$COTE $24,000,000 USD PURCHASE ORDER and some Info
Post# of 107707
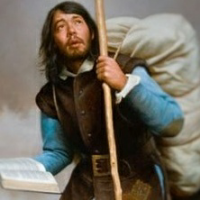
Thursday - April 4, 2019
COATES MANUFACTURING LTD., A WHOLLY OWNED SUBSIDIARY OF COATES INTERNATIONAL, LTD., RECEIVED A $24,000,000 USD PURCHASE ORDER ON APRIL 3, 2019, FOR 12 - 2 M.W. CSRV® ELECTRIC POWER GENERATORS
Wall Township, NJ – (Globe Newswire – April 04, 2018) For Immediate Release: Coates International, Ltd. (OTC PINK: COTE) (the “Company”) Coates Manufacturing Ltd., a wholly owned subsidiary of Coates International, Ltd., received a purchase order from an American alternator manufacturer for $24,000,000 USD for 12 - 2 M.W. multi-fuel CSRV® electric power generators.
▪ Company President and CEO, Mr. George J. Coates, comments: “This is a great start for this year. However, the company has already received many orders worth millions of USD.”
▪ Update: The Company management has decided not to extend its existing facilities and is selling its vacant parcel of land and is considering the purchase of a 102,000 sq. ft. manufacturing plant with expansion to another 145,000 sq. ft. The company is planning for the possibility of this to take place this year.
http://www.coatesengine.com/
Wednesday - April 3, 2019
COATES INTERNATIONAL, LTD. COMPLETES THE R&D ON ITS HYDROGEN H2 PROJECT. THE COATES CSRV ENGINES CAN NOW OPERATE ON GASEOUS HYDROGEN (H2) AND LIQUID HYDROGEN – PATENT PROTECTION WILL BE APPLIED FOR BEFORE THE TECHNOLOGY IS DIVULGED TO OUR INTERESTED CUSTOMERS
Wall Township, NJ – (Globe Newswire – April 03, 2018) For Immediate Release: Coates International, Ltd. (OTC PINK: COTE) (the “Company”) Management is pleased with the progress of its Hydrogen H2 technology. Company President and CEO, Mr. George J. Coates, comments: “This new breakthrough technology is a great asset to our company as the Coates CSRV® engines are believed to be the only power units in the world that can operate safely on Gaseous Hydrogen H2. The engines can also operate on liquid Hydrogen. Gaseous Hydrogen H2 is extremely volatile and static electricity from a woolen sweater or from someone’s hair could cause an explosion. Here at the Coates companies, we have solved these problems with our new Hydrogen technology.”
Introducing the CSRV Engine
The Coates Spherical Rotary Valve Engine is the most advanced in the world, with the most positive valving system ever built. The breathing capabilities of the system are almost double that of a poppet valve. For instance: a static test of a five-litre poppet valve engine on an airflow machine produced a reading of 133 cubic feet per minute (CFM) with valve fully opened. The five-litre Coates Spherical Rotary Valve Engine on the same machine, however, produced a reading of 319 CFMs fully opened; a colossal advantage in airflow comparison. A five-litre poppet vavle engine tested on a dynomometer under the same loads and conditions at 5500 produced 480 BHP and 454 foot pounds of torque. The maximum RPMs on the poppet valve engine were 5700 RPMs; the Spherical Rotary Valve Engine in comparison reached 14,850 RPM's, The Coates Spherical Rotary Valve comprises two spherical rotary valves assembled on two separate shafts - one for inlet and one for exhaust. They rotate on ceramic carbon bearing with no oil lubrication, the spheres do not make contact with any part of the housing. The seals are a floating type and are also made of a ceramic material. They have two piston rings and are floating in a small cylinder-type chamber, they are activated by the compression and the combustion strokes of the engine which allows 100 percent sealing effectiveness, when compressed.
Because the valves rotate away from the combustion chamber and are vented and charged on the opposite side of each sphere, this creates a lower combustion chamber temperature, allowing for higher compression ratios to be used thus creating an extremely efficient engine. Some of the Coates Spherical Rotary Combustion Engines are at 12 to 1, 13 to 1, 14 to 1 and 15 to 1 compression ratios depending on the application.
Their advanced engine The Coates Spherical Rotary Valve (CSRV) System: http://www.coatesengine.com/csrv-system.html
CSRV System Advantages
The Coates Spherical Rotary Valve System (CSRV) replaces the traditional Poppet Valves and all their associated parts, springs, guides, seats, retainers, cotters, pushrods, cam followers, camshaft, camshaft bearings, and many more parts including the oil.
Animation: CSRV vs Poppet Valve
The CSRV System is comprised of only two moving shafts and does not utilize oil pressure fed bearings, or oil spray; in fact, no engine oil is present in the head of the CSRV Engine. This means the engine oil does not see the hottest parts of the engine, which was the exhaust Poppet Valves. These extremely hot components usually are engine oil spray cooled. This heat would breakdown the atomic structure of the engine oil, thus lowering the oil viscosity, therefore, oil changes are recommended every 3,000 to 5,000 miles. On the other hand, with the CSRV incorporated in the engine design, oil change intervals are extended to approximately 50,000 miles or more.
The constant rotation of the CSRV, rotate away from the extreme heat of the combustion chamber, eliminating the possibility of hot spots in the combustion chamber; thus allowing for higher compression chamber ratios to be incorporated in the design of a combustion engine. This results in a higher thermal efficient engine and a more complete combustion that will utilize all of the energy contained in the fuel; also reducing harmful emissions.
High Compression Ratios
In the 1950 and 1960s combustion engines utilized compression ratios of 12 to 1. and higher, producing higher horsepower (H.P.), more torque (TQ) and a higher (thermal efficient engine) Engine efficiency was at approximately 35%. Governments around the world found that tetraethyl lead was the lead component in the gasoline at that time.
The findings were that this lead component in the fuel was extremely hazardous to human health and the world’s environment; it was then removed from the fuel. This caused the high compression automobile engines to develop hot spots in the combustion chamber and the hot spot was found to be the exhaust poppet valve. It was getting red hot, causing pre-ignition and damage to the engines. The only remedy for this was to lower the compression ratio of all engines; this resulted in a lowering of thermal efficiency from an engine having 35% efficiency to 22 to 24% efficiency. This included the less dense fuel with the lead removed.
This means for every dollar worth of fuel you put into your vehicle, you only get 22 to 24 cents of drivability, and the other 76 to 78 cents are lost through heat friction and pumping losses. We extract out of the earth approximately 86,000,000 barrels of oil daily, 62,000,000 barrels of this oil is lost just keeping our engines running. The other 24,000,000 barrels make possible our actual driving motion, and at the same time, creating insurmountable amounts of other harmful pollutions to be pumped into our atmosphere.
These are the reasons that compelled founder, George Coates to develop the CSRV Combustion Engine. The CSRV Engine utilizes much higher compression ratios, and has no hot spots and has a much greater volumetric efficiency; creating a higher thermal efficient combustion engine in the 35 – 40%, and possibly higher. With the ability to utilize alternative fuels, these possibilities open up new opportunities to reduce the world’s consumption of oil-fossil fuels, and reduce the production of harmful emissions that are pumped out into our atmosphere every day, and if implemented will reduce the United States’ dependency on imported foreign oil.
Rethinking the Internal Combustion Engine
The Coates Spherical Rotary Valve Engine is the most advanced in the world. A conventional piston engine ignites the fuel and air mixture in the combustion cycle and evacuates the gas by-products in the exhaust cycle. These cycles occur thousands of times per minute per cylinder. Through the rotation of the camshaft, a spring-loaded poppet valve opens to enable the fuel and air mixture to enter the firing chamber during the induction stroke. The camshaft then closes the intake valve during the compression and combustion stroke of the cylinder and opens a second spring-loaded valve to vent the cylinder after ignition. These gases then enter the exhaust manifold.
The parts required for this conventional spring-loaded valve assembly include items such as springs, cotters, guides, rockers, shafts and the valves themselves. The valve operates in a vertical position in the cylinder head such that a downward movement opens the valve and allows the introduction or evacuation of gas from the chamber.
The weakest link in the conventional engine has been the limited effectiveness of the poppet valve. The Coates engine replaces the poppet valve with a spherical rotary valve, thereby creating more efficient and powerful combustion and compression stokes.
The spherical rotary valve system is made up of spheres rotating on a shaft sandwiched between a split head. These spheres are either chain or belt driven via the crankshaft, much like an overhead camshaft. Each sphere rotates against a matching seal between it and the piston, one for intake and one for exhaust. The spheres have cavities and ports machined into them for the induction of fuel and air on the intake stroke, and the evacuation of fired gases on the exhaust stroke. This design performs exactly the same function as poppet valves, but the design eliminates the poppet valves, valve springs, guides, camshaft, pushrods, rocker arms and other smaller parts. The Coates engine operates with over 100 fewer parts than convention engines.
In addition, the spherical rotary valve combustion engine utilizes a proprietary seal at the intake and exhaust ports of the cylinder to prevent pressure leakage. This two-piece seal contacts the peripheral surface of the rotary valve and utilizes the compression and expansion of the fuel and air mixture to create a gas-tight seal with the valves. The lubrication of the rotary valve assembly is accomplished by bronze shaft bearings.
CSRV Advantages
The spherical rotary valve combustion engine possesses several significant advantages over the conventional poppet valve assembly. The benefits include the following:
Lower Emissions: Conventional engines run hot due to their inability to disperse heat from the firing chamber. The resulting high temperatures break down the oil used to lubricate the valves and produce oxides of nitrogen as well as the usual hydrocarbons. In addition, oil entering the combustion chamber through the intake valve is continually redirected back into the induction system due to pressure provided by the exhaust valve. This process compounds the problem of oil burning in a conventional engine. The Coates engine avoids the problem of oil burning by requiring no oil lubricants for the valves. Moreover, the rotation of the spherical valve heads reduces engine temperature by constantly changing the surface exposed to combustion heat. By eliminating the use of oil in valve lubrication and lowering operating temperature, the Coates engine emits significantly lower levels of pollutants than a conventional engine.
Reduced Fuel Requirements - Conventional engines lose power through friction and pumping. The spherical rotary valve assembly virtually eliminates engine friction and pumping losses. As a result of this operating efficiency, engines incorporating the spherical rotary valve design offer higher fuel economy than do conventional engines.
Reduced Lubrication Requirements - The use of seals and shaft bearing make oil lubrication of the valve heads unnecessary and lower the overall oil requirements of the Coates engine in comparison to a conventional engine. Without the component wear that characterizes typical poppet valve systems, engines using the spherical rotary valve design also produce fewer metallic particulates. As a result of these factors, the spherical rotary valve engine can realize longer maintenance intervals than conventional engines.
Increased Engine Power - The comparative efficiencies of the spherical rotary valve combustion engine have enabled engine speeds of 14,850 RPMs. In addition, the spherical rotary valve design can accommodate markedly higher compression ratios than conventional engines. The rotary design provides these exceptionally higher compression ratios with no detectable detonation when utilizing fuels of lower octane ratings. These factors, coupled with the ability of the rotary valve head to deliver more fuel to the combustion chamber than the poppet valve, makes the Coates design especially well suited for more powerful engines.
Reduced Engine Noise and Vibration - The spherical rotary valve combustion engine virtually eliminates mechanical clatter, one of the sources of engine noise. Mechanical clatter is a by-product of the wearing of components, inadequate lubrication, and components working themselves out of adjustment. The operation of CIL's prototype engines involves a rotary movement of the valve with uniform acceleration and deceleration of the components. Without the specific stresses and vibrations inherent in a poppet valve assembly, the spherical rotary valve combustion engine runs more quietly than conventional engines.
Alternative Fuel Adaptability - Unlike engines of conventional design, the spherical rotary valve assembly can be fit to almost any internal combustion engine from the single cylinder to the largest marine diesel. In addition, the spherical rotary valve system causes the engine to run far cooler than conventional designs thereby enabling it to utilize lower octane fuels.
Conventional poppet valves run hot due to their inability to disperse heat away from the combustion chamber. Hot exhaust valves in the conventional valve train system create "hot spots" which are the primary cause of pre-ignotion unless lead additives are present. Lead-free gasoline requires the use of long-stroke, relatively low compression engines in order to function properly without fuel additives.
High compression ratios can be utilized incorporating the Coates more efficient and powerful short-stroke design, while maintaining the desirable characteristics of optimum performance using lead-free gasoline. The design also allows the use of alternate fuels such as methanol and an alcohol mixture. The capability of variable valve timing is a design characteristic that lends itself to alternate fuel compatibility.
Reduced Manufacturing Costs - Utilizing standard production techniques while remaining within acceptable engineering standards and tolerances relating to current production line technology, the design can be manufactured at a substantial savings due to the following factors: (a) Reduction in the number of engine components(the number of components required in the manufacture of the design is approximately 29 vs. 155+ for conventional valve train designs); and (b) All components of the design can be die cast or stamped out resulting in a dramatic reduction of assembly time over conventional engine designs and once assembled, requires no further adjustments.
Comparative Analysis
Emissions tests conducted by an independent EPA-Compliant laboratory in USA have confirmed the superiority of Coates International CSRV engines in producing significantly lower pollutant. The following chart presents the emission results as reported by an independent laboratory which tested two vehicles, one running with stock engine and the second with stock engine retrofitted with Coates CSRV system.
Both vehicles were tested in steady state with the following parameters:
No EGR system
Warm up run on Dynamometer: 30 minutes
Engine temperature: 180 degrees F
Inertia Load: 2,000 pounds
Road horsepower: 13
Two catalytic converters installed
http://www.coatesengine.com/csrv-advantages.html
Contact Information:
Coates International, Ltd.
Phone: 732-449-7717
Fax: 732-449-0764
www.coatesengine.com
www.mostadvancedengine.com

