Courtesy of LV RDPD from a U.S. EPA document: htt
Post# of 43066
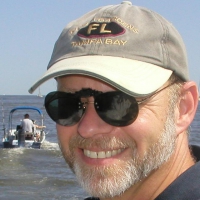
Courtesy of LV RDPD from a U.S. EPA document:
http://nepis.epa.gov/Exe/ZyNET.exe/P100FBUS.t...ZyEntry=27
2.1.4 JBI: Niagara Falls, New York
JBI uses a proprietary pyrolysis process, Plastic2Oil (P2O), to convert mixed, nonrecyclable plastic waste to fuel oil and naphtha. JBI receives feedstock from a variety of sources, including commercial and industrial partners, and is currently seeking a permit to use MSW-based feedstock. JBI has been operating at a commercial status in Niagara Falls, New York, since 2010 and anticipates one jointly-operated site in Canada and several in Florida. The P2O processor is highly automated and runs continuously, as long as feedstock is loaded into the hopper. Approximately 1,800 pounds of feedstock can be converted per hour. The process currently converts up to 20 tons of plastics per day. However, 30-ton-per-day units are in development. The footprint for the processing equipment is less than 1,000 square feet.
Feedstock is first shredded or pre-melted and conveyed to the reactor via a hopper and conveyor system. The reactor cracks the plastics into shorter hydrocarbons that are gaseous at the operating temperature of the reactor. After cracking, the heavy fraction gases are condensed and stored in fuel tanks and the light fraction gases are compressed and used to internally power the P2O process or are sold separately. Inputs include natural gas for start-up, proprietary catalysts, water and electricity. P2O is permitted to generate electricity onsite using process gases as fuel. Since the process can convert approximately 8 percent of the plastic feedstock into these light-fraction process gases, the grid electricity requirement averages around 67 KWh per ton of plastics processed.
According to data reported to RTI by JBI (RTI, 2012), for every ton of plastic processed, approximately 5 pounds of nonhazardous solids, 136 pounds of char (characterized by JBI as carbon black or pet coke), and spent catalysts are produced in addition to the naphtha, diesel, and light-fraction gases. Residues are removed automatically.
The Plastic2Oil process claims a recovery efficiency rate of approximately 92 percent (RTI, 2012). Each ton of plastic produces approximately 1,700 pounds of gasoline and diesel. Additional
byproducts include residuals, which have been found to have a heating value of 10,600 BTU, and syngas. These products and byproducts may then be blended with other fuels and additives, depending on the market and/or needs of the purchaser. JBI also relies on the off-gases generated internally, reducing the operating costs and offsetting electricity grid mix emissions.
According to the RTI report (2012), primary air emissions from the P2O process include particulate matter, carbon dioxide, nitrogen oxides, hydrocarbons, and VOCs. However, JBI claims it is not required to monitor emissions or install emissions control technologies. In terms of GHG emissions, converting 1 ton of plastic using the P2O process is claimed by JBI to yield approximately 0.29 pounds of carbon equivalent emissions. The vendor also reports 2.41 pounds of NOx emitted for every ton of waste plastics. JBI reports that the atmospheric emissions are less than those of a natural gas furnace. JBI claims water is used for gas cooling and wastewater from this step is reused, but no water effluent is generated.
The estimate for cost per design capacity is $587,000 for the entire machine. Operational costs to cold start and power the processing equipment average about $7 per hour. Plastics are generally provided to JBI at no cost.
In addition to receiving permits to begin commercial operations in New York, JBI recently announced a joint venture with OxyVinyl Canada to produce oil onsite using the waste plastics generated by OxyVinyl. JBI is currently focusing on creating additional partnerships with organizations that have existing permits and high-volume waste plastic streams to maximize consistent feedstock volume while minimizing the permitting processes.


Plastic2Oil, Inc. (PTOI) Stock Research Links
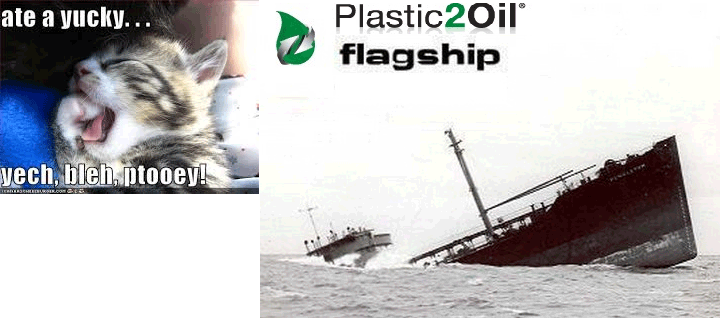