3-1 Location of Groundwater Monitoring Wells
3-2 Mine Reclamation Plan Layout
List of Tables
Table 1. List of Mineral Claims………………............................................................................................... 9
Table 2. Assay Values of Phase I In-Situ Leaching………........................................................................... 13
Table 3. Assay Values of Phase II Preshot Core....................................................................................... 14
Table 4. Production Record by Arimetco (1992-1993)....................................................................……… 16
Table 5. Temperature Ranges for Kingman, Arizona............................................................................. 17
Table 6. Production Schedule................................................................................................. 25
Table 7. Major Mining Equipment........................................................................................................... 27
Table 8. Staffing Plan............................................................................................................................... 28
Table 9. SX/EW Reagents....................................................................................................................... 30
Appendices
Appendix A. Agreements
Appendix B. Road Documentation
Appendix C. Claims
Appendix D. Geology & Mining History
Appendix E. Permits /Applications Submitted
Appendix F. Biological Resources Report (TBP)
Appendix G. Cultural Resources (TBP)
Appendix H. Financial Assurance Cost Estimate
Appendix I. Plot Plan
Appendix J. Use and Occupancy Request
LIST OF ACRONYMS AND ABBREVIATIONS
ACRONYMS
ADEQ Arizona Department of Environmental Quality
AG Acid Generating
APP Aquifer Protection Permit
ARD Acid rock drainage
BADCT Best Available Demonstrated Control Technology
BLM Bureau of Land Management
BMP Best Management Practices
CDWID Chloride Domestic Water Improvement District
CESQG Conditionally Exempt Small Quantity Generator
CFR Code of Federal Regulations
DES Department of Economic Security
DOT Department of Transportation
EIM Emerald Isle Mine
EPA Environmental Protection Agency
EW Electrowinning
GCL Geosynthetic Clay Liner
HDPE High-Density Polyethylene
ILS Intermediate Leach Solution
IO Isolated Occurrence
IP Induced Polarization
M Magnitude
MCE Maximum Credible Earthquake
MGS Mining Geophysical Surveys
MPE Maximum Probable Earthquake
MPO Mine Plan of Operation
MSHA Mine Safety and Health Administration
NAAQS National Ambient Air Quality Standards
NAG Non-Acid Generating
NFPA National Fire Protection Association
NEPA National Environmental Policy Act
NRHP National Register of Historical Places
PLS Pregnant Leach Solution
PMA Pollutant Management Area
POC Point of Compliance
PVC Polyvinyl Chloride
RCRA Resource Conservation and Recovery Act
ROW Right of Way
RQD Rock Quality Designation
SGV SGV Resources Incorporated
SIERRA Sierra Resource Group Incorporated
SPCC Spill Prevention Control and Countermeasure
SWPPP Storm Water Pollution Prevention Plan
SX Solvent Extraction
TBD To Be Determined
TCu Total Copper
TSC TSC Enterprises Incorporated
TSS Total Suspended Solids
UNSE UniSource Energy Services
USBM United States Bureau of Mines
ABBREVIATIONS
cf cubic feet
cm/s centimeters per second
Cu Copper
Cu-Mo Copper-Molybdenum
cy cubic yard
in. inch
ft. feet
gpm gallon per minute
lbs. pounds
m meters
mg/l milligrams per liter
kV kilovolts
kVA kilovolt-amperes
mph miles per hour
sq. square
pcf pounds per cubic foot
T tons
V volts
Zn Zinc
Purpose and Scope
This Mine Plan of Operations (MPO) describes the proposed mine activities at the Chloride Copper Mine Project (hereinafter referred to as the Project) & historically known as the Emerald Isle Mine (EIM) proposed by Sierra Resource Group, Inc. (SIERRA). The purpose of this MPO is to present the following:
Present the contemplated plan of operations for the restart of the mine.
Present the plan for reclamation that is integrated into the mine operation.
This Plan of Operations is submitted to comply with 43 CFR 3809, Surface Management for Unpatented Mining Claims and Sites Situated on Land Administered by the Bureau of Land Management.
Project Overview
The Chloride Copper Mine Property (Property) is located in Mohave County, Arizona, approximately 30 miles northwest of the city of Kingman, Arizona. The total area held by SIERRA for the Project Property amounts to approximately 154 acres on BLM and an option to purchase 90 acres of private property directly to the south. The geographic coordinates of the Property are 35° 21’ N Latitude and 114° 10’W Longitude (T22 and 23 and R18). The Property consists of 37 unpatented lode claims and 14 mill-site claims (Figure 1-2) in Section 22 & 27, of Township 23N, R18W, within the Hualapai Mining District. The area has been extensively disturbed by past mining and exploration, beginning in the 1910s and sporadically until the 1990’s.
Figure 1. Site Vicinity
Within this project boundary there are a total of 154 acres administered by the Bureau of Land Management (BLM) and an optional 90 acres of private land. The proposed BLM land to be mined during this project totals 36.12 acres. This land consists of previously disturbed land due to past mining and mine support work, including facilities, tailings dams, ponds and abandoned equipment. The pit will be developed in 3 phases, consisting of both high and low grade ores to be blended together. Sierra proposes to excavate about 1,935,336 tons of materials from the 36.12 acres of BLM land and 0 tons of material from the proposed private land for a total of 1,935,336 tons total.
A summary of the acreages of BLM land and private land, by use, is provided in Table 1.0.
Table 1.1 Acreages of the Chloride Copper Mine
Description BLM Land
(acres) Private Land
(acres) Total Acres
Project Boundary 154 90 244
Previously Disturbed 157 0 157
CCM Proposed Mine Area 36.12 0 36.12
Total Reclaimed 36.12 0 36.12
The copper recovery system that will be utilized on the project is the Solvent Extraction/Electro-Winning (SX/EW) process. This will include the use of a portable cone crusher, various screens, conveyors, agglomerator, stripping units and a tank house. The stripping unit and the tank house are already constructed on the site. Excess barren rock from the overburden, crushing and screening process will be stockpiled and the materials will be utilized as material for reclamation.
Table 1.1.2 – Production Schedule (Note it is for 3 years with an estimated total of copper produced at 12,195,108 lbs.) At $3.40 that equates to $41,463,367. Cost to produce a lb is estimated at $1.25 comes to $15,243,885. That equates to a profit of roughly $26MILLION for 3 yrs of operation.)
SOMEONE SHOULD ASK ROD WHY THE MPO IS FOR ONLY THREE YEARS!
Year
1 2 3 Total
Tons Ore 480,813 448,987 455,427 1,385,227
Tons Waste (Minimal) 183,370 183,370 183,370 550,109
Ore Grade % Copper 0.53 0.57 0.55 0.55
Copper Recovery % 0.7198 0.8414 0.8414 0.8
Copper Produced Pounds 3,678,179 4,299,552 4,217,377 12,195,108
Figure 2. Legal description
Table 1.1.3 - Mine Phases
Excavation Phase/Years Property Ownership Size
(acres) Township 23 North, Range 18 West, Section 22 & 27
Phase 1/Year 1 BLM 10.56 NE ¼ and SW ¼
Phase 2/Year 2 BLM 5.28 NE ¼ and SW ¼
Phase 3/Year 3 BLM 5.28 NE ¼ and SW ¼
Work will begin as soon as all necessary permits have been obtained and equipment can be mobilized. The operation, including reclamation, should be complete within three to four years from start-up. Occupancy, as defined in 43 CFR 3715, will occur on BLM property and is requested in Section 9.0 of this Plan of Operation.
OPERATION COMPLETE IN THREE YEARS?? WHAT HAPPENED TO THE 10 YEARS THAT RIZZO ESTIMATED??
The Project is designed and will be operated to minimize potential direct, indirect, and cumulative impacts related to the resources discussed below. Table 1.1 shows resources with potential to be impacted by the Project, and the development and operating practices that will be used to minimize those impacts.
Table 1.1 – Environmental Protection Practices Review
Potentially Affected Resource Practice
Socio-economics Hire from local area workforce where possible
Air Implement dust control measures such as road watering and treatment. Dust from crushing & screening at the process site will be controlled by water sprays.
Water Install storm water diversions and controls to minimize erosion and sedimentation.
Use any mine water encountered for dust control.
Store fuel, lubricants and solvents with secondary containment on private land.
Clean up spills immediately.
Recycle ~50% of the water at the process site.
Land/Soils Use existing roads for access to site.
Stockpile topsoil for revegetation.
Vegetation Minimize new disturbance to limit vegetation damage.
Wildlife Minimize new disturbance to limit habitat degradation.
Off-site water will be provided.
Special Species Status
Train workers to recognize and protect special status species.
Reclaim a portion of habitat disturbed by a previous operator.
Visual Resources Remove temporary structures;
Waste rock to be returned to mine area.
Re-grade disturbed areas to a depth of 2 feet to blend with topography during reclamation.
Remove processing equipment
Cover historic tailings with soil material.
Livestock
Minimize new disturbance.
Cattle, if present, will not be excluded from the Project area.
Off-site water will be provided.
Cultural Resources Avoid known cultural resources.
Train workers to recognize and avoid cultural resources.
If previously unknown cultural resources are found, isolate the area and obtain clearance before proceeding.
Recreation/Public Safety Minimize new disturbance. Exclude public only from operations area.
1.0 Claimant - Operator, Mineral Materials Request
1.1 Claimant and Operator Information
Sierra Resource Group Inc.,
9550 S. 77 Eastern Ave, Suite 253
Las Vegas, Nevada 89123
(702) 462-7285.
Project Contact:
Mr. Travis M. Snider
Senior Vice President of Operations
Sierra Resource Group
(602) 672-0598
SIERRA’s Federal Tax Identification Number is: 88-0413922
SIERRA is a U.S based mining company, headquartered in Nevada, and is committed to the exploration, discovery and development of gold, silver, copper and other mineral resources. SIERRA Inc. is a publicly traded company, (STOCK SYMBOL: SIRG) and holds mining properties and mineral claims in Arizona and is looking to expand throughout the Americas in the near future. Sierra is committed to exploring responsibly, maintaining environmentally friendly policies while impacting the local economy in a positive manner that will allow its shareholders to take pride in their investment.
2.0 Location, Access, Claims, Land Use
2.1 Location
The Chloride Copper Mine Property (Property) is located in Mohave County, Arizona, approximately 30 miles northwest of the city of Kingman (Figure 1-1). The street address for the mine is 8000 North Boulder Dam Highway, Chloride, Arizona. The geographic coordinates of the Property are 35° 21’ N Latitude and 114° 10’W Longitude (T22 and 23 and R18). The Property consists of 37 unpatented lode claims and 12 mill-site claims (Figure 1-2) in Section 22 & 27, of Township 23N, Range 18W, of the Gila-Salt River Meridian. The property is within the Hualapai Mining District, which has been extensively disturbed by past mining and exploration, beginning in the 1910s and sporadically until the 1990’s.
2.2 Access
Access to the Property is by U.S. Highway 93, from Las Vegas, Nevada or from Kingman, Arizona. Logistical support, in terms of power and telephone lines, is available from Kingman, which is linked to the Arizona Power grid. Water is available from wells near the Property and through purchase from other sources. Active and past mining is present in the Hualapai Mining District. Mining personnel are available from the community and mining equipment is available from Kingman, Las Vegas, and Phoenix.
The northern wells are accessed by an existing road along a wash for approximately 1.25 miles to Well No. 1 and 1.5 miles to Well No. 2 from the Old Boulder Highway. PAT-1 is accessed by an existing road approximately .75 miles from the Old Boulder Highway. The proposed water line from the east side of the site is accessed by an existing road as well.
2.2.1 Roads
The historic mine access road off of Boulder Dam Highway has been in use for many years to support the mine. It has had a locked gate at the entrance of the property to protect the public from hazardous areas since the early 1990’s. The existing dirt road averages 16 feet in width but needs to be graded. Documentation of the current, existing widths and layout at 1000 foot intervals along the road are provided in Appendix B. The natural setting along the roads is similar to that of the mine site.
In addition several other roads exist in the mining site area and in the mine. These roads were developed during the last time the property was in operation to support it. These roads will be utilized to access the pit, tailings area, new heap leach, facilities and the monitoring wells located around the pit.
2.3 Electrical
The electrical power supply for the Project facilities falls within the UniSource UNSE territories. Access to the interconnect is located on the eastern side of the Chloride Copper Project. A 69 kV power line will be brought to a substation located near the SX/EW plant where the original substation was located (Figure 1-7). The 69 kV line will be supported with standard power line wooden poles with proper heights to account for topography. In addition to the 69 kV line, a 12 kV line is proposed to supply power to wells north of the site (Figure 1-8). This 12kV line will also be constructed using standard wooden poles.
A new substation is planned to be installed and located near the SX/EW plant. The substation will receive the 69 kV line. A primary step down transformer will reduce the power load to 12.47 kV, and a secondary step down transformer will reduce the voltage to 480 volts (V). A ROW application will be made for UNSE to provide single-phase power to the northern supply wells by either a connection from the existing power distribution line east of the wells, or from the distribution line along the Old Boulder Highway approximately west of the wells. Should this application be denied, SIERRA will install a separate 12.47 kV line to run from the substation to the location of the supply wells. A local secondary transformer at the wells will step down the voltage as required by the supply pumps. The estimated power load will be approximately 1,400-kilovolt amperes (kVA).
2.4 Water
The Chloride Copper Mine has one well on site and three wells off site. That can supply the mine adequate amounts of water. If necessary, SIERRA may enter into an agreement to purchase water from the Chloride Domestic Water Improvement District (CDWID). The water line that supplies the town of Chloride and is owned by the CDWID is located less than a mile west of the mine site along the Old Boulder Dam Highway. Based on a design done by Paul Rizzo and Associates the make-up water use for the site is 63 gpm. This design is based on the use of a drip system for the heap leach as opposed to the much more water consumptive wabbler or sprinkler systems.
2.5 Rights of Ways
A series of BLM Rights of Way (ROW) will be applied for bringing utilities to the Chloride Mine site. The current plan for the water supply lines is to re-establish or establish an existing water supply line (Figure 1-7). These include:
3.5-mile pipeline for the northern two wells will be modified under previous ROW AZA-00740.
Additional water supply lines will be utilized and are described in Section 2.7.1. These sites exist within the existing claim block and they include:
6,000 ft. pipeline for the possible supply well east of the mine site. This well is identified as Well No. 352158114103501 and is shown on Figure 1-7. A purpose and need for ROW is in the process of being filed by SIERRA.
5,500 ft. pipeline to connect to the town of Chloride water supply line.
50 ft. pipeline to connect to the PAT-1 and 2 wells pipeline from the R-2 well.
For electrical power supply, a number of changes will be implemented regarding the UNS Electric, Inc. (UNSE) ROW. The UNSE ROW near the Chloride Mine site are as follows (Figure 1-8):
ROW AZA31567 will be decommissioned by UNSE.
ROW AZPHX 34352 will be decommissioned after the 69 kV power source (ROW AZA33319 is connected to the Chloride Mine.
ROW AZA33319 carries a 69 kV power line. The ROW enters the site from the southeast and terminates at the proposed location of the substation. UNSE intends to modify the alignment to avoid interfering with mine operations. The realignment will remain within the pre-1955 claims.
ROW AZA 20658 may be decommissioned if an alternate source of power can be supplied to the PAT-1 and 2 wells and eastern well.
12 kV Single Phase Distribution Line - The applicant, UNSE, is seeking to acquire a ROW to locate a 12 kV single-phase distribution line on Federal Lands in the Chloride area of Mohave County, Arizona. This line has been requested to feed two water well sites for Chloride Copper Mine operation (fka Emerald Isle Mine). The wells will supply water to the mine via a water line authorized under AZA-00740. The existing three-phase power line in the area that could serve these sites was permitted under AZPHX-034352, but is seriously dilapidated and needs to be removed according to UNSE.
The power line route will be located on public land identified as T. 23 N., R. 18 W., Section 15. Figure 1-7 shows the proposed ROW for the 12 kV line, which is 20 ft. in width, 10 ft. on each side of the route centerline. The line will run north along Old Boulder Dam Highway until reaching the west quarter corner of Section 15, at which point it will run generally northeast until reaching the first well site. The line will then head southeast from the first well site to the second well site. Construction of this new 12 kV line will require 17 new poles on Federal Lands. No fencing, welding, concrete work, grading, permanent foundations, or road building is expected on Federal Lands.
Figure 3. Project Location Map
2.4 Claims
The total area held by SIERRA for the Project Property amounts to approximately 154 acres. Polyvinyl chloride (PVC) pipes and wooden posts mark the unpatented claim corners, end lines, and discovery monuments, most of which have been surveyed. The fee lands are located by legal description at the Mohave County Recorder’s Office. The names, sizes, and designations of the 49 total claims are shown in Table 1. Four of the 49 claims fall under the classification as pre-1955 claims under the amended mining act. Figure 1-3 shows the mine site and existing open pit with the claims superimposed on the image.
Table 1 – List of Mineral Claims
Sierra -Chloride Cooper Property
Claim Name Approx. Area (ha) AMC Number Remark
Copper Hill Mill Site No. 1 1.4 105792
Copper Hill Mill Site No. 2 1.4 105793
Copper Hill Mill Site No. 3 1.4 105794
Copper Hill Mill Site No. 4 1.4 105795
Copper Hill Mill Site No. 5 1.4 105796
Copper Hill Mill Site No. 6 1.4 105797
Copper Hill Mill Site No. 7 1.4 105798
Copper Hill Mill Site No. 8 1.4 105799
Copper Hill Mill Site No. 10 1.4 105801
Copper Hill Mill Site No. 11 1.4 105802
Copper Hill Mill Site No. 12 1.4 105803
Hermes Mill Site No. 13 1.4 105804
Copper Hill No. 1 Mill Site 14 1.4 105805
Copper Hill No. 1 Mill Site 15 1.4 105806
Copper Hill No. 2 5.6 105785 6A55-56 Pre-1955
Hermes 5.6 105786 6A62-64 Pre-1955
Hermes No. 2 5.6 105787 6A63-64 Pre-1955
Jimtown Copper No. 1 5.5 105788 Pre-1955
Valley Copper No. 1 4.2 105789 Overstaked
Valley Copper No. 2 5.6 105790
Valley Copper No. 3 5.6 105791
Emerald No. 1 2.8 339597 Overstaked
Emerald No. 2 5.6 339598
Franklin D. Roosevelt 5.6 90056
Subtotal Old Claims 71.3
Emerald # 1A 5.6 364261
Emerald # 2A 5.6 364262
Emerald # 3 5.6 364263
Emerald # 4 5.6 364264
Emerald # 5 5.6 364265
Emerald # 6 5.6 364266
Emerald # 7 5.6 364267
Emerald # 8 5.5 364268
Emerald # 9 5.6 364269
Emerald # 10 2 364270 Overstaked
Emerald # 11 4.9 364271 Overstaked
Emerald # 12 0.1 364272 Overstaked
Emerald # 13 5.5 364273 Overstaked
Emerald # 14 2.2 364274 Overstaked
Emerald # 15 5.6 364275
Emerald # 16 4.2 364276 Overstaked
Emerald # 17 5.6 364277
Emerald # 18 2.8 364278 Overstaked
Emerald # 19 5.6 364279 Overstaked
Emerald # 20 2.7 364280 Overstaked
Emerald # 21 5.5 364620 Overstaked
Emerald # 22 3 364621 Overstaked
Emerald # 30 0.1 364622 Overstaked
Emerald # 31 5 364623
Emerald # 43 1.4 364624
Emerald # 44 0 364625
Emerald # 45 0 364626
Subtotal New Claims 106.6
Total 177.9
2.5 Land Use
The project area is not zoned by Mohave County. There are five residences located within 1.0 miles of Chloride Copper Mine Project and several other mining operations in the nearby area. The predominate landowner in the area is the United States Government with the land administered by the Department of Interior, Bureau of Land Management (BLM). The lead agency for this project is the BLM, Kingman Field Office, located in Kingman, AZ.
Historically, the land has been utilized for mining, recreation and rangeland which are the primary uses today. Historic mining activities in the Hualapai District of northern Arizona date back to the early 1860s, mostly for silver and gold within oxidized portions of veins. By the early 1900s, mining companies started to explore for base metals. Remnant mine workings in the area include lumber, nails, concrete lined settling ponds, tailing piles, structural remains, concrete, scrape metal and disturbed areas on the claims.
3.0 Geology
3.1 Regional Geology
The Chloride Copper Mine Property is located within the north-northwest trending Sacramento Valley. The mountains surrounding the Sacramento Valley consist of igneous and metamorphosed Precambrian complexes, younger intrusives, and volcanic deposits (Figure 1-4). The volcanics include basalt flows, basaltic andesite flows, and rhyolite tuff that range in the age from Cretaceous to Quaternary.
The alluvial deposits of the Sacramento Valley have been divided into older, intermediate, and younger units by Gillespie and Bentley (1971). The older alluvium is of Tertiary age and consists of semi-consolidated fragments of granite, schist, and gneiss interbedded with volcanics. Intermediate alluvium of Pliocene to Pleistocene age overlies the older alluvium and is also composed of semi-consolidated rock fragments. The younger alluvium is of Holocene age and consists of surficial deposits that have been further divided into piedmont and stream deposits (Gillespie and Bentley, 1971). Piedmont deposits consist of MPOrly consolidated rock fragments similar to the older alluvium along with some caliche layers. The deposits overlie terraces, alluvial fans, and pediment slopes, as well as the valley floor.
The Chloride Copper Mine Property is located near the Mineral Park porphyry copper-molybdenum deposit, within the Wallapai Mining District on the western flank of the Cerbat Mountains (Figure 1-5). The Cerbat Mountains trend north and are composed of Precambrian basement rock intruded by a Cretaceous (Laramide) quartz-monzonite porphyry. Tertiary extrusive rocks crop out on the flanks of the Cerbat Range (Eidel et al., 1968). The north trending Black or River Range west of the Cerbat Mountains consists of Cretaceous and Tertiary volcanic rocks overlying a MPOrly exposed metamorphic basement complex.
The Wallapai Mining District is approximately 4 miles wide and 11 miles long and is defined by the known lateral extent of base and precious metal veining. Faults are abundant in the District, but the lack of good marker units makes offset and age relationships difficult to interpret (Wilkinson et al., 1982).
Several large N70°W trending faults are present in the area from Roper Ridge to Ithaca Peak and numerous smaller northwest trending faults exhibit intense fracturing and silicification. The geology of the Wallapai District is summarized as follows:
A series of folded metasedimentary and metavolcanic rocks occur along the western flank of the Cerbat Mountains.
The folded rocks were intruded by regionally northeast-foliated granitic gneiss of batholithic proportions.
The north-northwest trending contact between the folded rocks and the granitic gneisses is a major structural feature in the district.
Intrusion of the Ithaca Peak stocks at or near the intersection of this contact and the Turquoise Mountain fold.
The Ithaca Peak intrusion contact was the locus for intrusion of rhyolite dikes and the formation of the major veins within the District (Wilkinson et al., 1982).
Figure 4. Topography
3.2 Local Geology
The Chloride Copper Project is located in an alluvial fan about one mile west of the western slope of the Cerbat Range (Figure 1-5). The alluvium is underlain by the Late Tertiary Gila Conglomerate and Cretaceous granitic rocks of the Ithaca Peak intrusive. The trace of fold axes also suggests that the Property area is at least partly underlain by northeast trending basement amphibolitic rocks. To the south, the relief is low and undulating due to protruding bedrock and erosion of the pediment surface. The alluvium in the vicinity of the old mine represents older alluvium, as does the alluvial fan apron flanking the range (TSC, 1992).
The dissected alluvial fan reveals MPOrly sorted, mixed deposits of angular to sub-angular sand, pebbles, cobbles, and boulders (up to 15 ft.), representing all the rock units in the Cerbat Range. Crude stratification exists in some places, but the bulk of the fan flanking the range is largely mixed and unconsolidated.
The alluvial veneer at the Chloride Copper Project has been partially consolidated by mineralizing solutions to form the blanket of copper mineralization. Due to its proximity to the Mineral Park Copper-Molybdenum (Cu-Mo) deposit, the salts and clays eroded from the Ithaca Peak porphyry alteration halo likely have contributed to the bonding of the Gila Conglomerate.
The most obvious structural feature on the Property is the Emerald Isle Fault. The Fault is a range front, dip slip (normal) fault related to the Basin and Range structural province. The fault has a major measured displacement of approximately 105 ft. down to the west. Horizontal displacement is unknown and expected to be minimal. In the northeast corner of the pit, the strike is N60E, while on the south side of the pit near the old adit, the strike is N10E. The dip varies from -45° west to -70° west. The fault has sustained late Quaternary movement since both the pediment and overlying alluvium are faulted (TSC, 1992).
Chloride Copper Mineralization
The Property is located on Quaternary alluvial fan deposits. The Quaternary alluvial fan deposits are underlain by the Late Tertiary Gila Conglomerate and Cretaceous granitic rocks similar to those present at the nearby Mineral Park Mine.
There are three types of copper mineralization at Chloride Copper Mine site. The first type is primary fissure vein mineralization containing copper sulfides. This was the type of mineralization which was mined in 1917 and 1918, but which is no longer the target. The second (and the main) type is primary copper mineralization within the dark conglomerate reported to consist primarily of tenorite (CuO). The third type is secondary copper mineralization, in the form of copper staining, such as malachite (CuCO3·Cu(OH)2) and chrysocolla (CuO·SiO2·H2O), which are commonly observed on fracture planes as well as within the matrix of the dark conglomerate and overlying lower alluvium.
Copper mineralization at Chloride Copper is hosted by the Gila Conglomerate. The copper zone is in the form of a mineralized lens contained within a paleochannel some 2,500 ft. long, 500 ft. to 750 ft. wide. The thickness ranges from 20 ft. to 300 ft., averaging about 100 ft. In places, the conglomerate is absent and in other places, it is very thick, due to the north trending Emerald Isle Fault.
The source of the copper present at the Chloride Copper Mine site is interpreted to be the low grade porphyry-type copper mineralization at Alum Wash, about 3.5 miles northeast of the Emerald Isle deposit, and mineralization is characterized by dark blue to black rock.
In this respect, the style of mineralization appears to be somewhat similar to the Exotica deposit, a copper oxide satellite deposit related to the extensive Chuquicamata copper deposit in Chile.
4.0 Description of Operations
Copper oxide ore will be processed using heap-leaching technology (Figure 2-4). Copper sulfate in solution will be processed through the existing SX/EW plant. Metallic copper will be recovered by EW. Metallic copper will be produced from the copper sulfate solution in the form of high purity, cathode copper plates, which will be loaded onto trucks for shipment to market.
4.1 Operations
Mining and heap pad construction will proceed 10 to 12 hours per day, 5 days per week. There will be no mining at night and no mining is anticipated currently on the weekends. Eight equipment operators, 3 haul truck drivers and a supervisor will work the shift. Typical equipment to be used is listed in Table 2, below. Equipment could vary slightly. Mine equipment will be diesel-fueled and filled from on-site tanks. Pick-ups and on road haul trucks will be fueled off-site at commercial stations.
Table 7 - Major Mining Equipment
Equipment Fleet Size
50-100-T Mine Haul Trucks 3
Cat 992D Wheel Loader 2
Cat 320 BL Hydraulic Excavator 1
Light Duty Grader (140 Class) 1
Small Dozer 1
10-T Forklift 1
5,000 Gallon Water Truck 1
Portable crushing and screening unit 1
D-8 N Dozer 1
Pick-ups 2
Sub-Total Mining Equipment 14
Figure 5. Process Diagram
Possible permits for the mine site and their status is:
Aquifer Protection Permit (APP): Sierra has applied for an APP from the ADEQ (Appendix E). Upon receipt of the determination, the operator will provide a copy to BLM.
Air Quality Permit: Sierra is in the process of having CDM Smith start the Air Quality Permit process. It is anticipated that ADEQ will grant another A Negative Determination of Permit Applicability, as ADEQ has issued for this project previously.
Arizona Pollutant Discharge Elimination System (AZPDES) General Permit for Storm Water Discharges Associated with Industrial Activity – Mineral Industry to Waters of the United States 2010 (MSGP 2010). There is an existing permit and the process to transfer it is underway by CDM Smith.
Army Corps Of Engineers (ACOE) Section 9, 404 Permit of the Clean Water Act. SIERRA will submit a Preliminary Jurisdictional Determination request to the Phoenix office of the ACOE. This request is to determine if jurisdictional “waters of the United States,” or “navigable waters of the United States,” or both, are either present or absent on a particular site. Documentation from ACOE will be submitted to BLM when received (Appendix E).
4.2 Processing
The existing disturbed footprint of the Emerald Isle Mine (now Chloride Mine) including the access road is approximately 157 acres on Federal Lands managed by BLM (Figure 2-1). It is anticipated that the planned mining by SIERRA will fall within the existing disturbed footprint. The area of planned mining and processing is shown on Figure 2-2.
The Chloride Copper Project will produce more than 4 million lbs. of copper per year (roughly 0.0025 percent of annual U.S. production) for approximately three years. This is also dependent on the price of copper and additional economic factors related to recovery.
(THE SX/EW PLANT CAN PRODUCE 5M LBS A YEAR AND THE PARTS TO EXPAND IT ARE STORED ON SITE.)
Mining will consist of conventional ripping, excavation, and crushing techniques. Waste rock will be transported by haul truck to the waste rock storage areas. The crushed copper oxide ore will be agglomerated with sulfuric acid and then placed on a lined heap leach pad. Leaching solutions will irrigate the ore to dissolve the copper and collect it in a containment pond referred to as the PLS pond. The PLS will be pumped to a SX/EW plant for removal of the copper and plating as a cathode. The cathode copper generated from the SX/EW plant will be transported off site for further processing. Figure 2-3 presents a simplified depiction of the ore mining and processing. The following is a list of specifications related to mining and processing the oxide copper ore.
Approximate pad area: 6.5 acres. (Buzz says this is now 35 acres!)
Mine production rate of < 2,000-T per day.
Ore will be segregated from overburden in upper pit based on block modeling.
Lower grade stockpiled ore from southwestern edge of pit (located on old mine waste pile), existing heap leach pad and old mill tailings will be mixed with high-grade ore.
Truck dump stacking of ore in 15 to 20 ft. high lifts.
Heap leach pad lifts will be constructed as panel amounting to approximately 28,000-T per panel.
10 panels per lift.
150-day leach cycle with a maximum solution application rate of 0.0049 gpm per sq. ft. and an average of 0.0045 gpm per sq. ft.
(This means it will take 5 MONTHS for the copper to leach.) (This is the number I had been searching for.)
Production solution flow of 650 gpm.
No stacking over ore not leached the full leach cycle period.
Average stacked ore density of 100 pounds per cubic feet (pcf).
Solution pond capacity for runoff from the 100-year, 24-hour design storm event, plus 12 hours of solution drains down from the operating heap area.
Minimum BADCT factor of safety values for static and seismic heap stability.
Composite liner system under leach pad areas.
Double-lined solution ponds with leak detection and removal system between liners.
Pond design to allow leak repair without operating shutdown.
Single liner system in emergency storm water ponds.
Gravity drainage from leach pad area to solution ponds.
The makeup water usage for the mining effort shall be around 60 (gpm).
A perimeter fence surrounding the area of operations will be four-strand barbwire livestock fence with warning signs. The fence shall be built to Arizona standards.
A ditch/berm will be placed on the outside of the four-strand barbwire livestock fence at the pit.
SX/EW Reagents
Reagents requiring handling and mixing, as well as the attendant distribution system are outlined below:
Table 9 - SX/EW Reagents
Accelerant Delivered Form Method of Storage Solution Storage Concentration Other Information
Sulfuric Acid (H2S04) Liquid (truck) In tank 93%
Diluent (Kerosene) Liquid (truck) In tank 100%
Extractant (Acorga M5910 or equivalent) Liquid (drums) Drums on pallets Circuit concentration, 6% of organic solution – To be Determined (TBD)
Cobalt Sulfate (CoSO4) Dry crystals in bags or super sacks Bags or sacks on pallets TBD
Guar Dry powder in bags or super sacks Bags or sacks on pallets 10% (mix tank)
Mist Suppressor (FC-1100) Liquid (drums) Drums on pallets
Figure 6 – Process Flow Diagram
2.7.1 Production Plan
The Chloride Copper Project will receive water from multiple sources (Figure 1-7). SIERRA has rights to three historic production wells approximately 1.5, 2, and 2.5 miles north of the mine site; however, only two (Well No. 1 and 2) have serviced the mine in recent years. The third well may be evaluated to determine if it is dry or has collapsed. Based on historical mining records the R-2 well just west of the open pit produced considerable water for production. This well will be evaluated as a source of water for operation. SIERRA is purchasing the private land parcel adjacent to the south of the mine site that has two wells (PAT-1 and PAT-2; however, only PAT-1 is currently producing water. PAT-2 will be evaluated as a possible water source). SIERRA is also negotiating an agreement with the well rights’ owner for improving the well (No. 352158114103501) located east of the mine site. The open pit is within the alluvial aquifer. The amount of groundwater that flows into the open pit is unknown; however, the pit may also be a source of water. If necessary, SIERRA may enter into an agreement to purchase water from the Chloride Domestic Water Improvement District (CDWID). The water line that supplies the town of Chloride and is owned by the CDWID is located less than a mile west of the mine site along the Old Boulder Dam Highway.
Delivery System
An existing pipe delivers water from one of the northern wells to the mine site. There are no plans to replace the existing pipe provided that the pipe is still functional. A temporary above ground high-density polyethylene (HDPE) will be installed to connect the second well to the existing pipeline. If the third well is determined to be usable, the HDPE temporary pipeline will be extended to the third well. Temporary above ground HDPE pipelines of 4-6 in. will be installed to deliver water from the PAT-1 and PAT-2 wells. If feasible, another HDPE line will be installed from the well, east of the mine site, as well as from the R-2 well just west of the open pit. If necessary, another HDPE pipe will deliver water from a connection along the Old Boulder Dam Highway. To the extent practicable, the aboveground HDPE pipelines will be connected in such a way as to minimize the linear footage of HDPE pipe. ROW applications will be submitted for those sections of pipeline crossing BLM land between private land and the SIERRA claims.
The existing pipeline from the northern Well No. 1 to the mine site is a fully functional concrete asbestos pipe. As long as the pipe is functional it will not be replaced; however, if malfunctions or breaks occur, the pipe will be replaced and disposed of following state and federal guidelines for disposal of asbestos.
4.3 Ancillary Facilities
The ancillary facilities necessary to support the Chloride Copper Mine and ore processing operations include an administration building, change house, warehouse with lay down yards, analytical laboratory, a vehicle, and maintenance building. Most of these structures will be pre-manufactured. Also included are fuel and lubricant storage facilities for mine and process equipment.
Figure 7 – Plant Layout
4.4 Water Management Plan
4.4.1 Mine Site
A Storm Water Pollution Prevention Plan (SWPPP) for the Chloride Project will be developed to allow for the management of storm flows during the active mine life. The SWPPP will include storm water management provisions for the open pit, leaching facilities, plant area, waste rock storage facility, and access road.
The Project water management facilities will have sufficient capacity to handle runoff generated throughout the life of the Project for the 100-year, 24-hour storm events.
Closed Systems
For the purposes of the SWPPP, the open pit, the heap leach facility, and the plant site are considered closed systems, with all direct rainfall and local runoff contained on site. In the open pit, rainfall will be collected in a sump and incorporated into the process circuit during active operations. All rain falling on the heap leach pad will be captured and collected by the heap solution collection and drainage system, and then incorporated into the leaching process. A storm water pond designed for a 100-year flood will capture any runoff from the heap leach pad and old mill tailings. It will also capture overflow from the PLS.
Waste Rock Facility
If additional mine waste is added to the waste rock facility, initial perimeter buttresses will be constructed that will be consistent with current reclamation and appropriate Best Management Practices (BMP). As additional waste rock is deposited, the buttresses will progress outward. The buttresses will limit erosion potential while minor diversion channels will be used to direct runoff back to the mine area
4.5 Native Plant Management
Sierra will adhere to the Arizona Native Plant Law. If it is determined that there is an excessive amount of desired plans that need to be removed a salvage plan will be generated. In general the salvage plan may include:
removal and transplanting out of surface disturbance area
removal and salvage by private individuals
removal and salvage by commercial dealers
any combination of the above
4.6 Rock Characterization and Handling Plan
A geochemical testing program will be conducted to characterize the mine waste material removed from the open pit from past operations. It is anticipated that the results of the testing program will indicate that the majority, if not all of the waste rock sampled will be non-acid generating (NAG).
4.6.1 Ore Grade and Characteristics
The Property is located on Quaternary alluvial fan deposits. The Quaternary alluvial fan deposits are underlain by the Late Tertiary Gila Conglomerate and Cretaceous granitic rocks similar to those present at the nearby Mineral Park Mine.
There are three types of copper mineralization at Chloride Copper Mine site. The first type is primary fissure vein mineralization containing copper sulfides. This was the type of mineralization which was mined in 1917 and 1918, but which is no longer the target. The second (and the main) type is primary copper mineralization within the dark conglomerate reported to consist primarily of tenorite (CuO). The third type is secondary copper mineralization, in the form of copper staining, such as malachite (CuCO3·Cu(OH)2) and chrysocolla (CuO·SiO2·H2O), which are commonly observed on fracture planes as well as within the matrix of the dark conglomerate and overlying lower alluvium.
Copper mineralization at Chloride Copper is hosted by the Gila Conglomerate. The copper zone is in the form of a mineralized lens contained within a paleochannel some 2,500 ft. long, 500 ft. to 750 ft. wide. The thickness ranges from 20 ft. to 300 ft., averaging about 100 ft. In places, the conglomerate is absent and in other places, it is very thick, due to the north trending Emerald Isle Fault.
The source of the copper present at the Chloride Copper Mine site is interpreted to be the low grade porphyry-type copper mineralization at Alum Wash, about 3.5 miles northeast of the Emerald Isle deposit, and mineralization is characterized by dark blue to black rock.
In this respect, the style of mineralization appears to be somewhat similar to the Exotica deposit, a copper oxide satellite deposit related to the extensive Chuquicamata copper deposit in Chile.
4.6.2 Excess Rock Characteristics
Excess rock materials will consist of overburden and oversized rock from the excavation. Material that falls into the overburden category is generally non-mineral bearing. These materials will initially be stockpiled on the property and eventually used for reclamation. As the pit progresses, and room is available in the pit floor, these materials may be returned to the pit as backfill or stockpiled in the pit.
4.6.3 Existing Old Mill Tailings
SIERRA is evaluating the possibility of a combined mining and reclamation of the old mill tailings. Until the time the decision is made as to treating the tailings as a source of ore, they will be treated with a dust suppression polymer to control fugitive dust. SIERRA plans to initially cover the northern portion of the mill tailings with clean alluvium. Depending on technical feasibility, the southern 500 ft. of the 1,600 ft. (long axis) of the mill tailings will be mined. Appropriate measures will be taken to suppress any dust generated from processing the southern portion of the mill tailings.
4.6.4 Precipitation Runoff Quality
Precipitation runoff quality will be checked, as described in the SWPPP for each site, by monitoring outfall points for evidence of turbidity or hydrocarbons entering natural water courses.
4.7 Spill Contingency Plan
A Spill Control and Countermeasure Plan (SPCC) will be developed in compliance with the Federal Clean Water Act and provided to BLM upon plan approval. This plan will be maintained onsite at all times.
4.7.1 Mine Site
The only likely spills at the mine site on BLM land are diesel fuel and lubricants. Diesel fuel usage is expected to be about 150 - 200 gallons per day. Fueling of excavation equipment will be completed using a small fuel truck filled at the process site. No fuels, lubricants or other petroleum based products will be stored on BLM property other than what is contained in mobile mining equipment.
Routine servicing and maintenance of equipment will be performed at the site where the equipment is located. Repairs will normally be done at the shop on the private property unless the equipment is immobile, in which case, repairs will be done where the equipment became disabled. Oil changes will be done in the shop area on private land. If oil, lubricants or other fluids have to be drained, a plastic catch basin will be used to prevent soil contamination. Major repairs will be done at the shop or an off-site service facility.
Soil contaminated by minor spills of petroleum products will be immediately shoveled into drums by site personnel, labeled and returned to the process site on private land for short term storage. In accordance with hazardous waste regulations these materials will be disposed of at a licensed, approved off-site facility on a regular schedule. Sierra will keep two empty 55 gallon drums with shovels, booms and mats available for this use. Spills greater than 25 gallons, or spills less than 25 gallons that are not cleaned up in 24 hours, will be reported to the ADEQ at 602-771-2330 and to the BLM Kingman Field Office.
4.8 Fire Plan
Planning for emergencies will be an important part of establishing operations for the Chloride Project. Several types of safety procedures will be prepared prior to start up. These procedures will include a Spill Prevention Control and Countermeasure (SPCC) Plan, an Emergency Response and Contingency Plan, a SWPPP, a Fire Plan, and others. These plans will identify emergency preparedness and emergency contact protocols for reasonably foreseeable situations. As project planning continues to develop, the specifics of the emergency planning process will also advance. In addition, extensive training of personnel and the availability of appropriate equipment and supplies will ensure a successful emergency management program. Staffing for the Chloride Project includes safety, industrial hygiene, and environmental technical professionals. Some of the facilities and equipment for emergency planning include: a fully equipped environmental sampling and spill response station, RCRA-compliant waste storage and accumulation areas, safety and training building, and portable fire suppression unit.
Of special concern will be preventing wildfires. Mine vehicles will be equipped with, at a minimum, fire extinguishers, shovels, and first aid kits. Policies, such as prohibiting parking on top of vegetation, and properly disposing of cigarette butts, will be established and enforced to minimize fire potential.
Adequate and reliable illumination will be installed and maintained for all exits. Battery powered back up will provide a minimum of 60 minutes of illumination and will be standard for all emergency lighting and exit signs. Maintenance inspections will be conducted on a monthly basis. Emergency and exit lighting systems will be tested annually.
Fire and smoke alarms will be installed in all employee work areas. Systems and components will receive inspection monthly. Annual testing and maintenance will be conducted for systems and components. Records of inspections will be kept on site for a minimum of five years.
The National Fire Protection Association (NFPA) established NFPA 10, which is the Standard for Portable Fire Extinguishers. NFPA 10 mandates the type, size, placement, and minimum number of extinguishers required for each building. Fire extinguishers will be installed in accordance with this standard.
4.9 Emergency Response Plan
In the event of an emergency, site personnel will report to the office for instructions from the senior company/contractor person on site. Calling 911 will bring response from the Mohave County Sheriff who will dispatch emergency equipment and personnel. The coordinates of the mine site and process site will be posted at the offices to direct medevac helicopters to the sites. The site has both land line and cellular phone coverage.
4.10 Storm Water Pollution Prevention Plans
A Storm Water Pollution Prevention Plan (SWPPP) for the Chloride Project has be developed to allow for the management of storm flows during the active mine life. This plan will be transferred and updated. The SWPPP will include storm water management provisions for the open pit, leaching facilities, plant area, waste rock storage facility, and access road.
The Project water management facilities will have sufficient capacity to handle runoff generated throughout the life of the Project for the 100-year, 24-hour storm events.
4.11 Surface Disturbance
Road repair and maintenance will be done within the footprint of existing roads. Road work will not exceed 40 feet width, even where the existing road is wider.
The existing mine haul roads (Figure 2-2) and any new haul roads will be consistent with BADCT Standards. They will be constructed around the east and south edges of the upper open pit limits. Temporary haul roads will be constructed internal to the upper pit limits, as necessary, to provide access to all working faces in the upper open pit and connecting with the primary crusher, oxide leach pad, and waste rock storage areas located to the southwest, east, and north of the pit. Mine haul roads will be constructed using mine waste material. Road surface material may be crushed and screened as needed to produce a smooth running surface.
4.11 Waste Management
Due to the small size of the operation, both the mine and process will generate small quantities of wastes. Chloride Copper will manage materials on site to minimize the amount of waste created and to ensure wastes do not become mixed, contaminated, or otherwise mismanaged. A summary of these measures is provided below.
4.11.1 Solid Waste
As part of the onsite permitting effort, Chloride Copper may file for a solid waste facility permit and include the facility in the area-wide permitting effort allowed by ARS §49-243.P. The facility would use a trench and cover technique. The facility would be managed for onsite, non-hazardous wastes, and will not accept any off site wastes. The primary disposal activities on site will include, but may not be limited to, the following:
Demolition and construction debris
Non-putrescible materials
Waste from maintenance and operations meeting the definition of inert or non-hazardous such as respirator filters, gloves, boxes, non-recyclable packaging material, air filters, hoses, and piping
This permit will meet the requirements of a non-municipal solid waste facility.
4.11.2 Hazardous Waste
Hazardous wastes that may be generated at the facility include, but may not be limited to, the following:
Waste paint materials such as thinners
Chemical wastes such as acetone from the onsite laboratory
Chemical wastes from the SX/EW process
As part of the permitting effort, Chloride Copper will file for a hazardous waste identification number from the Environmental Protection Agency (EPA) and register as a generator of hazardous waste with the ADEQ. Proper management of wastes should allow Chloride Copper to have a status of Conditionally Exempt Small Quantity Generator (CESQG) of hazardous wastes. However, in the event that it becomes necessary to manage quantities of waste in excess of the CESQG threshold, Chloride Copper will comply with applicable requirements for proper management of waste on a larger scale. In addition, the Chloride Mine will ensure that:
Waste will be packaged, labeled, stored on site, and inspected as required by the hazardous waste regulations.
Materials entering the site will be examined to determine if they have the potential to create hazardous waste, and if they do, non-hazardous substitutes will be sought.
Operations will be examined on an on-going basis to ensure that hazardous substances are eliminated whenever possible.
4.11.3 Sanitary Waste
Sanitary waste at the Project will be handled by a septic system, with leach fields located in the vicinity of the buildings where sanitary facilities exist. During the construction phase, and where necessary during operations, portable toilets will be used in various locations throughout the plant and mine sites. Sanitary wastes will be collected periodically by a commercial sanitation service and removed for disposal off site.
4.11.4 Specific Waste Management Activities, Mine and Process
In general, waste will be managed in dumpsters or other appropriate containers. All containers will be covered or weighted to prevent blowing trash. Trash from office areas will be bagged. A waste disposal company will be contracted, as necessary, to manage wastes other than debris or construction and demolition wastes.
Scrap Metal
Scrap metal will be managed to facilitate recycling, with separate roll-off dumpsters located near points of use. Contracts with scrap metal recyclers will be established for on-going recycling activities. In the event recycling becomes impossible or otherwise impracticable (i.e., scrap prices drop or scrap prices become so high that there are not enough recyclers), scrap metal will be stockpiled near the solid waste facility for bulk recycling. Existing scrap metal from past mining will be stockpiled for future removal.
White Paper
The Department of Economic Security (DES) provides a recycling service for white paper. Unfortunately, the pick-up service DES offers is confined to the Kingman area. At this point, Chloride Copper plans to drop off white paper waste at the DES offices on an as-needed basis to minimize the amount of paper disposed on site. Chloride Copper will continue to investigate additional opportunities for white paper management.
Grease
Grease associated with the hoisting, milling, and other operational equipment will be placed into drums or other bulk containers suitable for recycling. If the grease is not suitable for recycling, the contained waste will be sent off site for disposal. While on site, the containers will be managed in an area that will provide secondary containment.
Used Oil
Used oil from maintenance activities will be managed in bulk containers with secondary containment to ensure there is no release to the environment. Only oil acceptable for recycling will be placed in the bulk containers. Used oil not acceptable for recycling will be placed in drums for proper disposal.
Batteries
Lead acid batteries will be returned to the vendor for recycling or shipped off site to a recycler. While they are stored on site, they will be managed in an area protected from storm water and will have secondary containment. Nickel-cadmium batteries will be stored for recycling by a local vendor. While on site, they will be managed in drums or boxes suitable for storage. Lithium batteries will also be stored for recycling in appropriate containers.
Tires
There are two opportunities for disposing of tires that are less than 3 ft. in diameter. The vendor will remove the waste tires from the Property for appropriate disposal or recycling; or a waste handler will be contracted to remove the tires for appropriate disposal or recycling.
At mining sites, the vendors who supply the tires generally remove them for recycling or disposal. Chloride Copper will contract with vendors or waste haulers who can appropriately manage waste tires smaller than 3 ft. in diameter.
Tires that are greater than 3 ft. in diameter are eligible for onsite disposal (AAC Title 18 Chapter 13.) This code allows operators to bury mining waste tires in an onsite cell if they meet specific requirements. Once placed in the cell, the tires will be covered with a minimum of 6 in. of material within 50 days of placement. Once the cell is full, at least 3 ft. of final cover will be placed over the cell within 180 days. Chloride Copper will file the required annual reports, keep records, and provide any certifications as required by the regulations.
At this time, Chloride Copper is investigating the potential for reuse of these tires and will continue to seek contracts for beneficial uses of mining tires. As appropriate, tires may also be used for erosion control or structural fill. If there are alternatives for tire disposal, Chloride Copper will review them and apply as appropriate.
Lead Flake and Anodes
The EW process uses lead anodes to provide the necessary electrolytic conditions for copper plating. During this process, the anodes degrade creating a lead flake that falls into the EW cells. This flake and the degraded anodes are a valuable commodity when managed properly and recycled. On site management of these materials will consist of placing the flake into a roll-off or other container designed to contain the material for transport to a lead smelter for recycling. Anodes will also be stored in containers to facilitate shipment for recycling.
Piping and Liner Materials
Piping and liner materials may be recycled. Chloride Copper plans to identify a recycler of these materials and utilize them accordingly. If piping and liner grade materials are not recyclable, Chloride Copper will dispose of these materials in the onsite waste management facility.
Wood and Other Packing Materials
Much of the material delivered to the Chloride site will be on wooden pallets, packaged in cardboard, or wrapped in plastic. Many of these items will be recycled in Kingman. Chloride Copper plans to recycle as much of the shipping and packaging material received at the site as possible, utilizing businesses in Kingman and the surrounding communities.
Off Site Shipment of Wastes
When offsite disposal is necessary, Chloride Copper will manage materials as required by the Resource Conservation and Recovery Act (RCRA) and Department of Transportation (DOT) regulations. All shipments will be properly marked and manifested (using manifests or bills of lading), and characterizations of shipped waste materials will be available.
4.12 Noxious Weeds
If any noxious weeds appear at the Project site they will be controlled by hoeing.
4.13 General Schedule
Mine development will commence as soon as equipment can be mobilized following approval of this Plan of Operations. This would be expected within one month of plan approval.
Mining operations will be conducted in a series of phases.
The phases, the BLM acreage to be mined per phase and the tons of materials to be mined per phase are identified as follows:
Table 1.0 Acreages of the Chloride Copper Mine
Description BLM Land
(acres) Private Land
(acres) Total Acres
Project Boundary 154 90 244
Previously Disturbed 157 0 157
CCM Proposed Mine Area 36.12 0 36.12
Total Reclaimed 157 0 157
Table 10 – Production Schedule
Year
1 2 3 Total
Tons Ore 480,813 448,987 455,427 1,385,227
Tons Waste (Minimal) 183,370 183,370 183,370 550,109
Ore Grade % Copper 0.53 0.57 0.55 0.55
Copper Recovery % 0.7198 0.8414 0.8414 0.8
Copper Produced Pounds 3,678,179 4,299,552 4,217,377 12,195,108
Table 1.1 - Mine Excavation Phases
Excavation Phase Property Ownership Size
(acres) Township 23 North, Range 18 West, Section 22 & 27
Phase 1 BLM 10.56 NE ¼ and SW ¼
Phase 2 BLM 5.28 NE ¼ and SW ¼
Phase 3 BLM 5.28 NE ¼ and SW ¼
Mining and processing will begin simultaneously, and are expected to be complete within three to four years unless additional ore is found. Mine site (BLM land) reclamation will be ongoing after the completion of Phase 3 with reclamation of the final cuts conducted as soon as mining is complete. It is expected that this procedure will take one years per phase.
4.14 Site Operations Security and Public Safety
Security
In order for the Project operations to run smoothly, it is important that the site be secure. Theft and vandalism could potentially have a negative effect on worker safety and on operating efficiency. Therefore, the plant and open pit will initially be fenced and access to the site will be controlled by a security gate. Security patrols will be conducted routinely. Signs will be posted along the fence and at strategic locations along roads warning people that entering the site is prohibited.
Public Safety
In addition to protecting the site from potential vandalism or theft, it is also important to protect the public from interfacing with the mine operations and to prevent potential injury. Hazards of a typical mining operation include, but are not limited to: traumatic injury from large equipment, getting entangled in machinery, driving over steep embankments, slipping or falling on uneven ground or slippery surfaces, encountering high-voltage electricity, exposure to chemicals or reagents while not wearing proper personal protective equipment, and exposure to loud noises while not wearing hearing protection. Employees working at the site are required to receive specific training in accordance with Mine Safety and Health Administration (MSHA) rules, covering all aspects of site safety, whereas recreationists will likely have no such training and may not recognize the hazards. Therefore, it is imperative that access is controlled and that trespassing rules are enforced. The same fencing, patrols, and signage discussed in Section 2.12.1 will serve to warn recreationists and others in the area of potential dangers. In addition, employees will be trained to be aware of trespassers in the course of their normal duties and report any suspicious activity to the safety and property departments.
The mine and plant operation will be designed to minimize the need for visitors to drive or walk in hazardous areas. Most visitors, vendors, and salespeople will come and go from the administration building or the guardhouse at the entrance of the facility. Supply route drivers will receive site orientation training and be familiarized with their specific loading/unloading locations and procedures.
4.15 Summary of Operations
A summary of the operations, existing conditions and future conditions are provided in the Table below.
Table 4.4 Summary of Operations
Operations Existing Future
Mine Hours of Operation - Mon – Sat., 6:00 am – 4:00pm
SX/EW Hours of Operation 24 hours/day, 7 days/week
Number of employees - 33
Acres Disturbed 157 acres – BLM
0 acres – Private 36.12 acres – BLM
0 acres – Private
Depth of Mining 100 feet max (estimated)
Truck Trips - 28 per day one way
Dozers - 1- Cat D6
1- Cat D9
Loaders - 2 – Cat 966
1- Cat 988
Excavators 1- Cat 350
1-John Deere 890D
Off Road Haul Trucks 3- Cat 740
Water Consumed/Day - 50,400 gals.
Fuel Storage Tanks, Scales, Garages, Gates, Signs, Fences 3 gates and fence on private parcel 1 Fuel tank – 12K capacity, cargo containers, trailer on private land.
1 gate, mine hazard warning signs on BLM land
Production - 2000 tons/day
Table 4.4 Summary of Operations - continued
Noise Emissions - Per MCAP
Air Emissions Max allowed by AZ DEQ
NPDES Permit Need - To be determined
Diesel Consumption - 200-250 gals./day
Electrical Consumption - NA – Grid
Daily Opacity Levels - Maximum allowed by Air District
Biological Permits To be surveyed -
Cultural Resources To be surveyed -
Tribal Concerns - To be determined
Visual - Lights only for night work at plant
BLM Bond Amount - ?
5.0 Transportation
Transportation
There is no rail service into the plant and all materials arriving and leaving the plant will be transported by truck. East-west rail service is available at Kingman, about 30 miles to the south.
Sulfuric Acid
Sulfuric acid is a reagent used in the leaching operation; it will be received in special acid tank trucks with a capacity of about 22-24 T. Sulfuric acid is available regionally from two smelters in Arizona and one in northern Mexico. Acid receipts will be scheduled five days per week and during a day shift. The plant can receive and unload about one acid truck per hour, which will require about three hours per day for sulfuric acid. Acid receipts will be scheduled to avoid high traffic hours and shift changes for safety.
Diesel Fuel
Diesel fuel is a major consumable for the haul trucks. Diesel fuel is available from local suppliers and will be received in tank trucks with a capacity of about 3,000 gallons. Diesel receipts will be scheduled five days per week during the day between shift changes. The plant will receive and unload about one truck per hour, which will require about two hours per day for receiving the diesel into storage.
Copper Cathodes
Cathode copper will be produced from the oxide ore in the SX/EW plant. Peak cathode production will occur in the later part of Year 1. This production rate will fall off in Year 3. The cathode copper will be loaded onto flatbed tractor trailers. Approximately one truck every day will be loaded for delivery. Cathode copper shipments will be scheduled five days per week during the day.
Kerosene
Kerosene is used as a diluent in the SX process. Kerosene will be delivered in 2,500-gallon trucks and stored in an onsite tank. It is anticipated that one truckload of kerosene will be received every two months. Deliveries will be scheduled during workdays.
Miscellaneous Consumables
Miscellaneous quantifiable consumables will consist of reagents used in the process and wear parts used in the crushing process. Reagents used in the SX/EW circuit will be an oxime extractant, diatomaceous earth, clay filter media, FC-1100 mist suppressor, guar, and cobalt sulfate.
Consumables such as office supplies, safety equipment, and small tools cannot be quantified; however, these consumables are not considered significant to the transportation study.
Miscellaneous Fuels and Lubricants
Miscellaneous fuels and lubricants will include gasoline, motor oils, lubricants, and antifreeze. Used oils and waste antifreeze will be transported out of the plant for recycling. All miscellaneous fuels and lubricants will average less than 1,000 gallons per week or one trip per week.
Employees
SIERRA employees will only be involved in transporting ore and mine waste. They will not be engaged in commercial transportation. Product shipped will be through a licensed trucking firm. Goods and supplies will be delivered by licensed trucking companies.
Safety Evaluation
Access to the plant will be by federal and state highways up to the primary access road. The access road will be 0.5 miles long with no sharp turns or grades of more than 8 percent. The access road will be two-lane, 14-ft. wide each, with shoulders. Drainage system will be provided along the road to control storm water runoff. The road will be designed for travel at 25 mph.
Figure 8 – Truck traffic flow.
6.0 Interim Management Plan
Temporary closure is not anticipated but could be necessitated by an act of God, break-down of key equipment, unavailability of fuel or key supplies, labor disputes, periods of low copper prices or other unforeseeable events.
Should temporary closure be required, SIERRA would notify the BLM Kingman Field Office of the closure, the reason for the closure and the expected duration of the closure. Specific measures that will be taken at the mine and process sites are provided below.
6.1 Mine Site
In the event that the pit area is not to be occupied by personnel and be closed for more than one month, SIERRA will take the following actions:
Mining equipment will be consolidated in the process (private land) area.
Gate will be locked.
6.2 Process Site
In the event that the process site is not to be occupied by personnel and be closed for more than one month, SIERRA will take the following actions:
Tools, equipment, supplies and records will be removed from the office/change house and the shop/storage mobile building.
All fuel, chemicals and waste will be removed from the site and tanks secured.
The gates will be locked and Keep Out signs posted.
All necessary pumping systems will remain operating to circulate process flows.
A remote monitoring system will be established to allow water levels to be monitored from off-site.
A company representative will inspect the site daily and after heavy rains to ensure that the site is secure and that the inspection and maintenance requirements of the SWPPP are being met.
7.0 Reclamation Plan
7.1 Mine Site
Reclamation of all areas disturbed will be completed to the standard described in Section 3809.1-3(d) of 43 CFR 3809.6. SIERRA will implement reasonable measures to prevent unnecessary or undue degradation of Federal lands during operations and reclamation. These will include restricting reclamation activities to disturbed areas (e.g. not obtaining fill or covering materials from undisturbed areas).
As a component of the overall environmental stewardship policy of SIERRA for the Chloride Project, a concurrent reclamation plan will be instituted to meet or exceed regulatory requirements by conducting a reclamation and closure approach as SIERRA progresses with mining activities. This approach provides a template for development of on-going mitigation measures that will be implemented during the operation phases of the Project. Elements of this approach have been discussed in previous sections of the MPO. In concept, the mine site will look much like what it looks like today with the exception of a larger heap leach pad and alteration of the eastern portion of the open pit. The heap leach pads will be naturally contoured and covered with typical desert soil. The eastern pit will be benched and contoured consistent with BLM and Arizona reclamation requirements (Figure 3-2). Temporary HDPE and concrete asbestos pipelines will be removed and disposed of in accordance with both state and federal regulations. Structures such as the SX/EW plant will be removed and all pipe and other manmade materials with the exception of the concrete foundations will be removed and disposed of properly. Revegetation is not required for slope stability nor is it required by the BADCT; however, surface contouring consistent with the landscape will promote natural vegetation. A facility closure process will be followed for those mine facilities that are regulated by the ADEQ and the APP.
Major elements of the reclamation and closure plan are dictated by the regulatory requirements contained in the Arizona Mined Land Reclamation Act, BLM regulations, and the APP program. Although other regulatory requirements may contribute mitigation elements, these three regulatory programs form the framework for the reclamation plan. Appendix 1 presents the estimated cost for reclamation based on BLM guidelines.
Applicable design criteria for the overall approach to mining, processing, and the sequencing of material placement within the final landform for optimum reclamation and closure conditions are addressed. The plan contains provisions for protection of the environment during the operations phase using BMPs. These practices are primarily guided by the protection of surface water and groundwater resources. Sediment transport is addressed through design of storm water control features and dust control measures. The proposed reclamation/closure mitigation elements for the Chloride Project include employment of concurrent reclamation; therefore, reclamation obligations will be incrementally reduced as the operation progresses.
7.1.1 Property Reclamation
At the completion of mining, SIERRA and its contractors will remove all equipment, and any remaining trash or debris from the BLM property. The pit and haul road from the BLM property to the private land will be reclaimed. On hillsides, side-cast material will be pulled back to blend with the hillside. On flatter areas, the surface will be re-contoured to match existing contours, surface ripped and scarified. A hydraulic excavator will be used to pull about 1,500 cy of material side-cast during haul road construction back into the roadway on any hillside portion of the road. The remainder of the road will be ripped to a depth of 2 feet using a dozer with a ripper to promote revegetation.
All areas under BLM management that have been affected by mining disturbance resulting from this MPO shall be graded to blend with the surrounding topography as best possible. The attached Mine Plan of Operations maps provide the approximate final contour for the reclaimed site.
All disturbed areas on BLM land will be ripped to 2 feet in depth or scarified by grader to create a seedbed. Contoured and scarified surfaces will be allowed to naturally re-seed. In accordance with the Arizona Native Plants law, all recovered plants stored in the nursery area will be returned to the area and re-planted. When reclamation is complete, SIERRA will notify the BLM so that an inspection of the area can be made.
Because both the mining and reclamation operations are phased, this will allow SIERRA to minimize the amount of disturbed ground. In the first year the total amount of disturbance from mining will be at the highest amount for the project. It is estimated to be at 10.56 acres of disturbance. In years 2 and 3 as the heap leach pad is developed the amount is expected to fall to 5.28 acres per year. As each new years operation begin the previous years disturbance will be reclaimed.
The estimated cost of reclamation for the project is $??????. Reclamation cost calculations are presented in Appendix H, and include dust control, contractor administration costs, contractor’s overhead expenses, contractor’s profit, and the BLM contract management fee.
8.0 Monitoring Plan
8.1 Wildlife
SIERRA will post photos of any threatened, endangered and special status species in the mine office. Miners will be instructed to recognize and avoid disturbing these species or other wildlife encountered. Sightings and injury or death of any species will be recorded and reported to the BLM.
8.2 Archaeological Sites
Archaeological sites will be marked and avoided. SIERRA will monitor operations to ensure that these sites and other artifacts that may be discovered are not disturbed. BLM will be contacted promptly if artifacts are discovered.
8.3 Surface Water Quality
Surface water quality at the mine site and process site will be monitored as required by the SWPPPs prepared to comply with MSGP 2010.
8.4 Reclamation Success
SIERRA will monitor the mine site annually for three years following the winter rains to see if disturbed areas are revegetating and other reclamation measures need repair or modification. Should remedial work appear necessary, SIERRA will consult with the BLM Yuma Field Office to agree on methods and to obtain approval to carry out the work.
9.0 Occupancy
Sierra Resource Group, Inc. requests BLM grant permission for occupancy at the Chloride Copper Mine Project under 43 CFR 3715, Use and Occupancy under the Mining Laws. The following information is submitted in support of this request.
The mining equipment will remain on the mine site until mining is complete. A gate will be placed across the existing road that enters the mining area at the northwest corner of the site. This road allows access to the pit area and will be gated to protect public safety and for security of the mining equipment. Additional gates will be placed at access points to the private parcel. These gates will be located on private property. In addition, appropriate warning signs will be placed at all access points and in the pit area to notify the public of potential safety hazards on the mine site.
The proposed occupancy is reasonably incident to prospecting and mining operations. The mining equipment is required for the mining operation and serves no other purpose. Because of the remoteness of the site, it would be impractical to remove equipment after each day’s work and return for the next. Limiting access to the mine site and appropriate warning signs are needed to protect the public from mining hazards and to discourage theft and vandalism of mining equipment.
The proposed occupancy is appropriate for the planned work, constitutes actions and expenditures of labor and resources that would be made by a person of ordinary prudence to develop, mine and beneficiate a valuable mineral deposit using methods and equipment appropriate to the geological terrain, mineral deposit and stage of development and reasonably related activities.
The proposed occupancy constitutes substantially regular work that directly benefits the mineral property by providing for mining the ore and reclaiming the site. The work is directly associated with the development of the land and the processing of the ore. The work is contemplated to be continuous until mining and reclamation are complete.
The activities proposed are reasonably calculated to lead to the extraction and beneficiation of minerals from the ore on the property. The mining equipment proposed in Section 4.1.1 above is sized to be adequate for developing the mine and mining the ore at the proposed rate with normal equipment availability. The work of development and mining will be observable and verifiable.
The operations processing plant, office/change house unit, shop/storage unit, watchman’s trailer/RV, portable toilets, fuel and water tanks shall be located on the private parcel.
Nothing proposed in this Notice will interfere with public access to adjacent public lands around the mine site. Existing BLM roads not entering the operating area on BLM land will remain open to the public.
Mine employees, guests and visitors to the mine will be required to comply with a mine safety plan and will be provided with required safety equipment. The signs on the gates will direct visitors to the office to obtain authorization before visiting working areas of the mine. Approved visitors will receive a briefing on mine hazards and safety procedures. An analysis and the full use and occupancy request is provided in Appendix J.
10.0 Acknowledgements
It is understood that should the nature of the operation change, a modified or supplemental Mine Plan of Operations and Reclamation Plan may be required.
It is understood that approval of this Mine Plan of Operations and Reclamation Plan does not constitute certification of ownership to any person named herein or recognition of the validity of any mining claim herein.
It is understood that a bond equivalent to the actual cost of performing the agreed upon reclamation measures will be required before this plan can be approved.
Bonding and any bond reduction amounts will be set on a site-specific basis in coordination with cooperating agencies.
It is understood that approval of this plan does not relieve SIERRA of the responsibility to comply with other applicable Federal or State laws, rules, or regulations.
SIERRA agrees to comply with all Conditions in the Mine Plan of Operations and Reclamation Plan, including recommended changes and reclamation requirements.
SIERRA understands that the bond will not be released until the BLM or state agency in charge gives written approval of the reclamation work.
Signatures
SUBMITTED BY:
SIERRA RESOURCE GROUP, INC.
Rod Martin
CEO & Director
Date:
11.0 References
Arizona Bureau of Mines, 1969, Mineral and Water Resources of Arizona: The Arizona Bureau of Mines Bulletin 180, University of Arizona, Tucson, 1969.
D’Andrea, D.V., Larsen, W.C., Fletcher, L.R., Chamberlain, P.G. and Englemann, W.H., 1977, In Situ Leaching Research in a Copper Deposit at the Emerald Isle Mine: United States Department of the Interior, Bureau of Mines, Report of Investigations 8236, 1977.
D’Andrea, D.V. and Runke, S.M., 1976, In Situ Copper Leaching Research at the Emerald Isle Mine (Chapter 24): United States Department of the Interior, Bureau of Mines Internal Report on World Mining and Metals Technology, pp. 409-419, 1976.
Dings, M.G., 1951, the Wallapai Mining District, Cerbat Mountains, Mohave County, Arizona: U.S. Geological Survey Bulletin 978-E, Contributions to Economic Geology, pp. 124-153, U.S. Government Printing Office, Washington, D.C., 1951.
Donley, E., Lamb, A. and Sykes, T., 2001, Potentially Responsible Party Evaluation Search, Emerald Isle Mine Site, Mohave County, Arizona: Draft Report Prepared by Dynamic Corporation for the U.S. Department of the Interior, Bureau of Land Management, Germantown, MD, November 2001.
Dunham, H.E., 2004, Valuation of Emerald Isle Property: Fairness Opinion Document Prepared for Atlas Minerals, Inc., Denver, Colorado, by H.E. Dunham and Associates, Tucson, Arizona, March 2, 2004.
Eidel, J.J., Frost. J.E. and Clippinger, D.M., Copper-Molybdenum Mineralization at Mineral Park, Mohave County, Arizona in Ore Deposits of the United States, 1933-1967, The Graton-Sales Volume, John D. Ridge, (Ed.): The American Institute of Mining, Metallurgical, and Petroleum Engineers, Inc., New York, 1968, pp. 1258-1281.
Gillespie, J.B., and Bentley, C.B., 1971, Geohydrology of the Hualapai and Sacramento Valleys, Mohave County, AZ: U.S. Geological Survey Water Supply Paper 1899-H.
Keith, S.B., Gest, D.E., DeWitt, E., Woode Toll, N. and Everson, B.A., 1986, Metallic Mineral Districts and Production in Arizona: Arizona Bureau of Geology and Mineral Technology, Geological Survey Branch Bulletin 194, p. 26, 1986.
Peterson, R.C., 1976, Review of Aeromagnetic Data over the Emerald Isle Prospect: Report Prepared for Mine Development Associates, 1976.
Ste-Genevieve Resources, 2004, Miscellaneous Correspondence and Technical Data.
TSC Enterprises, Inc. (TSC), 1992, Emerald Isle Mine, Arizona: Internal Company Report.
U.S. Mines Register, 1952, U.S. Bureau of Mines, Mines Register, (Successor to the Mines Handbook and the Copper Handbook) Vol. XXIV, pp. 158-159.
Western Regional Climate Center, 2003, Arizona Climate Summaries: http://www.wrcc.dri.edu/summary/climsmaz.html.
Wieduwilt, W.G., 1976, Review of Induced Polarization and Resistivity Data, Emerald Isle Area, Mohave County, Arizona: Report Prepared for Perry, Knox, Kaufman, Inc., Project 0620, Tucson, June 6, 1976.
Wilkinson Jr., W.H., Vega, L. and Titley, S.R., 1982, Geology and Ore Deposits at Mineral Park, Mohave County, Arizona, in Advances in Geology of the Porphyry Copper Deposits, Southwestern North America, Spencer R. Titley, (Ed.): University of Arizona Press, Tucson, Arizona, pp. 523-541.

