Canadian Metals Inc. announces filing of the Amend
Post# of 301275
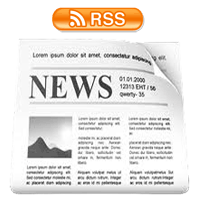
MONTREAL, July 11, 2018 (GLOBE NEWSWIRE) -- Canadian Metals Inc. (The “Corporation”) (CSE:CME) announces filing of an amended Technical Report for the Pre-feasibility Study (“PFS”) of its Langis project titled “Amended NI 43-101 Technical Report on Pre-Feasibility Study for Langis Project”.
The Amended Technical Report is to address concerns, requests for modifications and requests for clarifications expressed by the Autorité des Marchés Financiers (“AMF”) in two (2) observation letters issued on June 12th and June 20th, about the technical report dated June 1st, 2018 in relation to the National Instrument 43-101 on mining projects. The Amended Technical Report addresses clarifications and modifications of chapters 2, 3, 6, 13, 17, 22 and 25:
- Move information from section 3 to section 2
- Reliability of existing metallurgical testing to convert Langis siltstone into FerroSilicon75
- The representativity of samples tested (Geologically & Metallurgically)
- Revision and additional support on the FeSi75 selling price assumption used
- Removal of incorrect cautionary comment in the economic analysis
- More details on the technical path the material from Langis will transit to Baie-Comeau
- The reason why a QP in the report did not carry site visit at Baie-Comeau
- Complement the risk assessment
- Present a budget with physical amount of tests for the next step of testing required
The amended technical report has addressed the above items. The 2 main aspects of changes in the study are commodity price use in the study and support information allowing the Langis sandstone material to be usable in production of Ferro Silicon.
1- After reassessment and analysis of the long term selling price, the 1819 US/t was in the high range while a more reasonable selling price more conservative is in the 1493$US/t, this price is now used for the economic analysis. The impact is a lower NPV and IRR, in the context of Ferrosilicon production it still present robust economic values and is still positive and deserve to move forward 2- Additional information on analytical testing, third party testing and suitability to produce Ferro silicon has been demonstrated, not only at existing quarry face but from core material at different position in the deposit. It is also important to mention that testing and production of Ferro silicon was conducted and achieved with existing producers at small scale and results and coordinates may not be disclosed due to confidentiality agreements. The QP have had access to these information and confirm the positive results to support the PFS.
The Prefeasibility Study was prepared by CIMA+ in partnership with several Quebec-based engineering firms: GoldMinds Geoservices for Mineral Resources & Reserve Estimate and Mining; WSP for Environmental Impact and Strategy; Michel Bilodeau for Financial Analysis and CIMA+ for Metallurgical Process, CAPEX, OPEX and Engineering.
Table 1 Original PFS vs Amended PFS Highlights:
Prefeasibility Study Results Highlights | Units | Original PFS | Amended PFS | |||
Pre-Tax | After-Tax | Pre-Tax | After-Tax | |||
NPV @ 8% Discount Rate | CAD | 525 | 388 | 241 | 171 | |
Internal Rate of Return (IRR) | % | 24,5 | 22,0 | 16,0 | 14,4 | |
Payback Period | Year | 3,8 | 4 | 5,9 | 6,1 | |
Average annual SiO2 raw production to the quarry (Mineralization) | tonne | 225 000 | no change | |||
Quarry Process Recovery of raw material | % | 75 | no change | |||
Average annual SiO2 production of lump for the smelter | tonne | 129 692 | no change | |||
Average production of excess SiO 2 for local market | tonne | 40 000 | no change | |||
Average production of FeSi75 (1.8 SiO 2 per Tonne of FeSI75) | tonne | 72 051 | no change | |||
Average production of Microsilica/Slag | tonne | 13 320/5 180 | no change | |||
Weighted average selling FeSi75 price | USD | 1 819 | 1 493 | |||
Weighted average selling Microsilica/Slag (in USD $250/$100) | CAD | 333/133 | no change | |||
Weighted average selling of SiO2 for local sale (in USD $24.38) | CAD | 32.50 | no change | |||
Direct CAPEX | CAD | 220.3 M | no change | |||
Indirect CAPEX | CAD | 90.8M | no change | |||
Contingency (15 %) | CAD | 32.8M | no change | |||
Owner costs | CAD | 8.0M | no change | |||
Total CAPEX | CAD | 311.1M | no change | |||
Projected Construction Period | Month | 18 to 24 | no change |
Tonne =1000kg=2205 lb Exchange rate $0.75 USD = $ 1.00 CAD use throughout this press release.
Cautionary Note: Prefeasibility Study information is not a guarantee of future performance. Furthermore, such forward-looking information involves a variety of know and unknown risks, uncertainties and other factors, which may cause the actual plans, intentions, activities, results, performances or achievements of CME to be materially different from any plans define in the Prefeasibility study. The purpose of this PFS is to inform the reader of the economic potential of the mineral property within a degree of accuracy of ± 25 %.
Amended PFS compared with the results of the Pre-Economic Assessment (PEA) the following can be highlighted:
- From PEA a NPV@8% of 273.1 CAD and an IRR of 18.0% after-tax
- From PFS a NPV@8% of 171 CAD and an IRR of 14.4% after-tax.
- The metallurgical plan has been relocated from Matane to Baie-Comeau with a significant optimization around the plant layout and production of the FeSi75.
- We have increased the percentage of Budget Quotes and Estimated items to secure the CAPEX (According to AACE Estimate Standards class 4 @ ±25 (range -30% to 40%) engineering completions 5 to 12%)
- We have increased the OPEX budget quotes from several items for the raw materials, including Coal, Woodchips and quartz (transport and quarry operation)
- Construction activities were not factorized but estimated based on an equipment list, preliminary MTO and Technology suppliers background
- We have optimised the furnace size based on the operators, experts and technology suppliers advises. The aim was to have a stable operation with less innovation to commission.
- The Price market study came from a list of experts such as Roskill, CRU, MetalBulletin, Platts, CIBC, BMO, Argus ferro-Alloys, Ryan`s note (Peter Ryan).
- For the PFS formal quotes for mining, crushing and screening costs at the quarry compares to estimation in the PEA.
The new location of the metallurgical plant in Baie-Comeau has advantages such as significant HQ electrical grid location (capacity and availability), access and retention of skilled labour. Furthermore, Baie-Comeau has the benefits of an industrial platform to support operation and maintenance contracting strategy an easy access to service-industrial providers.
Mineral Resources (no changes from Original to Amended PFS)
- High-grade silica sandstone deposit at surface open-pit constrained resources at a cut-off grade of 97% SiO2;
- Major increase in resource estimates 217% for Langis compared to the October 2016 resources.
- The block model is a 5m x 5m x 3m 3-dimensional block model with each block containing major elements SiO2 %, Fe2O3 %, Al2O3%, MgO %, MnO %, K2O %, CaO %, Na2O %, TiO2 % grades, density and resource classification (Measured, Indicated, and Inferred).
Table 2 Mineral Resources
Category | Total Silica (mt) | SiO 2 Grade (%) | |
Measured | 3.9 | 99.01% | |
Indicated | 3.7 | 98.97% | |
Total (M+I) | 7.6 | 98.96% | |
Inferred | 14.0 | 98.97% |
Cautionary Note: Mineral Resources are not Mineral Reserves and have no demonstrated economic viability. The estimate of Mineral Resources may be materially affected by mining, processing, metallurgical, infrastructure, economic, marketing, legal, environmental, social and governmental factors.
Mining (no changes from Original to Amended PFS)
The mining method selected for the Project is a conventional open pit, truck and shovel, drill and blast operation.
Based on client request, contract operation was used as a basis for the PFS Study, and GMG was provided with four budgetary pricing from different regional contractors after running RFP for the turnkey operation of the quarry based on the required tonnage and product specifications
The contractor will operate a seasonal quarry operation with 5 days per week, 11 hours per day, 5 months of the year during the warmer seasons to reduce the social impact of the project .
Mineral Reserves (no changes from Original to Amended PFS)
The open pit design includes 6.3 Mt of Probable & Proven Mineral Reserves at a grade of 99% SiO 2 taken from the 7.6Mt of M+I resources. In order to access these reserves, 0.8 Mt of overburden and 2.6 Mt of waste rock will need to be removed. This results in a stripping ratio (waste to ore) of 0.41.
The following tables present the parameters used for the pit optimization, while the second shows the parameters used for the reserve estimation.
Table 3 Pit Optimisation Parameters
Item | Value | Units |
Mining Cost—Ore and Waste | 5.00 | $/t (mined) |
Processing Cost | 10.00 | $/t |
Quarry Recovery | 95.00 | % |
%SiO 2 Cut-Off Grade | 97.00 | % |
Overall Pit Slope | 45 | degree |
Material Density Selling Price Assumption | 2.33 44 | t/m 3 $/t |
Limiting Resource Classification | Measured & Indicated | |
Pit Design Method | Lerchs-Grossmann |
Table 4 Parameters Used for the Reserve Estimation
Activity | Rate | Units |
Contractor Costs | ||
Drill and Blast | CAD | 4.36 |
Ore/Waste Excavation and Crushing (primary and secondary) | CAD | 10.78 |
Loading and Handling (stockpiling at quarry site) | CAD | 3.90 |
Total from Rock face to Stockpile ready for shipment (ore) | CAD | 19.04 |
General & Administrative Costs | ||
CME supervision staff Production (QA/QC) | CAD | 0.59 |
CME supervision staff Environment (regulation & monitoring) | CAD | 0.59 |
HQ power supply (estimated) | CAD | 0.25 |
Environmental monitoring (analytical costs) | CAD | 0.05 |
Quebec government MERN | CAD | 0.40 |
MRC for road use | CAD | 0.58 |
Insurance | CAD | 0.04 |
Social St-Vianney | CAD | 0.25 |
Total G&A Costs | CAD | 2.75 |
Ore Total (contractor + G&A Costs) | CAD | 21.79 |
Waste (contractor mining costs) | CAD | 8.26 |
Next table presents the open pit reserves for the Langis deposit for a LOM of 28 years.
Table 5 Open‑Pit Mineral Reserves
Category | Total Silica (mt) | SiO 2 Grade (%) | |
Proven | 3.5 | 99% | |
Probable | 2.8 | 99% | |
Total (Proven + Probable) | 6.3 | 99% |
Table 6 Grades of major elements in the Mineral Reserves
Total Proven & Probable (mT) | SiO2 (%) | CaO (%) | Cr2O3 (%) | K2O (%) | MgO (%) | MnO (%) | Na2O (%) | P2O5 (%) | SO3 (%) | SrO (%) | Al2O3 (%) | Fe2O3 (%) | TiO2 (%) |
6.30 | 99.0 | 0.06 | 0.01 | 0.09 | 0.12 | 0.01 | 0.02 | 0.01 | 0.02 | 0.01 | 0.46 | 0.13 | 0.05 |
The above table indicate the expected average grade of the major elements. All within the CME expected values for the Langis deposit.
Metallurgical Testing
CIMA+ have not performed additional metallurgical testwork for the purposes of the PFS. The main reasons are:
- FeSi production under metallurgical processes is a very standardized process using Submerged Arc Furnace (SAF) utilizing a very standard process flow sheet and various suppliers of such technology following the same route of processing including standard raw materials requirements for the SAF operation
- From a geological standpoint, the Langis Sandstone deposit is relatively homogenous and has not been affected by metamorphism. The nature of the beds are well preserved and the stratigraphy is well preserved in the deposit. There are minor vertical faults causing limited vertical displacement of the sedimentary package and grade (chemistry) and core texture are not affected other than being less massive (lower RQD). The authors are in the opinion that samples taken at the existing quarry face represent the general behaviour of the Langis deposit. Moreover, GoldMinds took wrap density measurements on core samples and found a lower density that what was used earlier. The Langis Sandstone has a porosity and this characteristic is probably one of its component which makes the material behave well in the thermal shock test,
- The QP’s are aware that metallurgical testing has been performed on core samples from various part of the deposit at a different world renowned producer’s laboratory. As per confidentiality agreement, CME is not allowed to disclose the name and, respectively - the results to the public. These tests were performed on samples from the 2013 drilling program, the results proved Langis silica can be used for generation of ferrosilicon with actual piece of ferrosilicon produced as a result of these tests from the Langis sandstone, which is currently stored at CME headquarters. The QP have had access to this information and confirm the material and test are reliable for the PFS level of design. More importantly the tests were performed on samples representing different parts of the deposit not limited only to the quarry sector, which proves similarity of the Langis sandstone across the ore body.
As part of the final PFS recommendations, CIMA+ stresses on the fact that more extensive metallurgical testing should be undertaken under the FS stage including:
- Development of a strategy and recipe for a detailed metallurgical test program to optimize process performance and confirm the metallurgical design including mineralogy, characterization of heating properties of quartz, thermal stability by shock heating, melting properties by Sessile drop test, phase transformation during heat treatment, and simulation of Si production process in medium scale. In addition, more detailed pilot‑scale ferrosilicon production should executed
- Investigation of the option to produce Metallurgical Silicon (mgSi) as final product as a pose to FeSi75 or be capable to produce both products.
The detailed metallurgical test program recipe will be developed by CIMA+ prior to the FS stage and will result in testing sufficient to FS and EPCM of the proposed facility.
Processing and Smelting (no changes from Original to Amended PFS)
The Langis silica deposit will be quarried and recovered for use as a feedstock into a downstream ferrosilicon smelter in Baie‑Comeau to produce metallurgical products such as FeSi75 (ferrosilicon 75 standard).
Process steps at the quarry site will consist of blasting, crushing, and sizing the silica before transportation to the smelter. Silica that is too fine for use in the smelter can be marketed to local industries, while lumps will be used directly in the smelter.
The smelter at Baie‑Comeau will produce FeSi75 by a pyrometallurgical process that combines silica from the Langis quarry with a coal for fixed carbon source, iron ore, and wood chips in an SAF in which these raw materials are smelted into ferrosilicon. Molten ferrosilicon is tapped from the furnace into ladles, and then a multiple layer casting method will be used. The solidifying product is crushed and classified into saleable FeSi75 products after sufficient cooling.
The metallurgical facility will produce on an annual basis 72,051 tonnes of FeSi75 as well as the following process by-products: 13,583 tonnes of microsilica and 5,282 tonnes of slag. The raw materials request to produce the FeSi75 are:
- Silica (Quartzite) – Langis Silica (129 692 tonnes)
- Reducing Agent – Coal (83 839 tonnes)
- Iron ore (25 218 tonnes)
- Wood Chips (72 051 tonnes)
- Electrode Paste – Søderberg Paste (3 603 tonnes)
Capital and Operating Costs Summary (no changes from Original to Amended PFS)
The capital cost requirements for the project are presented in Table 7 below. The capital cost assumes a fully contracted quarry and beneficiation operations from local operators. The metallurgical plant relocates to Baie‑Comeau and the cost structure and indirect costs were optimized to reflect the local conditions. The capital cost estimate, summarized below, covers the development of the mine, ore processing facilities, and infrastructure required for Canadian Metals project. It is based on the application of standard costing methods of achieving a PFS, which provides an accuracy of ± 25 % and follows AACE Class 4 Guidelines. The operating cost covers mining, transportation, processing, tailings and water management, general and administration fees, as well as infrastructure and services.
Table 7 Capital Costs Summary
CAPEX Item | Cost in CAD | |
Direct Costs | ||
Quarry Development/Pre-Stripping | $ 250,000 | |
Quarry Infrastructure | $ 821,000 | |
Metallurgical Plant Buildings | $ 50,4M | |
Metallurgical Plant Process | $ 135,9M | |
Metallurgical Plant Infrastructure | $ 32,8M | |
TOTAL DIRECT | $ 220,2M | |
Indirect Costs | ||
Owner Costs | $ 8,0M | |
Freight | $ 5,8M | |
Heavy Lift (250‑T Crane) | $ 620,000 | |
Construction Indirect Costs | $ 11,5M | |
Supplier Engineering | $ 10,0M | |
EPCM | $ 21,9M | |
Contingency | $ 32,8M | |
TOTAL INDIRECT | $ 90,8M | |
TOTAL DIRECT & INDIRECT | $ 311,1M |
The estimate has followed the AACE Standards for a Prefeasibility level class 4 ±25% (range -30% to 40%)
The operating costs for the project were estimated annually. A summary of these operating costs is presented in the following table.
Table 8 Operating Costs Summary
Operating Costs Breakdown (28 years project life) | Annual Average | Average Costs | |
(CAD/t FeSi75) | |||
Energy | 26,226,570 | 364.00 | |
Raw Materials and supplies | 31,582,115 | 438.33 | |
Transport SiO 2 (Langis to Metallurgical Plant) | 9,078,426 | 126.00 | |
G&A all area | 7,285,797 | 101.12 | |
Quarry Operation | 5,034,203 | 69.87 | |
Labour metallurgical Plant | 11,744,313 | 163.00 | |
TOTAL | 90,952,284 | 1,262.00 | |
Projected Revenues From Sales | 175,099,774 | 2,430.00 |
Overall, operating cost covers quarry operations, transportation, metallurgical processing, energy and raw materials, G&A fees, infrastructure, and services.
The project will see the creation of approximately 135 direct jobs in the metallurgical plant located in Baie-Comeau. Although Canadian Metals has already received some contractor budget quotes for quarry operation and SiO2 transportation, CME will manage an official Request for Proposal (RFP) at the next phase. Canadian Metals wants to allow contractors to submit their bids without constraints on staff numbers and the strategy to reach operational objectives.
Project Economics Summary
Metallurgical ex-plant selling prices of US$1,493 per tonne or US$0.93/lb (US$1,819 per tonne or US$1.10/lb for the OriginalPFS) for ferrosilicon, US$250 per tonne for silica fume and US$ 100 for the slag were used for the financial analysis as well as CAD/US$ exchange rate of 0.75.
Table 9 Cash Flow and Project Financials Summary (Original vs Amended PFS)
Description | Units | Original PFS | Amended PFS |
Parameter | Parameter | ||
Pre-Tax | |||
Payback Period | Years | 3,8 | 5,9 |
Cash Flow | CAD | 2,085,7M | 1, 252, 1M |
NPV @ 6% | CAD | 727, 2M | 369, 0M |
NPV @ 8% | CAD | 525, 5M | 240, 5M |
NPV @ 10% | CAD | 381, 5M | 149, 7M |
Internal Rate of Return | % | 24,5% | 16.0% |
After Tax | |||
Payback Period | Years | 4,0 | 6,1 |
Cash Flow | CAD | 1, 573, 3M | 960, 6M |
NPV @ 6% | CAD | 543, 6M | 273, 3M |
NPV @ 8% | CAD | 388, 8M | 171, 3M |
NPV @ 10% | CAD | 277, 5M | 98, 6M |
Internal Rate of Return | % | 22,0% | 14,4% |
Sensitivity Analysis
The following sensitivity graphs for the Pre-Tax IRR and NPV@8% indicate that increase/decrease in CAPEX, OPEX and the FX rate will have a positive/negative effect respectively; but the greatest sensitivity is on the Selling price, then FX rate followed by OPEX and CAPEX.
To view Figure 1 and 2 Sensitivity Analysis (IRR and NPV @ 8%) – Original PFS, please visit the following link: http://www.globenewswire.com/NewsRoom/Attachm...14ac722cce
To view Figure 3 and 4 Sensitivity Analysis (IRR and NPV @ 8%) – Amended PFS, please visit the following link: http://www.globenewswire.com/NewsRoom/Attachm...4eefacbf7f
Project Summary
The prefeasibility study work plan is based on the recently completed updated resource model for the Langis project that shows a major increase over the previous resources statement results. The metallurgical plant planned location has been moved from Matane to Baie-Comeau in Quebec. The design includes a quarry, situated at Saint‑Vianney, QC, with a simple beneficiation plant on site from where the Langis quartz will be transported approximately 105 km (including 60 km across seaway) to a metallurgical plant (smelter) in Baie‑Comeau, QC, to produce ferrosilicon75 (FeSi75) as the final product as well as other saleable process by-products. Other raw materials for the process include coal for reducing agent, iron, wood chips, and Söderberg electrode paste. The smelter is designed to operate with two (2) 35‑MW Submerged Arc Furnaces (SAF), followed by standard tapping, cooling, and crushing facility for the final FeSi75 product. At the smelter, there will be an off-gas treatment system to capture microsilica (or silica fumes) as a by-product for sale and keep environmentally friendly metallurgical operations.
The quarry operation assumes 28 years Life-of-Mine (LOM) with an average annual capacity of approximately 225,000 tonnes of quartz, of which 75% of recovery will be sized at the beneficiation plant at Langis to feed the Baie-Comeau smelter requirements with approximately 129,692 tonnes and an average of 38,883 tonnes for the local market. Over this quantity, the quarry will produce fines amount and a low-grade volume for an average of 55 468 tonnes per year, which it will also be sold to the local market.
The distance from St-Vianney to Matane and Baie-Comeau Port to Metallurgical plant are about 40 km/15 km on a B-trains (60 tonnes of capacity) used for transportation via existing public roads. Distance from Matane to Baie-Comeau is around 65 km, a barge system or the existing facilities will be used for transportation across St. Lawrence River from month May to February. The global strategy is to contract on all included engagement for the transportation. The strategy is to handle the traffic between Langis to Matane for ten months and to stop during the thaw period around two months. The trucking activities will be restricted from 7 am to 6 pm to minimize noise and ground vibrations to neighbours and the local communities.
Land Acquisition for the Smelter in Baie-Comeau
Dated July 11th 2017 Canadian Metals apply to get the land (581,000 square meter) from the Quebec Ministère de l’Énergie et des Ressources Naturelle (MERN) for the future smelter in Baie-Comeau, the analyze by the MERN of their request is almost completed. In parallel Canadian Metals work with Baie-Comeau Authorities regards the official transfer of this land in the Jean Noel Tessier Industrial area, for them this mean an easier access to municipal infrastructure, It is expected this been achieved in a few months, as the discussions involves well among Canadian Metals, MERN and Baie-Comeau.
Certificate of Authorisation (CA) for Baie-Comeau site
Dated March 19th 2018, Canadian Metals officially issued Project Notice to Québec Ministere du Developpement Durable, de l'Environnement et de la lutte contre les changements climatiques (MDDELCC), data collection on site was performed during the summer 2017 by WSP and will be completed in 2018. Recently, Canadian Metals has mandated WSP to perform the environmental impact study to acquire the CA for the Baie-Comeau site. Canadian Metals expect this study being completed by the second quarter of 2019
Permit for the Langis quarry operation
Langis project, a high-purity silica deposit located in St-Vianney, Québec with fully permitted with the certificate of authorization (CA) for the Langis silica project from the Quebec Ministere du Developpement Durable, de l'Environnement et de la lutte contre les changements climatiques (MDDELCC). The certificate of authorization represents the principal regulatory approval required to start the operation of the Langis quarry and has been issued by the Quebec regulators.
Canadian Metals owns it operating lease (BEX) from the Quebec Ministry of Energy and Natural Resources. Canadian Metals will actualize all authorizations and permits to operate the Langis pit at 225 000 tonnes per year.
Community Relations
Since 2016, Canadian Metals has held several meetings with people or groups from the town of St-Vianney and Baie-Comeau and nearby communities. During these presentations and consultations, important ties of trust have been forged between the population and the company. An accompanying committee, composed of citizens and regional experts, is working with Canadian Metals technical team to ensure that the project grows while respecting the host environment and, above all, contributes to the regional dynamism.
Risk and Opportunities
During the PFS processing, some risks have been considered by the operator and investor perspective. The following risk list presents some of the major flaws and opportunities that we have considered during the prefeasibility study:
- Product sale price and market : we have managed several information from many market input. For example, we have considered the many outlooks advises from the experts and bankers;
- Exchange Rate: It can improve or reduce the project economy. We have considered the bank forecasts considering the project strategies.
- Raw Material Transport: the costs of transport (quartz and coal) might have a major impact on the Opex. We have considered several bids or quotations to minimize this impact on the project operation costs.su
- Technology: we based our design to avoid commissioning innovation technology and first design. The design is based on the Submerged Arc Furnace (SAF) a well-know technology.
In addition, as part of the amended report work the risks associated to the metallurgical testing were incorporated into the risk analysis as well.
Recommendations:
For the next stage of project development, namely the Feasibility Study, CIMA+ recommends several very important steps and tasks regarding the metallurgical testing and design in order to firm up and optimize the process design to ensure optimal metallurgical plant performance that will produce the optimal final products and thus maximize the project economics. Those steps and measures are:
+ Develop a strategy and recipe for a detailed metallurgical test program to optimize process performance and confirm the metallurgical design. Such test program should include mineralogy, characterization of heating properties of quartz, and simulation of Si-production process in medium scale. In addition, a Pilot scale ferrosilicon production will be undertaken for clearly defining the process flow sheet.
The proposed budget to execute the above listed activities is expected to be in the range of $500k-$750k and the work should be included into the feasibility study.
Quality Assurance and Quality Control (QA/QC) Preparation for the mineral resources
The samples were analyzed by at the independent laboratory at SGS Lakefield in Ontario. The half core sample are dried, crushed to have 75% passing 2mm and afterward riffle split to have 250grams which is pulverized with tungsten carbide puck pulverizer to have a pulp 85% passing 75 microns. Afterward an XRF borate fusion with 12-element analysis was done. The independent standards are in line with expected results as well as laboratory QA/QC and allow public disclosure of the results.
Qualified Persons
The technical information derived from the PFS and presented in this news release was prepared and approved by Georgi Doundarov, P. Eng., PMP, CCP, of CIMA+, Nathalie Fortin P.Eng. of WSP Canada Inc, Claude Duplessis and Claude Bisaillon, P. Eng., of Goldminds Geoservices all independent Qualified Persons as defined by National Instrument 43-101.
Baie Comeau Site Visit
CIMA+ didn’t perform a Qualified Person site visit to the Baie Comeau site where the Metallurgical plant is proposed to be located. CIMA+ decided not to perform the site visit during the Prefeasibility study level and postpone it for the next stage of the Langis project development – Feasibility study. The reasons behind that decision were:
- WSP Environmental team performed such visit in order to complete the section 20 of the Prefeasibility report, namely “Environmental Studies, Permitting, and Social or Community Impact”
- CIMA+ acquired all the necessary topographic maps, required to evaluate the site and perform the engineering design for the Prefeasibility study
- CIMA+ had series of discussions with the Baie Comeau town authorities (engineers, etc.)
- CIMA+ obtained the required documents from the Government of Quebec on the new road 349 including geotechnical and land surveys
- CIMA+ received various aerial photos from the Baie Comeau site visit, conducted by Hubert Vallee (at the time CEO of Canadian Metals).
- CIMA+ had performed interviews with various local contractors and operators such as the operators for the port yard and the lay down pad located in a close proximity to the proposed Metallurgical plant location
- Finally, CIMA+ already had recent Baie Comeau information, obtained for the purposes of previous projects the company was involved in the area.
CIMA+ plans to execute the Baie Comeau site visit prior to the next stage of the Langis project development – the Feasibility study.
About Canadian Metals
Canadian Metals is a diversified resource company focused on creating shareholder value through the development of large-scale industrial mineral portfolios in specific commodities and jurisdictions that will fuel the new energy economy. The Company is uniquely positioned to pursue this strategy and controls significant interest in Silicon and base metal assets throughout North America.
Our main activities are directed towards the development of Langis project, a high-purity silica deposit located in the province of Quebec with fully permitted with the BEX and the certificate of authorization from the MDDELCC. The Company is rapidly positioning itself as a supplier of high purity silica and silicon alloy in North America. Silicon based materials can be formulated to provide a broad range of products from more durable, faster building materials with smarter electronic devices, solar panels and more efficient wind turbines. We expect to become a global supplier for a number of industries and applications but without limitation: glass, ceramics, lighting, oil and gas, paint, plastic and rubber. We also want to become an integrated supplier to metallurgical industries including foundries, and participate in a wide range of civil, industrial, environmental and related applications. These target markets are an integral part of the lives of millions of people every day.
For more information, please contact:
Sean Tufford Vice President, Corporate Development Email: Sean@canadianmetalsinc.com Phone: (902) 818 -8807
René Boisvert President, Email: rboisvert@canadianmetalsinc.com
Stéphane Leblanc Chief Executive Officer Email: sleblanc@canadianmetalsinc.com
Website: www.canadianmetalsinc.com
Cautionary Statements Regarding Forward-Looking Information
Certain statements included herein may constitute “forward-looking statements”. All statements included in this press release that address future events, conditions or results, including in connection with the pre-feasibility study, its financing, job creation, the investments to complete the project and the potential performance, production and environmental footprint of the ferrosilicon plant, are forward-looking statements. These forward-looking statements can be identified by the use of words such as “may”, “must”, “plan”, “believe”, “expect”, “estimate”, “think”, “continue”, “should”, “will”, “could”, “intend”, “anticipate” or “future” or the negative forms thereof or similar variations. These forward-looking statements are based on certain assumptions and analyses made by management in light of their experiences and their perception of historical trends, current conditions and expected future developments, as well as other factors they believe are appropriate in the circumstances. These statements are subject to risks, uncertainties and assumptions, including those mentioned in the Corporation’s continuous disclosure documents, which can be found under its profile on SEDAR ( www.sedar.com ). Many of such risks and uncertainties are outside the control of the Corporation and could cause actual results to differ materially from those expressed or implied by such forward-looking statements. In making such forward-looking statements, management has relied upon a number of material factors and assumptions, on the basis of currently available information, for which there is no insurance that such information will prove accurate. All forward-looking statements are expressly qualified in their entirety by the cautionary statements set forth above. The Corporation is under no obligation, and expressly disclaims any intention or obligation, to update or revise any forward-looking statements, whether as a result of new information, future events or otherwise, except as expressly required by applicable law.
Neither the CSE nor its Regulation Services Provider accepts responsibility for the adequacy or accuracy of this release.

