GLGI..complete DD package.. Company Profile
Post# of 36355
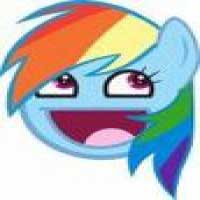
GLGI..complete DD package..
Company Profile
Greystone Logistics, Inc., through its subsidiaries, engages in manufacturing and selling plastic pallets; and grinding, pelletizing, and selling recycled plastic resins primarily in the United States. It offers rackable, nestable, display, monoblock, and stackable pallets, as well as picture frame, Web-top pallets produced using a proprietary blend of recycled plastics. Pallets are primarily used in the automotive, chemical, consumer products, grocery, produce and food production, paper and forest products, retailing, and steel and metals industries. The company also sells recycled plastic that has been reprocessed into pellet form; and provides pallet leasing services. It primarily serves the beverage and pharmaceutical industries. Greystone Logistics, Inc. sells its products through direct sales staff and a network of independent contractor distributors. The company was formerly known as PalWeb Corporation and changed its name to Greystone Logistics, Inc. on March 18 2005. Greystone Logistics, Inc. was founded in 1969 and is based in Tulsa, Oklahoma.
----------------------------------------------------------------------------
Shares Outstanding 26,111,201 a/o Apr 12, 2012
Float 15,500,000
Authorized Shares Not Available
Shareholders of Record 333 a/o Sep 14, 2010
----------------------------------------------------------------------------
1613 E. 15th Tulsa, OK 74120
Website: http://www.greystonelogistics.com
Phone: (918) 583-7441
investorrelations@greystonelogistics.com
----------------------------------------------------------------------------
Insider Ownership 12,573,703
Insider transactions
Jun 12, 2012 KRUGER WARREN F Director 16,632 Direct Purchase at $0.08 per share.
May 28, 2012 KRUGER WARREN F Director 10,000 Direct Purchase at $0.11 per share.
May 7, 2012 KRUGER WARREN F Director 17,500 Direct Purchase at $0.10 per share.
Mar 13, 2012 KRUGER WARREN F Director 4,761 Direct Purchase at $0.08 per share.
Mar 9, 2012 KRUGER WARREN F Director 40 Direct Purchase at $0.08 per share.
Feb 29, 2012 KRUGER WARREN F Director 7,699 Direct Purchase at $0.01 per share.
Feb 3, 2012 KRUGER WARREN F Director 10,000 Direct Purchase at $0.10 per share.
Dec 4, 2011 KRUGER WARREN F Director 13,561 Direct Purchase at $0.08 per share.
Feb 15, 2011 KRUGER WARREN F Director 40,000 Direct Purchase at $0.06 per share.
Dec 12, 2010 KRUGER WARREN F Director 7,800 Direct Purchase at $0.08 per share.
Dec 8, 2010 KRUGER WARREN F Director 2,200 Direct Purchase at $0.09 per share.
Dec 6, 2010 KRUGER WARREN F Director 15,000 Direct Purchase at $0.09 per share.
Nov 28, 2010 KRUGER WARREN F Director 25,000 Direct Purchase at $0.09 per share.
Jul 14, 2010 KRUGER WARREN F Director 7,522 Indirect Purchase at $0.15 per share.
----------------------------------------------------------------------------
10Q for period ending 2-29-2012
http://yahoo.brand.edgar-online.com/displayfi...-12-000334
10Q for period ending 11-30-2011
http://yahoo.brand.edgar-online.com/displayfi...-12-000013
10Q for period ending 8-31-2011
http://yahoo.brand.edgar-online.com/displayfi...-11-000797
10k for period ending 5-31-2111
http://yahoo.brand.edgar-online.com/displayfi...-11-000735
----------------
Articles link to: http://www.greystonelogistics.com/index_news.php
TULSA, OK--(Marketwire -07/10/12)- Greystone Logistics, Inc. (GLGI). Customer demand in the fourth quarter for a broad range of recycled plastic shipping pallets and steady sales volume for reprocessed plastic for resale drove record sales and income at Greystone for the year ending May 31, 201 2 ("Greystone Logistics" or the "Company").
Tulsa-based Greystone Logistics recorded sales for the corporate year ending May 31, 2012, or fiscal year 2012, of $24,186,047 compared to $20,501,824 in fiscal year 2011 for an increase of $3,684,223 or 18%. The Company recorded net income of $2,323,756 during fiscal year 2012 compared to a net loss of (847,204) in fiscal year 2011 for an increase of $3,170,963. Net income available to the common shareholders of Greystone Logistics for fiscal year 2012 was $1,934,039, or $.07 per share, compared to a net loss in fiscal year 2011 of $(770,095), or ($.03) per share. Earnings before interest taxes depreciation or amortization (EBITDA) for the Company, excluding EBITDA with respect to non-controlling interests, were $3,889,956 for fiscal year 2012.
Warren Kruger, CEO, stated, "Our entire organization is delivering on the Company's goals and producing results that are in line with the expectations laid out in our business plan. The diligence and patience exhibited while working through an extended series of challenges and opportunities is being rewarded. Plastic pallets are more frequently being recognized as a necessity rather than a luxury and our 100% recycled plastic products help the environment while providing sustainable money-saving solutions. Growth is coming from a broad range of products with concentrations in the beverage, agriculture, and pharmaceutical industries." Kruger continued, "Looking ahead to our corporate fiscal year 2013, we will earnestly continue to build value for our shareholders as I anticipate a double digit increase in revenue from resin sales, current pallet designs and new products and innovations in the pipeline."
Greystone Logistics is a "Green" manufacturing and leasing company that reprocesses and sells recycled plastic and designs, manufactures, sells and leases high-quality 100% recycled plastic pallets that provide logistical solutions needed by a wide range of industries such as food and beverage, automotive, chemical, pharmaceutical and consumer products. The Company's technology, including that used in its injection molding equipment, proprietary blend of recycled plastic resins and patented pallet designs, allows production of high-quality pallets quickly and at lower costs than many processes. The recycled plastic for its pallets helps control material costs while reducing environmental waste and provides cost advantages over users of virgin resin. Excess plastic not used in production of pallets is reprocessed for resale.
----------------------------------------------------------------------------
White Paper on the Pallet Industry and Greystone Logistics
Greystone Logistics - Manufacturer of 100% Recycled Plastic Pallets
by Warren F. Kruger, CEO
EXECUTIVE SUMMARY
Greystone Logistics, Inc (“Greystone” or “the Company”) is a manufacturer of plastic pallets made from recycled plastic. The company moved through the research and development phase and is growing rapidly based on a unique proprietary process for the manufacture of pallets from recycled plastic for delivery to the beverage, manufacturing, pharmaceutical and other industries. Greystone’s recycled plastic pallet design offers significant competitive advantages over plastic pallets made out of virgin resin and the traditional wood pallet. These range from pallet strength, stiffness, durability and RFID tagging capabilities to pricing and cost of use. The Company did not embark on designing its pallet product on speculation that market demand would follow; rather, seven years of research and development emanated from a specific request of The Miller Brewing Company for a plastic pallet to begin replacement of its wood pallet inventory. The Company business plan includes a third-party pallet management strategy to lease their pallets in closed loop logistical environments. The 500-800 million pallets going into the system each year create an estimated $6 billion dollar industry.
Greystone believes there is a substantial market for the replacement of wood pallets with recycled plastic pallets, amounting to an opportunity to bring about a paradigm shift in the pallet industry. The high cost of research and development, molds, equipment, testing, facilities, proprietary processes, patents, channels of distribution, long sales cycles, customer loyalty and accumulated tacit knowledge create significant barriers to entry for those considering entering the plastic pallet industry.
Pallets are used worldwide for the transportation of goods and they are primarily made of wood (approximately 97%). According to the William H. Sardo Jr. Pallet and Container Research Laboratory at Virginia Tech University and its director Dr. Marshall S. “Mark” White, in 2004 814 million pallets were manufactured or repaired with 800 million of those being wood pallets. Primary industry users of pallets include food (approximately 30%), chemicals and pharmaceuticals (approximately 14%), government (approximately 4%), dairy (approximately 3%) and beverage (approximately 3%).
Wood pallets have always presented industry users with operating challenges because of factors such as breakage, damage to inventory and inability to incorporate Radio Frequency Identification (“RFID”) tags. Furthermore, with the incorporation of sophisticated logistics systems shipping, automated warehousing and stocking systems the aforementioned operating challenges are further complicated by difficulties wood pallets present in alignment and movement with automated equipment. The infestation risk (in the wood itself or by the fumigation chemicals applied to the wood pallets) of wood pallets is also an issue in export markets. Plastic pallets overcome these operating challenges.
The Company has developed patents and proprietary processes, including recycled resin blends, which produce a plastic pallet that is aggressively price competitive with virgin resin pallets and has far greater cost efficiency than wood pallets. Greystone pallets cost approximately half of virgin resin pallets of similar weight and performance produced by competitors. Because plastic pallets can last over one hundred trip cycles and are recyclable, they have substantial advantages on a total cost basis over wood pallets that require repair every three trips at an average cost of $3. The Greystone product provides these significant price and cost advantages without sacrificing key product characteristics, including strength, stiffness and durability.
Greystone’s proprietary resin blend for pallet production can be sourced from abundant post-industrial and post-consumer recyclables. These items are available from manufacturers, recyclers and landfill operators and are in abundant supply, providing the Company with a substantial competitive advantage versus the raw material costs of its virgin resin pallet competitors.
The manufacturing process begins with the proper selection and blending of the raw materials, which is a proprietary process of the Company developed over years of research and development. The resin blend is then heated and injected into a mold designed for the proper size and function of the pallet. Once the pallet parts are molded, they are assembled (addition of fiberglass I-beams for stiffness, anti-skid grommets installed and the component parts snapped together). The manufacturing facility operates on a 24/7 basis with the exception of maintenance and holiday shutdowns.
The market for the replacement of wood pallets is in the hundreds of millions. Greystone believes that the adoption of plastic pallets will be led by major manufacturers and retailers. Although these entities have substantial capital resources to purchase pallets for their use, the Company believes there also is an enormous leasing/servicing opportunity. The largest player in the United States and the world in pallet pooling is CHEP International, a division of Brambles, with 85 million wood pallets (all 48 x 40 inches) in circulation in the United States and 200 million in inventory worldwide.
The company has expanded from the original 40x32 molds and now has sizes that include 48x40, 48x44, 37x37 and a low weight, low cost 48x40 nestable.
The Greystone management team combines operating experience at the highest level of the pallet and logistics industries as well as general manufacturing. Greystone manufacturing operates out of 120,000 square foot facilities in Bettendorf, IA and employs 100 people.
GREYSTONE LOGISTICS 48X40 GMA PALLET
Pallets are a six billion dollar annual industry in the U.S.
Following is Greystone Logistics (GLGI) company data, information on the GMA pallet, a discourse on the benefits of plastic over wood, review of demand, and a review of the next generation of 48x40 full picture frame bottom recycled plastic pallet for Greystone Logistics’ product line. The requirement for RFID Tags and ASAR requirements are mandating this explosive growth. Wood cannot utilize RFID effectively to meet ASAR standards.
Plastic pallets are superior to wood. The opportunity for growth of plastic pallets to replace wood has been limited because of price, weight, and racking ability. Plastic pallets have a residual (trade in) value because of the plastic commodity utilized in the product. This residual value and the cost-per-trip make a plastic pallet substantially less costly than wood.
Wood hinders 100% reading of RFID Tags. Greystone Logistics is a low cost recycled plastic pallet producer using 100% recycled resin for competitive pricing, a patented design with lower weight, and fiberglass rods for structural integrity. The company is achieving scale and continuing to grow its production capabilities using proprietary secret knowledge and processes. The new pallet sizes including the 48x40 pallet provide a broad opportunity for the right products at the right price in scale. As an example, CHEP Leasing has over $1 billion dollars of wood 48x40 pallets in their U.S. pool inventory and annual lease revenues in excess of a billion dollars on this inventory.
Greystone has manufactured and delivered millions of 40x32 beverage pallets for Miller Brewing with fiberglass supports that consistently carry up to 2300 pounds per pallet and four times that amount in a static stacked environment. There is no test more telling than that of real world use. The company develops recycled plastic pallets that have physical and performance characteristics required by specific customers. These include low cost, safe designs, high standards of quality and performance features for the integration and implementation of plastic pallets. The advantages and benefits of properly utilized recycled plastic pallets are changing the pallet landscape in the material handling industry particularly with RFID Tag ability, structural integrity and cost/benefits value.
INFORMATION ON PALLET INDUSTRY-GMA STANDARD 48X40
Pallets are devices used for moving and storing freight. It is used as a base for assembling, storing, stacking, handling, and transporting goods as a unit load. The pallet is so constructed to facilitate the placement of a lift truck’s forks between the levels of a platform so it may be moved easily.
The most common size pallet is the 48x40 4-way pallet or otherwise referred to as the GMA (Grocery Manufacturer Association) pallet. Sometimes known in the industry as the “GMA Pallet,” “The GMA Pallet,” “GMA 48x40 Pallet,” or “GMA Block Pallet.” The GMA acts as a commodity in the pallet industry, as price is often determined by availability. As wood pallets move through their life cycle from a new pallet to a used pallet, they are repaired and put back in service until they are land filled or used as wood compost.
The following design specifications are sought after by the Grocery Manufacturers pallet subcommittee all of which can be provided by a Greystone 48x40 recycled plastic pallet with fiberglass support:
True four-way entry capability
A size of 48x40
A weight 7-15 pounds less than A grade (CHEP) pallets
Sufficient top and bottom deck coverage to prevent product damage
Construction with reusable, renewable, and/or recyclable material
Necessary sanitation, moisture resistance, ventilation, and drainage to handle certain product categories, such as meat and produce
The use of high-quality pallets for consistency and lower per trip costs
Pallets are the primary interface between the packaged product and today’s highly automated material handling equipment. Today, approximately 90% of the U.S. domestic product is shipped on pallets. Although pallets are not the most glamorous part of the warehouse, they are important because users have expectations based on specifications and wood pallets lack critical manufacturing details that determine performance. The end user becomes frustrated when these pallets do not perform to expectation. This angst is aggravated when new multi-million dollar automated systems are in use.
Warehouses that use pallets, and equipment designers that recommend pallet designs for their systems, need to accurately specify the pallet quality level required for these systems. This paper lists the important aspects of accurate consistent specifications that can be provided with a 48x40 recycled plastic pallet with fiberglass rod support.
During the past two decades both timber prices and landfill fees have increased and have compelled businesses to modify the way pallets are managed. This fact sheet examines how businesses can evaluate and improve their pallet management systems and reduce associated waste by utilizing plastic recycled pallets.
Pallets made from plastic are a long-lasting alternative to wooden pallets in closed loop systems. Plastic is durable, reusable, easy to clean, and recyclable. Despite higher initial costs, these pallets save money in the long run due to money back guarantees of between $10-$22.50 (residual value) depending on the weight of the pallet. This residual value is due to the ability to recycle the commodity (resin). Wood lasts 1-4 years including multiple repairs. Plastic pallets can last at least 10 years with no repair costs. According to the Purdue University AGVS Research Group, the average life of these pallets is 100 trips, where one trip is defined as five handlings. These pallets usually meet both USDA and FDA standards for pharmaceutical, chemical, grocery and food processing operations as they can be sanitized and steam cleaned. They also exhibit low breakage rates and work well with automated material handling systems. Product damage is lowered, and employee safety is increased when using these pallets because they have no nails, staples, or broken boards. When damaged, however, the rods can be pushed for reuse and the pallet ground to use the resin again.
Closed Loop System
Plastic is best used in a closed loop or slave system where shipping is restricted to moving goods within or between specified plants and facilities. Closed loop systems operate best under one or more of the following conditions: short distance shipments, frequent deliveries to the same customer, delivery to a limited number of customers, and/or delivering with company owned vehicles.
Plastic pallets emulate the benefits of wood but have no nails, screws, or staples, thus reducing product damage and employee injuries. Because of the fiberglass rods, heat and weight are not a detriment because they don’t bend under open racking conditions in the same manner.
Pallet Standardization
Standardizing pallets provide optimum reusability and recycling. The Greystone process is injection molded. Plastic is injected, under pressure into a closed cavity mold. The material is cooled to ensure it maintains the exact shape of the mold. This process produces a high strength to weight ratio, reduces deflection, has accurate tolerances, is cleanable and has a superior static capacity for racking, impact resistance, distribution, stacking and automated standard racking equipment. Using one standard size will reduce pallet inventory needed and labor needed for sorting different pallet sizes. Recycling in the wood industry usually entails grinding the pallets to wood fiber for use as landscape mulch, playground bedding, animal bedding, compost, soil amendment, or biomass fuel all at minimal asset recovery value.
Third Party Management
The development of third-party pallet management companies and networks of individual pallet companies provides an efficient way for companies to manage their pallets. Third party management companies manage a user’s existing pool of pallets or rent pallets to the user on a per trip basis. The management company tracks pallets throughout their usage and retrieves them for reuse. Third party systems need higher quality pallets, and with plastic can increase the trips per pallet an average of 20 to 40 times compared to five times when managed by the user. Tracking and computerization is available throughout sourcing. At the end of the useful life, the plastic pallet has residual value and can be ground up and the resin used again.
Five Reasons to Utilize Plastic Recycled Pallets in a Third-Party Pallet Management Pool
Shipping vibrations can cause product damage for some products
Grommets used in the Greystone process provide anti-skid and cushioning combined with stiffer decks, which increase the resonant frequency, which transmit fewer shipping vibrations to the product and thus less damage.
Consistency in the manufacture of the recycled plastic pallets reduces error
Rigid, flatter deck consistency of plastic pallets will prevent deck bend and will transfer a greater percentage of product weight away from the rigid pallet blocks thus distributing the product weight over more of the pallet footprint, and reducing product damage. When damaged by fork lifts, the pallet can be recycled and has a residual value.
A specified minimum pallet Coefficient of Friction is provided
Low friction plastic is modified by the use of grommets to ensure superior performance. Excellent top deck grommet coverage for anti-skid, forklift tines contact points, and surface contact points to prevent “creep” in the back of trucks are all significant benefits of the Greystone anti-skid grommets.
Avoidance of moisture
Most wood lumber pallets are manufactured at a "green" moisture content, or 40-60% moisture content. Plastic is dry at manufacture. Dry pallets offer stiffer decks, the potential for tighter dimensional tolerances, and fewer moisture problems associated with RFID reading, shrinkage, warping, and bug and biological infestation.
Automated Material Handling Systems require high quality, consistent pallets
Specification outlines such things as size tolerances, square fit, and flatness. Higher quality plastic pallets meet these specifications.
Progressive industries and world-class companies are converting from wood pallets to plastic pallets for work-in-process, storage and distribution applications. Quickly plastic pallets are recognized for their economic, ergonomic and environmental benefits. In a closed loop system, plastic pallets make a tremendous number of trips before being recycled. On a per trip basis, plastic pallets represent great savings over wood pallets. Plastic pallets rapidly realize a return on initial investment and continue to perform during the course of their service life.
Plastic pallets provide a safe and comfortable handling solution, which improves workplace safety. They are dimensionally stable, consistent in weight and non-porous. In most cases, they are lighter than A grade wood pallets and their smooth and contoured construction is free of nails, splinters and rust.
Production Process
Greystone uses proprietary processes and recycled resin blends, developed over the last seven years, to produce its pallets. The use of recycled resin allows the Company to effectively compete on price in the marketplace without sacrificing pallet strength, stiffness or durability. Greystone has developed tacit knowledge of resin blends and production innovations considered trade secrets that afford a level of protection and a barrier for competitors to overcome.
Raw materials are purchased from suppliers and shipped into Greystone’s manufacturing facility in Bettendorf, IA.
After the raw material arrives at the manufacturing facility, it is separated and sorted. The sorting is done to separate the different resins that compose Greystone’s proprietary mix. The Company presently has in house grinding capacity of over 100,000 pounds per day and a pelletizing line to take low grade resin and create a useable plastic pellet.
The melted resin mix is injected into molding equipment to produce the component parts of the pallets. The fiberglass beams reinforce the strength and stiffness as well as increase the durability of the pallet. The reliability of the design has been proven in the marketplace to date as annually only one and one half percent of the production of plastic pallets were returned because of customer damage.
Pallet Market Size
Pallets are used worldwide for the transportation of goods and they are primarily made of wood. There are an estimated 1.9 to 2.0 billion pallets in circulation daily in the United States (an estimated 97% wood pallets and 3% plastic or other pallets). In 2004 the William H. Sardo Jr. Pallet and Container Research Laboratory at Virginia Tech University under the direction of Dr. Marshall S. “Mark” White estimated total pallet production in the United States at 814 million broken down as follows:
500 million new wood pallets
300 million repaired and used wood pallets
8.3 million plastic pallets
5.5 million corrugated paperboard pallets
1.1 million metal pallets
Plastic versus Wood Pallets
The demand for plastic pallets is rising rapidly because of the inherent benefits of plastic over wood pallets. Plastic pallets are lighter than wood pallets, less prone to breakage and much longer lasting. Over the last few years, as manufacturers and shippers of goods have streamlined their processes through automation, they have begun to seek reliable pallets that do not break constantly, hold their shape and are sanitary. Foreign governments in Europe and China have curtailed the use of wood pallets for the importation of goods because of fear of contamination and infestation.
At the same time, the strategic importance of inventory control systems have made it critical that shipments are tracked throughout their cycle. There is a rapidly increasing demand for the use of Radio Frequency Identification (“RFID”) tags to facilitate the tracking of shipped goods. In particular, pharmaceutical customers require RFID tags to track product shipments in the case of a recall. RFID tags do not work well with wood pallets because the moisture content of wood creates installation difficulties for the RFID tags and scanning interference problems. Entities such as Wal-Mart, Target, Circuit City and Best Buy have announced and are establishing internal guidelines requiring manufacturers to use RFID by 2006. New Department of Defense, Homeland Security and environmental regulations are creating a substantial imperative towards the use of plastic pallets imbedded with RFID tags. Greystone will install customer provided RFID tags.
From a financial perspective, multiple-cycle wood pallets can last for up to a three trip cycle before repair is mandatory. The cost of such repair is approximately $3.00 per pallet per repair. In comparison, plastic pallets can last for approximately a 100 trip cycle and can be returned for recycling at a residual price of close to 40% of initial selling price.
Competition – Manufacturing and Services
The wood pallet and container industry consumes nearly 35% of all hardwood produced in the United States according to the National Hardwood Lumber Association (NHLA). Data from the William H. Sardo Jr. Pallet and Container Research Laboratory at Virginia Tech University and its Director D. Marshall (Mark) White places the use of wood for pallet manufacturing at 12% of all lumber produced in the United States. There are over 400 different pallet sizes used by companies in the United States. The most widely used size, comprising 30% of all sizes, is the 48” x 40” (1219 x 1016 mm) pallet used by the grocery, produce and the consumer packaged goods industries, commonly referred to as GMA (Grocery Manufacturer Association) pallets (Source: Ibis World) Estimates by Ibis World and the Sardo Laboratory place the annual revenues of the wood container and pallet industry currently at around $5 to $5.5 billion. The value added component of the revenue estimate is about 45%-47%. The wood pallet and container industry is by no means concentrated, with roughly 2,500 – 3,000 pallet manufacturers and recyclers in operation. The estimated breakdown of wood pallet manufacturers is as follows:
44% manufacture new pallets only
47% manufacture new pallets and recovered use pallets (repair)
9% manufacture recovered use pallets only
Estimates of wood pallet manufacturing industry capacity utilization are at less than 60% in 2000 (Source: Sardo Laboratory). Industry employment in the 2002-03 calendar years was estimated at 46,000 (a range of 15 – 18 employees per firm on average). Capital investment in the industry was estimated in 2002 at $95-$100 million (roughly $35K per firm at the midpoint of the range). Ibis World forecasts modest industry growth over the next few years with little change in industry structure. Greystone believes that a gradual shifting from wood pallets to plastic pallets will take
place over time. Because of the lack of concentration among wood pallet manufacturers, there is a lesser risk of coordinated response (price, performance) against the penetration of plastic pallets. Wood is also a resource which faces environmental pressures (logging issues) as well as possible substantial overseas demand (China).
The largest industry users of pallets such as the food, chemical, pharmaceutical, beverage and dairy industries are populated with large public or private entities for which profitable financial performance is paramount. The operating issues presented by wood pallets have been tolerated to date as there has been no viable alternative in sufficient size for replacement. The performance of plastic pallets for Miller Brewing is a sterling case study of the benefits plastic pallets can bring to these large entities.
The manufacturing competition includes Buckhorn, Orbis, and Rehrig Pacific and some small single product producers.
The leasing/servicing sector in the United States is dominated by CHEP, a subsidiary of the Australian company Brambles. CHEP has worldwide sales of approximately $2.5 billion and a leasing pool in the United States of 85 million wood pallets. CHEP has only wood pallets in circulation (48” x 40”). A smaller competitor, PECO, based in New York has a pallet pool of 750K. PECO has been able to carve out a competitive position through its software and logistics infrastructure as well as its industry focus.
Summary
A paradigm shift from wood to plastic pallets is occurring with the recycle plastic pallets Greystone is making available. This company will succeed because it is providing the right products and leasing opportunities at the right prices for a willing and open market.
----------------------------------------------------------------------------
ABCs of Recycled Plastics
http://www.eia.doe.gov/kids/energyfacts/savin...ml#plastic
----------------------------------------------------------------------------
An interview with Warren Kruger CEO of Greystone Logistics
What does Greystone do?
Greystone is a high growth manufacturing and leasing company that designs, manufactures, sells and leases high quality 100% recycled plastic shipping pallets that provide logistics solutions needed by a wide range of industries such as the food and beverage, automotive, chemical, and pharmaceutical and consumer product industries. The company utilizes proprietary technologies and designs to produce high quality, recycled plastic pallets at a lower cost than competitors. The company’s patented designs yield pallets that combine low cost with light-weight, strength, and durability. Greystone Logistics is the largest 100% recycled plastic pallet manufacturer in U.S. Greystone also reprocesses and repelletizes plastic for resale in the open market.
Could you start with a history of the company?
This micro cap public company sustained significant losses since it’s inception as a marine paint manufacturing company in 1968. The company was dormant for years before a group of investors embarked on a business plan for the public company that involved a high risk, capital intensive plan to become a leading manufacturer in the burgeoning plastic pallet industry. Concern over my initial significant private placement investment led me to take over as CEO in January of 2003. Our team diligently worked the business plan under financial duress never losing faith that the company would be a success to become the leading manufacturer of recycled plastic pallets and plastic resin.
What can you tell us of the market opportunity for selling these high-quality plastic pallets?
We offer a variety of low-cost, high-value recycled pallets on our own design, including a beverage size pallet, a standard size rackable pallet, and a nestable pallet. The size of the industry will be astounding for many. This is a $6 billion market annually in the U.S. alone, with 600 million new platforms of all types entering the system per year. The average selling price for multiple-use recycled plastic pallets is lower than wood when you factor in the residual credit we give our customers for the value of the plastic. Like our customer, Miller Brewing, many other beverage companies, drug companies, and other industries are finally making the decision to move to plastic. Greystone currently has a multi-year relationship as the only plastic pallet provider for Miller Brewing. Our top-tier clients include Miller Brewing, Apotex Pharmaceuticals, Pfizer, Merck, Coors Brewing and many others. As you can imagine, wood is a problem. Broken boards, wood chips, bugs, and cleanliness are always issues.
The profit opportunity lies not only in the manufacture of recycled plastic pallets but in the leasing on a per trip basis of the plastic pallet. In North America there are two leasing companies in the pallet market with sales of well in excess of a billion dollars annually; Brambles, an Australian based company with a U.S. division called CHEP and another much smaller company called PECO Leasing. The future of the leasing industry will include recycled plastic pallets. Many of these potential users are investment grade companies that have closed loop pallet utilization that are perfect for plastic. CHEP with 85 million wood pallets under lease versus 750,000 for PECO has an unfavorable potential exposure to wood and faces probable residual value erosion.
Greystone is currently negotiating with numerous large companies to implement a closed loop Plastic Pallet Lease Pool. Greystone has an agreement with a logistics company for recovery. Greystone would provide a low-cost source of pallets for the leasing company plus a guaranteed strong residual value for the pallets. The lessee obtains compelling economic benefits by switching to recycled plastic pallets.
What unique qualities of Greystone give you a competitive advantage within your market space?
We have developed technology and proprietary recycled blends and processes to become the low-cost producer. There is a significant push on doing business with companies that provide environmental friendly alternatives and at Greystone we don’t just talk “green” we do “green” using upwards of 30 million pounds annually of post industrial plastic that otherwise may have ended up in landfill. We have patented designs on our pallets that utilize fiberglass for strength within the plastic pallet. Our production staff understands working with recycled material, which is a totally different process than using virgin material. In the past, high-priced plastic pallets and fear of change prevented a more significant move to plastic. Using our own regrind allows a pricing point at a level that competes with the cost of wood pallets.
Can you give an example of another industry segment where Greystone's products and services are being offered and in which industries are you planning to grow?
The pharmaceutical industry, like the beverage industry, is also moving rapidly to get away from wood. Pfizer Pharmaceutical has been a great client of ours for some time, as has Merck and Apotex, which is a large, generic drug pharmaceutical firm. We intend to focus on providing 40x48 pallets for leasing while insuring our existing clients long term needs are met.
What are some of the major trends you see affecting your core business?
The environmental mentality and social consciousness of all nations continues to improve. In the food and drug industry in Europe, wooden pallets are being phased out. Import and export regulations are being tightened and more strictly monitored to prevent biological and insect infestation in the U.S., Europe, China, Australia, New Zealand, Mexico, and many other nations. No more soft wood pallets are allowed - only hard wood, kiln-dried, fumigated, stamped pallets are supposed to be sent. We have also witnessed what the mad cow scare can do to the beef industry. You can see why a plastic pallet is a much better alternative for both cleanliness and environmental reasons.
How do you believe your Company can capitalize on these trends?
Greystone will continue to be the low-cost producer. Our sales efforts have already produced results within Miller Brewing, Coors Brewing, Pfizer, Apotex, West Pharmaceutical and Merck. Our customer base grows daily as clients finally make that commitment to make the transition from wood to plastic. We are there for them with a great product at a great value.
What key goals and strategies are you focusing on to ensure future success?
We will aggressively manage costs and strive to be the low cost producer. High capital costs will be a barrier to entry for all but a few. For a company of our size, this number is significant. Our cost of recycled resin is approximately $ .05 a pound lower in Iowa due to operating efficiencies and less than one-half the cost of virgin resin.
Based on your vision and accomplishments, what can you tell us about the next 2 to 3 years for your company?
The next 2 to 3 years we will be very, very exciting. Volume will allow us to be profitable and the cost savings in our resin purchase strategy that we have gone through in the last year and processing equipment being added will further lower resin costs. Greystone is excited about our sales prospects and the way the entire market is moving. Our sales growth continues to be double digit and I would anticipate sales for year end May 31, 2011 will finish at $21 million with slightly lower than last year operating profits because of the surge spending for infrastructure for sales growth. We have the capacity on our existing equipment to take us over the $25 million in sales, with relatively limited additional capital cost. With correct capitalization we could achieve $50 million in sales within three years.
To summarize the value proposition in Greystone Logistics, why should one track and follow this company near-term and beyond?
The materials handling industry is a $6 billion market in the U.S with over 600 million platforms of some type going in the system each year. Finally, here is a company that has recently come out of the developmental stage with business in hand; approaching consistent profitability; with the patented designs, product line, proprietary technology and know-how to compete with wood pricing. We have first mover advantage in the plastic pallet lease opportunity which we intend to exploit. This coupled with the regulatory mandates and changing attitude toward moving to plastic, put Greystone in position to leverage on this demand. We are the only pure-play public entity in this space with management absolutely aligned with driving the company business.
----------------------------------------------------------------------------
Greystone Logistics, Inc. Announces Recycling Award
Monday October 30, 2006 9:30 am ET
TULSA, OK--(MARKET WIRE)--Oct 30, 2006 -- The Iowa Recycling Association has selected Greystone Manufacturing, a subsidiary of Greystone Logistics, Inc. (OTC BB:GLGI.OB - News), as the 2006 Iowa Recycling Association's "Recycled Product Manufacturing Award Winner."
Greystone Manufacturing, located in Bettendorf, Iowa, manufactures 100% recycled content plastic pallets. The company grinds and utilizes millions of pounds of polyethylene (PE), polypropylene (PP), and polyolefin (TPO) plastics. Greystone works with generators, collectors, and processors of plastic and is conscientiously working to decrease the amount of waste sent to landfill.
About Greystone Logistics, Inc.
Greystone is a plastic pallet manufacturer that utilizes patented proprietary technologies and designs to produce high quality, recycled plastic pallets. Greystone serves the beverage, pharmaceutical and other industries.
Forward-Looking Statements
This press release includes certain statements that may be deemed "forward-looking statements" within the meaning of the federal securities laws. All statements, other than statements of historical facts, that address activities, events or developments that Greystone expects, believes or anticipates will or may occur in the future, including the potential sales of pallets, the improvement of operating results or other possible business developments, are forward-looking statements. Such statements are subject to a number of assumptions, risks and uncertainties. The forward-looking statements above could be affected by any of the following factors: Greystone's prospects could be affected by changes in availability of raw materials, competition, rapid technological change and new legislation regarding environmental matters; Greystone may not be able to secure additional financing necessary to sustain and grow its operations; and a material portion of Greystone's business is and will be dependent upon a few large customers and there is no assurance that Greystone will be able to retain such customers. These risks and other risks that could affect Greystone's business are more fully described in its reports filed with the Securities and Exchange Commission, including Greystone's Form 10-KSB for the fiscal year ended May 31, 2004. Actual results may vary materially from the forward-looking statements. Greystone undertakes no duty to update any of the forward-looking statements in this release.
----------------------------------------------------------------------------
The EPA on the Benefits of Plastic Pallets
http://www.epa.gov/epaoswer/non-hw/green/tools/pallets.pdf
----------------------------------------------------------------------------
Plastic Shipping Pallets Used for Rental and Pooling
Shipping Pallets
Shipping pallets are among the smallest but most crucial pieces of an efficient shipping or warehousing operation. If you’re moving products, you need to be able to depend on your shipping pallets. At Greystone Logistics, we offer dependable plastic shipping pallets that you can count on, offering you peace of mind through dependable, durable pallets. Buy pallets new or use our services for pallet rental and pooling. In the industry today, pallet rental and pooling is an increasingly popular option to maximize your dollars for the most efficient operations. For customers who don’t need years of service out of their skids, or who can share the use of their pallets at different times, pallet rental and pooling is the most logical choice. Our pallets have become the most popular in the industry simply because they’re dependable and shippers know it. Plastic is overtaking wood as the material of choice for pallets. It lasts as much as 50 times longer than wood and it retains a high trade-in value. It’s also recyclable, helping you meet your company’s sustainability needs. We’ve delivered more than three million pallets to date, so you know our pallets are field tested and have satisfied many companies. Our pallets offer up to 2,800 pounds of rackable capability and 5,000 pounds of dynamic lard, and up to 30,000 pounds of static load. Every one of our recycled plastic pallets is saving 50 pounds or more of post-industrial plastic or discarded wood from being dumped into landfills. On top of that, it’s lighter and it’s actually safer fro your workers – the smooth edges without nails and splinters keeping your workers from getting hurt on the job.
Plastic Pallets Used
Buying plastic pallets used from Greystone Logistics can be a shrewd business move. Our skids are durable and long-lasting, with life spans as much as fifty times longer than wood, which makes buying plastic pallets used a safe bet if you’re looking to cut your investment in shipping products. Contact in-factory sales team member Marilyn Crawford or Warren Kruger with our sales team at Greystone in Tulsa to learn more about our options for buying plastic pallets used. Whether it’s used or new, the plastic option is the better option for shipping and warehousing needs. We’ve found plastic pallets have a lower cost per-trip, with no maintenance or repair to make on them. The advantages of plastic also include sanitary reasons – they are non-porous and non-permeable. They aren’t susceptible to bug or biological infestation, as is the case for wood products. They are lighter than wood and have a reliably consistent size for a dependable performance.

