Romarco Minerals Inc. Mill arrives. Aticle January
Post# of 29
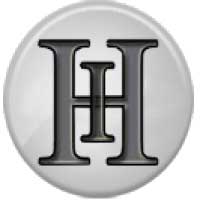
Romarco Minerals Inc. Mill arrives. Aticle January 27,2013 Lancaster News.
A long slow trek
Milling equipment takes 10 days to arrive at Haile Gold Mine
By Jesef Williams
Sunday, January 27, 2013 at 6:00 am (Updated: January 27, 6:00 am)
KERSHAW – Two expensive pieces of processing equipment were given parade-like treatment while on a recent trek from the coast to Lancaster County.
Aaron Morrison
Trucks carrying a semi-autogenous grinding mill, front, and a steel ball mill, both used to grind gold-laden rocks, make their way slowly down S.C. 265 on their way to Haile Gold Mine on Jan. 17. The trucks averaged 10 mph on their trip here from the port at Georgetown.
Buy this photo
As Romarco Minerals – parent company of Haile Gold Mine Inc. – awaits a final permit to build a gold mine near the town of Kershaw, the company is importing the machinery needed to run the gold-processing operation.
Two main cogs in that system are a SAG (semi-autogenous grinding) mill and a ball mill. When gold-laden ore is taken from the earth, pieces that are 6 inches or smaller are eventually fed into the SAG mill, said Mike Gleason, project construction manager at Haile Gold Mine.
That steel mill – 22 feet in diameter and 17 feet long – rotates to break the ore down into smaller rocks, measuring less than half an inch in diameter.
Gleason said those pieces are then placed in the steel ball mill, which is 15 feet in diameter and 30 feet long. That mill contains 3-inch balls that grind the ore into ever smaller pieces that resemble grains of sugar.
“The gold itself is microscopic in size,” Gleason said. “You can’t see it.”
Making it here
That’s a quick explanation of the mills’ functions, but getting that equipment to Kershaw is a story in itself.
Romarco Minerals ordered the mills in July 2011 from Polysius, a Germany-based company that has an office in Atlanta.
The mills cost about $8 million total, Gleason said.
Because of available resources and specialties, the SAG mill was made in Germany and the ball mill was made in India.
The mills were shipped to Georgetown, where they were taken from ships and loaded onto trailers for ground transport to Haile Gold Mine.
Guy M. Turner Inc. was the trucking company charged with the task of transporting the mills, which weigh thousands of pounds apiece.
Larry Bigger, a project manager with Guy M. Turner, said the two trucks – each pulling a mill – left Georgetown on
Jan. 7. Except for bypassing Lake City and Hartsville, the drivers traveled on rural secondary roads.
“Everything else was just out in the country,” Bigger said.
And slow travel was the name of the game. Not only are the mills valuable and heavy, they are also tall. Because of that, power lines had to be lowered or raised throughout the trip. Special permits were needed to do that.
Bigger said the height of the mills made the trek a unique and challenging experience.
“It was a challenge for the power companies. It was a very slow process,” he said.
“If we averaged 10 mph, we were doing good,” he said.
The mills arrived at Haile Gold Mine on Jan. 17 after being delayed about three days.
A waiting game
Now at Haile Gold Mine, the mills sit on a storage pad, where they’ll remain until the company gets the go-ahead to start mine construction.
Once operating, the mills will run 24 hours a day and will only stop for periodic maintenance, Gleason said.
On Thursday, David Thomas, general manager of Haile Gold Mine, was in Charleston meeting with the U.S. Army Corps of Engineers, which has to grant the final permit in order to build the mine and processing plant.
Haile Gold Mine officials hope to receive that permit this year.
“We’re still in that (discussion stage) right now,” Gleason said. “Hoping to get something definitive before too long.”
Contact reporter Jesef Williams
at (803) 283-1152y Jesef Williams
Sunday, January 27, 2013 at 6:00 am (Updated: January 27, 6:00 am)
http://www.thelancasternews.com/content/long-slow-trek

