This is a blockbuster gamechanger in nanotech. We
Post# of 22467
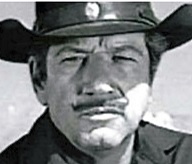
Therefore, the PR says high quantum efficiency (brightness), narrow FWHM (color purity), - and both those characteristics require high uniformity - the QD all being the same size. That is a major differentiator with other manufacturing systems.
There is a new term being used, "High Purity" which denotes to me that very little if any post production processing (PPP) is necessary for these PQD. PPP entails centrifuging the QD after their synthesis to get out all the low and high weight and deformed quantum dots in the the batch to produce their "champion" QD with great specs. Costly in time and manpower. So high purity, to me, means the QD are ready or nearly ready to ship when they come out of the continuous flow process and after testing.
These PQD produce "industry best" results that "set a new standard". If an OEM is making 4K or especially the new 8K Super High Resolution displays they need the best QD at the lowest cost. Continuous flow process does both.
Perovskite Solar! Prof. Michael Gratzel switched from DSSC to being a major proponent of PQD a few years ago and has co-authored advanced papers on PQDSC like "Air Processed Inkjet Infiltrated Carbon Based Printed Perovskite Solar Cells with High Stability and Reproducibility". Solterra is planned as an inkjet printing roll-to-roll production for high volume. I would be severely underestimating the cost difference between PQDSC and Silicon Panels if I said it was 5 times less costly, especially made in India. At 5 time less, we would see record breaking sales, at 10 times less we are getting to "save the world" pricing. PQDSC can be produced at a fraction of the cost of current tech.

