Like Eating Glass: Elon Musk Shares the Complexiti
Post# of 1091
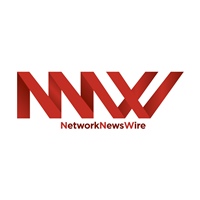
In just over a decade, electric vehicle (“EVs”) startup Tesla has become the largest EV maker in the world. The California-based company unveiled the first all-electric vehicle back in 2008, the Tesla Roadster, proving that it was possible to develop road-worthy, zero-emission electric vehicles. In the years since, Tesla has manufactured more popular EVs, with 2018’s Model 3 becoming the best-selling electric vehicle of all time.
With several territories across the world looking to reduce their carbon emissions and cut their reliance on fossil fuels, the EV sector is poised to see significant growth in the next couple of decades. However, according to Tesla CEO Elon Musk, manufacturing electric vehicles is an extremely complex process. Unlike conventional gas-powered vehicles, which are mostly hardware based, electric cars rely on carefully calibrated software and hardware. Developing these two crucial components from the ground up is fraught with complexities, so much so that Musk compares it to eating glass.
It is an “insanely difficult” process, he says, so complex, in fact, that those who haven’t been involved in manufacturing could not even imagine just how “painful and difficult” it is. Building an electric vehicle prototype is quite easy, says Musk, but producing an EV that will be on the roads is next-level difficult. This is because the average EV has some 10,000 unique parts and processes that have to function perfectly, he explains, and if each part isn’t present and perfectly installed, the car will not leave the factory.
For instance, there has been a shortage of the module used to control the airbags and seat belts this quarter, he says, so Tesla cannot ship recently manufactured EVs. This has significantly hampered Tesla’s global production in Fremont and Shanghai. There have been hundreds of electric vehicle startups in and out of the United States, but the only reason Tesla is the biggest EV producer in the world is its ability to get its electric vehicles from prototype to mass production.
With the world currently facing a chip shortage that is predicted to stretch into 2022, the resultant production bottleneck could have been bad for Tesla’s long-term manufacturing targets. For the first time in its history, Tesla surpassed $1 billion in GAAP net income over Q2 2021 — despite the ongoing chip shortage. Tesla achieved this feat by using alternative chips, which was an “incredibly intense” process that involved planning the new chips, writing new firmware, integrating it into an EV and then testing it exhaustively before going to production, all in a matter of weeks.
As the industry matures, EV makers are going to get better at manufacturing electric vehicles and dealing with issues such as component shortages as they arise. At the moment, companies such as Tesla will continue honing their EV manufacturing processes and finding new, innovative, and affordable ways to get even more zero-emission electric cars on other roads.
Since the electric vehicle industry is technology-heavy, entities such as Net Element (NASDAQ: NETE) are likely to be within their turf, unlike traditional auto makers who have quite a learning curve to contend with.
NOTE TO INVESTORS: The latest news and updates relating to Net Element (NASDAQ: NETE) are available in the company’s newsroom at http://ibn.fm/NETE
Please see full terms of use and disclaimers on the Green Car Stocks website applicable to all content provided by GCS, wherever published or re-published: https://www.GreenCarStocks.com/Disclaimer

