Sigma Labs Inc. (NASDAQ: SGLB) Strives to Help Aer
Post# of 382
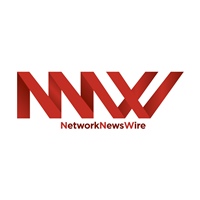
- 3D-printed weight-optimized and flow-optimized parts significantly improve the performance of aircraft and rockets
- Global aerospace 3D-printing market estimated at $1.4 billion in 2018, projected to reach $6.8 billion by 2026
- Sigma Labs’ breakthrough quality-assurance solution PrintRite3D® set to revolutionize 3D-printing industry, enabling it to grow globally
Sigma Labs Inc. (NASDAQ: SGLB) is set to exploit the tremendous aerospace 3D-printing-market growth potential with its revolutionary in-process, quality-assurance technology. This technology is poised to help the industry scale a critical hurdle: ensuring effective and efficient quality in real time.
The global aerospace 3D-printing market was estimated at $1.4 billion in 2018, projected to reach $6.8 billion by 2026 with an expected CAGR in excess of 22% during the forecast period. The airline and spacecraft segment is expected to lead the aerospace 3D-printing market due to the need for low-volume, low-weight parts that can be manufactured using 3D-printing technologies, which reduces supply chain constraints, minimizes warehouse space and lowers waste materials compared to traditional manufacturing processes (http://nnw.fm/H4tjI).
As the industry is challenged by environmental restrictions, high manufacturing cost and a competitive market environment, 3D metal components manufacturing offers a unique solution to help overcome much of these challenges.
Weight is considered the most important feature in the design and development of an aircraft because of its tremendous impact on fuel consumption. 3D-printing technology can help build lighter fuel-saving aircraft parts, a characteristic essential in an industry that operates at low-profit margins. Additive manufacturing provides advanced manufacturing techniques for developing the components, parts while maintaining the strength and aerodynamic features of an aircraft. This is an important motivating factor for airlines to procure newer generation aircraft, which will drive the growth of the additive-manufacturing sector. The aircraft segment currently holds the major share in 3D printing for the aerospace and defense market.
3D-printing technology also provides companies with a critical competitive advantage as it offers the flexibility to design and test products multiple times and quickly build prototypes, helping companies to cost effectively reduce uncertainties and improve the functionality of their products, thereby accelerating design cycles and reducing time to market.
By making the production process of components faster, cheaper, and simpler, while also enabling the seamless integration of components into a single structure and reducing the need for external joints, fasteners and adhesives, additive manufacturing has attracted interest from major aircraft manufacturers such as Boeing and Airbus B.V. as well as component producers such as Rolls-Royce, Pratt & Whitney and GE Aviation.
However, 3D-printing technology is facing a significant technical hurdle: real-time process monitoring and control. Due to variability in the 3D-printing process, consistent quality of produced parts is not reliably achieved without postproduction inspection, which is time consuming, costly and results in high rejection costs. Since components and parts can currently be inspected only by CT scans and other means, the producer doesn’t know until the end of the process if the finished parts meet design specifications, resulting in lost time and profits as well as the inability to economically scale up production.
Sigma Labs is revolutionizing the traditional quality assurance process with its quality-assurance software that operates in real-time, in process as parts are being formed unlike any other quality-assurance software on the market, Sigma Labs’ PrintRite3D® is a unique third-party validated software that enables real-time monitoring, analysis, feedback and control during the 3D-printing process of precision metal parts. PrintRite3D detects defects during the production process while providing feedback to machine operators allowing corrective actions to be taken, leading to faster production of metal parts with fewer errors and a more uniform product. Users will realize results in decreased downtime and waste while increasing yield and profits for 3D-printing companies.
Compared to its competitors, Sigma Labs’ PrintRite3D provides users with a superior solution. Most other solutions do not offer features such as crucial calibration filters, raw data export, machine-learning-enabled automated anomaly detection, and 3D thermal data visualization. Within the rapidly growing aerospace sector, Sigma Labs has been recognized as a superior solution to the industry’s critical needs and, as such, was selected by the industry-leading producer Airbus earlier this year to deploy its PrintRite3D Rapid Test and Evaluation Program.
With tier-1 clients such as Airbus, Siemens, Pratt & Whitney and Honeywell evaluating the software, Sigma Labs is on a clear path to grow significantly in 2020. The company is uniquely positioned to capture a significant part of the sizable addressable market with its proprietary technology that enables the entire 3D-metal-printing industry to overcome the single most-significant barrier to adoption in serial production.
For more information, visit the company’s website at www.SigmaLabsInc.com
Please see full disclaimers on the NetworkNewsWire website applicable to all content provided by NNW, wherever published or re-published: http://NNW.fm/Disclaimer

