Global Geoscience Announces Successful Completion
Post# of 301275
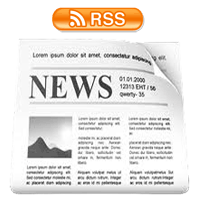
Highlights
- Vat leaching process and an on-site acid plant selected - yielding more operational and economic benefits for emerging Rhyolite Ridge lithium-boron mine in Nevada.
- Rhyolite Ridge is the global front-runner to become the first mine to recover lithium using the proven and well understood vat leaching method.
- Sulphuric acid cost estimated at US$20 to $30/tonne after credit from steam and power generation – an important economic driver for the lithium-boron project.
- Pre-Feasibility Study (“ PFS”) on track for release in Q3 2018.
SYDNEY, Australia, May 23, 2018 (GLOBE NEWSWIRE) -- Australian-based lithium-boron mine developer Global Geoscience Limited ( “ Global” or the “ Company” ) (ASX:GSC) today announced the results of the first phase of the Pre-Feasibility Study (“PFS”) for the 100%-owned Rhyolite Ridge Lithium-Boron Project in Nevada, USA.
The critical trade-off studies demonstrate a clear path forward for the project, and highlight the potential for Rhyolite Ridge to be a major, low-cost producer of lithium and boron in an environmentally sustainable manner that uses self-generated, zero-carbon power and minimises both water useage and surface disturbance.
Global Geoscience’s Managing Director, Bernard Rowe commented:
“Sulphuric acid is an important economic driver for the project, and the combination of vat leaching together with an on-site acid plant will substantially lower the cost of acid, thus reducing the overall operating costs.
“An acid plant will produce large amounts of steam that can be used for heating in the processing plant and for generation of electricity via steam-driven turbines with excess power available for selling into the grid.
“Steam produced from the acid plant negates the high input costs normally associated with mechanical evaporation.
“Vat leaching, coupled with mechanical evaporation, produces the most concentrated pregnant leach solution with consistent composition, thus simplifying downstream processing.
“With the critical trade-off analysis completed, the PFS is on track to be completed in mid-2018 with the outcomes scheduled to be released in Q3 2018.”
Summary of Trade-Off Studies
Four critical trade-off studies were completed as Phase 1 of the PFS:
- Vat Leaching has been selected as the leaching method providing:
- A more controlled leach environment with higher concentrations of lithium and boron into the pregnant leach solution (“PLS”)
- Less evaporation of the PLS is required because of the higher initial concentrations, resulting in fewer mechanical evaporators and lower power consumption
- Materially lower capital and operating costs compared to alternative leaching techniques.
- An on-site acid plant has been selected as the source of sulphuric acid providing:
- Substantially lower sulphuric acid cost estimated at $20-30/tonne including credit for steam and power generation used in the operation
- Acid plant produces more than enough steam and power for the entire operation
- Excess electricity (circa 20-30MW) available to be sold into the grid providing an opportunity for substantial further credits toward operating costs
- Substantially lower overall processing costs
- Fast payback on higher up-front capital to build a sulphuric acid plant.
- Mechanical evaporators have been selected over solar evaporation ponds providing:
- A highly controlled and efficient process environment resulting in simplified downstream processing
- Smaller footprint and less environmental impact
- Substantially lower water consumption as water is captured and recycled
- Lower operating costs as heat/energy is provided by sulphuric acid plant.
- Dry stack of vat leach rejects has been selected as the disposal method
- Lower capital cost, smaller footprint and less environmental impact than alternatives
- No tailings dam required.
Sulphuric acid is an important operating cost for the project and two of the trade-off studies examined ways to minimise acid cost and consumption. By allowing greater control over the leach process, vat leaching results in lower acid consumption compared to heap leaching.
An on-site acid plant to make sulphuric acid from sulphur has a major positive impact on the cost of acid. The cost of sulphuric acid has been estimated at $20-30/tonne after taking into account the benefit of the acid plant producing the steam and electricity required for the entire operation.
The substantial decrease in acid cost and consumption are expected to result in lower operating costs than previously envisaged. An acid plant will mean higher up-front capital expenditure, however, the plant payback period is expected to be short.
Leach Method
Metallurgical testwork has indicated that high recoveries of lithium and boron can readily be achieved at Rhyolite Ridge via leaching with sulphuric acid by either:
- leaching milled mineralisation in an agitated tank leach; or
- leaching crushed mineralisation in a heap or vat leach.
All three options are technically viable, each with competing strengths and weaknesses. The trade-off study evaluated the relative merits of each technology with the aim of selecting a single leach technology to advance into the PFS.
The table below ranks the leach technologies in order of preference for various key criteria and clearly shows that vat leaching is the preferred technology for Rhyolite Ridge .
Criteria | Tank | Vat | Heap |
Boric Acid Concentration | 2 | 1 | 3 |
Pay Metal Recovery | 3 | 1 | 2 |
Impurity Elements* | 1 | 3* | 2 |
Acid Consumption | 1 | 2 | 3 |
Other Reagents | 3 | 1 | 1 |
Steam Consumption | 2 | 1 | 3 |
Power Consumption | 3 | 1 | 2 |
Excess Acid Plant Power | 3 | 1 | 2 |
Water Consumption | 3 | 1 | 2 |
Waste Streams | 3 | 2 | 1 |
Land Disturbance | 3 | 1 | 2 |
Operating Risk | 2 | 1 | 3 |
Operating Cost | 3 | 1 | 2 |
Capital Cost | 3 | 1 | 2 |
Total (lowest is best option) | 35 | 18 | 30 |
Note: Ranking of 1 is most favorable and 3 is least favorable. * vat leach testwork completed subsequent to the trade-off study has shown lower levels of impurity elements compared to heap leach.
The most significant factor for vat leach over heap leach is the high concentration of boric acid in the PLS that can be achieved with vat leaching at an elevated temperature. This results in significant operating and capital cost savings in the evaporation/crystallisation of boric acid. The higher concentration in the vat leach PLS means less evaporation and subsequently, lower power consumption.
Vat leach offers the most process control of leach kinetics - allowing a reliable, repeatable and robust leach process.
Acid Source
Metallurgical testwork has shown that acid leaching can achieve recoveries of greater than 95% to PLS for lithium and boron from the Rhyolite Ridge mineralisation with acid consumption in the range of 350 to 450 kg/tonne of feed. This makes sulphuric acid an important economic driver for the project. The acid source trade-off evaluated the relative merits between purchasing sulphuric acid versus generating sulphuric acid on-site through a dedicated acid plant fed with purchased prilled sulphur.
Several key factors were examined in the acid source trade-off study:
- Freight – The freight cost for sulphur prill is based on trucking from San Francisco or Los Angeles. The freight cost for sulphuric acid is based on railing and then trucking. This resulted in the transportation cost for sulphuric acid being approximately 60% higher per unit than prilled sulphur.
- Price – The price of prilled sulphur is approximately 50% less than sulphuric acid.
- Electrical Power Cost – an acid plant is estimated to supply all the electrical power required for the operation as well as generating an estimated additional 20-30MW per annum which would be available to be sold into the grid.
- Process Plant Steam Supply - an acid plant will be able to supply all the steam required for the processing plant, thus building an additional boiler facility would not be necessary.
Producing sulphuric acid on site has many advantages:
- Low cost sulphuric acid leading to substantially lower operating costs
- Estimated at $20-30 per tonne of acid including credits from steam and power generation
- Provides sufficient steam and power for the entire operation plus surplus power that would be available to be sold into the grid as an additional credit
- Fast payback period on the higher up-front capital costs.
The overall cost of running the acid plant including maintenance, labour, sulphur and other consumables is estimated to total $55-$65 per tonne of acid. In order to compare with the cost of purchasing sulphuric acid, the estimated costs of producing the steam and purchasing the electricity required on site were deducted. The net cost is estimated at $20-30 per tonne of acid. These figures do not include any potential revenue from selling excess electricity generated of 20-30MW per annum.
The trade-off study concluded that constructing an acid plant is the strongly preferred option.
Evaporation Method
A trade-off study was undertaken to compare solar evaporation ponds with mechanical evaporation.
The climate at Rhyolite Ridge is favourable for the use of evaporation ponds and generally would have a lower energy cost per tonne than a mechanical evaporation and crystallisation circuit. However, the power and steam generated by a sulphuric acid plant negates the high input costs and improves the economics of the mechanical process at Rhyolite Ridge.
The table below ranks the evaporation methods in order of preference for various key criteria and clearly shows that mechanical evaporation is the preferred technology .
Criteria | Pond | Mechanical |
Land Disturbance | 2 | 1 |
Operating Risk | 2 | 1 |
Start-up Time | 2 | 1 |
Speed to Market | 2 | 1 |
Storage Facilities | 2 | 1 |
Consistent feed to downstream process | 2 | 1 |
Water Consumption | 2 | 1 |
Operating Risk | 2 | 1 |
Operating Cost | 2 | 1 |
Capital Cost | 1 | 2 |
Total (lowest is best option) | 19 | 11 |
Note: Ranking of 1 is most favorable and 2 is least favorable.
Several key differentiators include:
- Much smaller footprint for mechanical evaporation.
- Much lower risk of significant environmental incidents with mechanical evaporation.
- Significant advantages to using the continuous process that the mechanical evaporation and crystallisation provides. It is relatively easy to operate and produces a consistent boric acid slurry and lithium brine in terms of concentration and particle size. This greatly simplifies the downstream process which provides cost savings.
- For the pond option, it is expected that it would take a minimum of 19 months to have the brine in the entire pond system at normal concentrations. Also prior to the first product harvest, a significant amount of the initial boric acid production is used to create a bed at the bottom of the pond. This is required to act as a buffer between the harvesting equipment and the pond base.
- For the pond option, the water is evaporated and lost to the atmosphere. In contrast, essentially all the water evaporated in the mechanical process is condensed and available for reuse. In addition, the mechanical process recovers heat and in turn reclaims large quantities of water for reuse in the process.
Waste Disposal
The waste disposal trade-off study developed scoping-level designs and capital costs for constructing disposal areas of leach rejects or tailings for the three acid leaching technologies: vat leach, heap leach and agitated tank leach.
These cost and design considerations were used in the assessment of the preferred leach technology. The lowest cost option was determined to be dry stack deposition of vat leach rejects.
Vat leaching typically results in relatively coarse rejects which would be transported to and disposed in a designated area.
Dry stack deposition offers benefits through reduction of water consumption and production of an unsaturated “filter cake” tailing medium. A dry stack facility has the advantage of requiring a smaller facility footprint as they can be stored at a higher density and can be built into a mound that projects above topography. In addition, dry stack facilities do not require a conventional dam or a retention structure. A starter embankment is commonly constructed initially to provide startup capacity as well as to provide containment for contact water retention when required.
The capital cost of a waste storage facility for vat leaching was determined to be 28% less than heap leaching and 37% less than tank leaching. Vat leaching also requires the smallest footprint.
Background on Vat Leaching
Vat leaching is a batch leaching system conducted in large rectangular vessels typically made of lined concrete. Crushed ore is loaded into the vat, flooded with various leach solutions, before being drained, washed and unloaded to complete the leach cycle. A vat leach system consists of a number of vats, typically in the order of 8-15 vats, with solutions operating in carousel fashion, counter current to the ore. Vat leaching is typically well suited to fast leaching ores where a high concentration PLS is required.
A typical vat leaching setup is shown below:
http://www.globenewswire.com/NewsRoom/Attachm...12433e411f
Vat leaching is similar to heap leaching but differs in the following key aspects:
- Due to limitations in vat sizing, there are multiple vats with each vat serving a dual purpose of ore leaching and solution collection. This allows for a countercurrent leach arrangement with as many stages as there are vats. This is in contrast to heap leaching which is rarely more than 2 or 3 stages with intermediate solution storage ponds required between stages.
- Vats are flooded and contained which permits solution irrigation rates one to two orders of magnitude larger than heap leaching. Further, a flooded vat offers superior solution distribution and contact when compared to the downward percolation of heap leaching.
- Vat leaching offers a greater ability to control the leach temperature to elevated levels while minimising and controlling heat losses.
- Vat solution flow can be upflow avoiding conflicting crossflow of leach solution and evolved carbon dioxide from carbonate dissolution.
In the proposed vat leach at Rhyolite Ridge, the crushed lithium-boron mineralisation and acid leach solution will be contained in a lined and insulated concrete vessels, which limits heat losses and permits operation at an elevated temperature to increase boric acid solubility. To maintain leach temperatures, solution heating will be required and can take advantage of the acid plant as source of low-cost steam.
Contacts at Global Geoscience
Bernard Rowe | James D. Calaway | Roger Howe |
Managing Director | Chairman | Investor Relations |
T: +61 419 447 280 | T: +1 713 818 1457 | T: +61 405 419 139 |
E: browe@globalgeo.com.au | E: jcalaway@calawayinterests.com | E: rhowe@globalgeo.com.au |
About Global Geoscience
Global Geoscience Limited (ASX:GSC) is an Australian-based lithium-boron mine developer focused on its 100%-owned Rhyolite Ridge Lithium-Boron Project in Nevada, USA. Rhyolite Ridge is a large, shallow lithium-boron deposit located close to existing infrastructure. It is a unique sedimentary deposit that has many advantages over the brine and pegmatite deposits that currently provide the world’s lithium. The Rhyolite Ridge Pre- Feasibility Study is in progress.
Global’s Rhyolite Ridge is the only lithium deposit in the world that has been demonstrated to be amenable to simple acid leach processing, reinforcing it as an economically viable alternative to spodumene and brine deposits as a major, low-cost and long-term source of lithium.
Global Geoscience is aiming to capitalise on the growing global demand for lithium and boron. Lithium has a wide variety of applications, including pharmaceuticals, lubricants and its main growth market, batteries. Boron is used in glass and ceramics, semiconductors and agriculture. Global Geoscience aims to develop the Rhyolite Ridge Lithium-Boron Project into a strategic, long-life, low-cost supplier of lithium carbonate and boric acid. To learn more please visit: www.globalgeo.com.au .
Competent Persons Statement
The information in this report that relates to Exploration Results is based on information compiled by Bernard Rowe, a Competent Person who is a Member of the Australian Institute of Geoscientists. Bernard Rowe is a shareholder, employee and Managing Director of Global Geoscience Ltd. Mr Rowe has sufficient experience that is relevant to the style of mineralisation and type of deposit under consideration and to the activity being undertaken to qualify as a Competent Person as defined in the 2012 Edition of the ‘Australasian Code for Reporting of Exploration Results, Mineral Resources and Ore Reserves’. Bernard Rowe consents to the inclusion in the report of the matters based on his information in the form and context in which it appears.

