EV Firms Opt for More Affordable Production Method
Post# of 1075
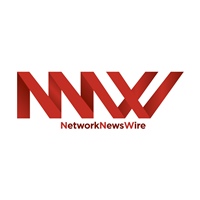
More than a decade after California-based startup Tesla unveiled the Tesla Roadster and proved that road-worthy electric vehicles (“EVs”) were a viable mass-market option, Tesla is now the largest electric vehicle maker as well as the most valuable car company on the planet. It currently has a backlog of 400,000 Model 3 orders and a production rate of 1,000 cars per day, and the EV maker has produced more than 360,000 EVs since the Roadster first hit the roads.
However, Tesla’s journey to the helm of the nascent EV sector was fraught with complications, especially regarding scaling up production for the mass market. New entrants into the electric vehicle space are taking different roads to avoid these issues.
Some have cast their nets out and found investors willing to pour billions of dollars into their startups, ensuring they have more than enough financing to set up large factories and start producing thousands of electric vehicles without having to deal with a myriad of production delays. For instance, Michigan-based automaker Rivian claims to have raised a whopping $10.5 billion in capital from Ford Motor Company and Amazon to finance the production of electric SUVs, trucks and vans. And in July, EV startup Lucid Motors went public and collected $4.5 billion in funding, which will allow it to get its first EV, the luxurious Lucid Air, on the road.
Electric vehicle makers who haven’t been able to raise such extensive capital are now looking at innovative production methods that will reduce the cost of mass EV production to avoid the production delays that plagued Tesla’s initial foray into mass electric vehicle production. Traditionally, carmakers would build around 240,000 vehicles per year at a cost of $2 billion, but EV makers are now building smaller “microfactories” with fewer or less-expensive equipment that churn out fewer vehicles at a reduced cost. London-based Arrival has gone this route, using microfactories worth around $40–$50 million equipped with fewer expensive machinery to build electric vans and buses.
Arrival has developed lightweight, colored plastics, eliminating the need for special painting equipment, which can cost hundreds of millions of dollars. Additionally, its engineers have built molds for plastic vehicle parts for thousands of dollars rather than traditional metal equipment, which would have cost the company millions of dollars. Arrival is also looking to take advantage of reduced shipping costs and accessible labor by installing its microfactories close to major markets around the globe. After raising $660 million back in March via a public offering, Arrival is now building two plants in the United States, one to develop electric buses and another for vans.
Canoo, another American electric vehicle startup, will also build microfactories, and according to the firm’s leader Tony Aquila, it will build a larger microfactory to act as a hub for the smaller ones. Electric Last Mile Solutions will reassemble prefinished electric vans made in China at an Indiana-based General Motors plant, a move that will save the company hundreds of millions of dollars in equipment. In fact, other startups are cutting costs by doing production overseas, and most of them plan to localize production as profits grow.
The magnitude of creativity being brought into the EV space may not have reached its peak just yet given that many more companies, including Net Element (NASDAQ: NETE), are switching from other industries and joining the electric vehicle industry. Such changes often come with new twists in the way things are done.
NOTE TO INVESTORS: The latest news and updates relating to Net Element (NASDAQ: NETE) are available in the company’s newsroom at http://ibn.fm/NETE
Please see full terms of use and disclaimers on the Green Car Stocks website applicable to all content provided by GCS, wherever published or re-published: https://www.GreenCarStocks.com/Disclaimer

