Don't PTOIs processors handle polystyrene? I wonde
Post# of 43066
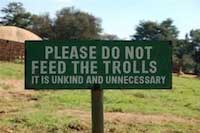
Recycler Agilyx shifts to focus solely on polystyrene
Agilyx Corp. expects to back in production in just a matter of months, this time producing styrene monomer at a reconstituted recycling facility in Oregon.
After years of mixed plastics-to-oil research and development, the Tigard, Ore.-based company has altered focus with an eye on only converting used polystyrene into styrene monomer.
Another $5 million in new funding is committed and work is now taking place to revamp Agilyx equipment to handle the new feedstock, CEO Ross Patten said.
The Agilyx facility, near Portland, went dormant when oil prices fell and it became uneconomical to operate mixed plastic-to-oil pyrolysis.
But this time around, with money from Saphron Hill Ventures and billionaire Richard Branson’s Virgin Group, two previous investors, Agilyx is changing focus to styrene.
“We are now reconstructing the plant here at Tigard to be a styrene conversion facility where we will be able to take polystyrene foam, and we can convert that back into a monomer and sell that to refiners who then sell it to converters,” Patten said. “We close the loop.”
Agilyx already is stockpiling used polystyrene in anticipation of restarting operations in June or July, the CEO said.
Some will pay the company to take their PS while others will drop it off for free, Patten explained. A third group, which can provide a very clean feedstock, will even get paid for the material.
Agilyx expects to use about half of the equipment previously employed at the mixed plastic facility. “What we call the front end pretty much stays the same, and the back end gets modified to the new conversion technology — the heat exchangers and chillers and stuff like that,” he said. “The front end consists of initially shredding to get a consistent size and there’s a melt phase where it gets melted and water is driven off and turned into a paste like material,” he said.
Agilyx also will be able to operate the existing system’s reactor, which uses pyrolysis to convert the plastic into gas through the use of high temperatures.
After the reactor, where the new construction is taking place, the gases are chilled and turned back into a liquid. “The first phase of that is to take out the old system. We’re in the process of doing that now,” he said.
“I am very committed to the technology and the mission of the technology. I really got into this because of the environmental impact,” Patten said. “We just can’t keep producing plastics that end up blowing around or putting it into the landfill when there’s a higher value.”
http://www.plasticsnews.com/article/20170124/...olystyrene

