The Case for Making Cities Out of Wood Could a sy
Post# of 51892
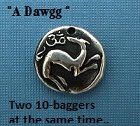
Could a synthesized wood that’s as “strong as steel”
be the backbone of future cities? < >

In 2018, Dan Doctoroff, the C.E.O. of Sidewalk Labs, Google’s sibling company under Alphabet, answered a question about what his company “actually does” during a Reddit “Ask Me Anything” session, replying, “The short answer is: We want to build the first truly 21st-century city.” Quayside, a Toronto neighborhood the company is developing in partnership with a Canadian tri-government agency, is the first step toward Doctoroff’s goal. It has been in the news because it could inspire a Black Mirror plot: It will be built from “the Internet up,” according to a project document, a merger of “physical and digital realms.” Fittingly, according to the New York Times, “No obvious way to opt out of Quayside’s surveillance systems exists, except by staying out of the area.”
But Quayside’s newsworthy for another, more encouraging reason: The plan is to build the place, not out of concrete and steel, but wood—and wood is looking good. A recent advance in wood technology should interest the neighborhood’s developers: Teng Li, a University of Maryland mechanical engineer, created with his colleagues wood that’s as “strong as steel, but six times lighter,” he said. Liangbing Hu, Li’s co-author on the study, added, “This kind of wood could be used in cars, airplanes, buildings—any application where steel is used.” Making it is just a two-step process. The scientists first boiled natural wood in a mixture of sodium hydroxide and sodium sulfite, to remove some of the lignin and hemicellulose, substances contained in the walls of wood cells (the former retard parasite and bacterial attacks, the latter cover and bind fibers). Then they put the wood in a hot press, which leads, as they say in the paper, “to the total collapse of cell walls and the complete densification of the natural wood with highly aligned cellulose nanofibres.” The result, they conclude, is a “low-cost, high-performance, lightweight alternative” to “most structural metals and alloys.”
“Our proposal is that we need timber to save us.”
The idea of future wood cities has been hanging around for at least a few years. In 2014, for example, the Boston Globe wondered, “Will cities of the future be built of wood?” The rise of both human population and global temperature prompted much of the interest in the sustainability of city-scale timber construction. By 2050, we will number almost 10 billion; and since two-thirds of us will be city dwelling—up from just over half in 2014—cities will have to grow. It’d be ideal to do that without curtailing efforts to combat climate change; it wouldn’t be helpful, for instance, to keep extracting and transporting the raw materials needed to build steel and concrete structures, which are more expensive and have large carbon footprints. Wood, on the other hand, is “a plentiful resource that grows back relatively quickly, and even pulls carbon out of the atmosphere as it does,” the Globe noted. Yugon Kim, an architect passionate about timber construction, said, “We all are hard-wired to see the city as being steel, glass, and concrete. Our proposal is that we need timber to save us.”
The proposal hasn’t been ignored. The Economist published a video titled, “Wooden skyscrapers could be the future for cities.” The main obstacle to this outcome—what a 2016 paper called “a full timber building renaissance”—is the public’s fear of city fires, which has been reflected over centuries in construction codes globally. Some researchers, like Alastair Bartlett, at the University of Edinburgh, see in these obstacles an “opportunity,” as he wrote in a 2017 study, “to revisit compartment fire behaviour and to quantify the impact of these new construction technologies on the compartment fire dynamics.”
Bartlett, along with some colleagues, tested the sort of wood mid- and high-rise buildings—like Framework, in Portland—have recently been made out of, known in the industry as “cross-laminated” or “mass” or “tall” timber, which is how Quayside’s developers refer to it. Bartlett set up three rooms of equal size, about as big as a large walk-in closet. Two of the rooms had two exposed surfaces of timber (one with two walls exposed, the other a wall and the ceiling); the last room had two walls and the ceiling exposed (non-exposed surfaces were covered with plasterboard). Each room had four wooden “cribs,” or pallets, for the “fuel load,” placed on the ground, one of which was lit using fiber strips soaked in paraffin. Bartlett then documented how fast and how hot each room burned. The room with an exposed wall and ceiling managed to “auto-extinct”—the fire went out by itself. This depended “on the char layer [of the wood] remaining attached” rather than falling off while the cribs were burning, Bartlett concluded. He wants to do many more experiments because it’s still not clear how, in mass timber buildings, to get compartment fires to reliably burn out on their own, a “cornerstone of fire safety engineering design,” he writes. “The failure modes of common compartment construction systems and materials are relatively poorly documented from a scientific (rather than compliance testing) perspective.”
Bartlett’s experiment investigating the fire dynamics of a room with two walls of exposed timber. (a) shows the back wall of exposed timber catching fire. (b) shows all the exposed timber surfaces burning. And (c) shows the extent of flames right before the researchers extinguished them. Photograph by Rory M.Hadden, Alastair I.Bartlett, et al.
The combustibility of this wood depends partly on its size, according to Daniel Safarik, editor of the Council on Tall Buildings and Urban Habitat, a Chicago-based non-profit. “Massive wood walls and structural beams and columns comprised of engineered panels have demonstrated fire performance equal to concrete and, in some cases, superior to steel,” he told The Architect’s Newspaper. “Mass timber has to burn through many layers before it is structurally compromised—basically it ‘chars’ long before it collapses.” Still, as a 2016 review concluded, “Large-scale and full-frame tests are also necessary…to determine the variety of possible fire induced failure modes that may occur in real mass timber buildings.” The same will no doubt be true of the new densified wood Li and his colleagues recently created.
There is also, alongside the environmental and economic, an aesthetic-psychological case for wood cities. Clare Farrow, who is co-curating a current London exhibit called “Timber Rising–Vertical Visions for the Cities of Tomorrow,” wrote in Dezeen, “Studies are showing that the presence, scent and touch of wood can have remarkably positive effects, not only on people’s wellbeing in a general sense, but more specifically on stress levels, blood pressure, communication, learning and healing.” A 2015 review in Wood Science and Technology supports her claims and also suggests that “specific aspects of wood such as colour, quantity, and grain pattern should be examined” in future studies.
I certainly have a fondness for wood. On work errands with my father, when I was a child, I remember being drawn to the plywood section of Home Depot. I’d run my hands against the surfaces of large slabs, sometimes still damp after being cut, and I’d smell the fresh sawdust piled up at the cutting station. I still have my 7th and 8th grade woodshop projects—gumball machine, foldable stool—and for some reason, to my wife’s chagrin, love making my apartment’s wood floor creak. I was bummed to learn that, in 2017, a plan to build a 10-story timber condo in New York City was scrapped (“the cooling-off of NYC’s condo market,” according to the website Curbed, “made the deal seem less attractive.”) But Quayside’s wood-centric vision of future cities has me feeling optimistic. “Timber construction is possible at all scales and at pioneering height,” a Quayside document states. We’ll have to see if that confidence catches on, in Newark and beyond.

