Contact printing The contact printing process f
Post# of 22465
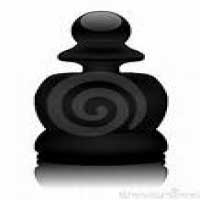
The contact printing process for forming QD thin films is a solvent-free[contradictory] method, which is simple and cost efficient with high throughput. During the process, the device structure is not exposed to solvents. Since charge transport layers in QD-LED structures are solvent-sensitive organic thin films, avoiding solvent during the process is a major benefit. This method can produce RGB patterned electroluminescent structures with 1000 ppi (pixels-per-inch) resolution.[16 ]
The overall process of contact printing:
Polydimethylsiloxane (PDMS) is molded using a silicon master.
Top side of resulting PDMS stamp is coated with a thin film of parylene-c, a chemical-vapor deposited (CVD) aromatic organic polymer.
Parylene-c coated stamp is inked via spin-casting of a solution of colloidal QDs suspended in an organic solvent.[contradictory]
After the solvent evaporates, the formed QD monolayer is transferred to the substrate by contact printing.
Contact printing allows fabrication of multi-color QD-LEDs. A QD-LED was fabricated with an emissive layer consisting of 25-µm wide stripes of red, green and blue QD monolayers. Contact printing methods also minimize the amount of QD required, reducing costs. The demonstrated color gamut from QD-LEDs exceeds the performance of both LCD and OLED display technologies.[16]
https://en.wikipedia.org/wiki/Quantum_dot_display
https://www.google.com/#q=new+quantum+dot+Par...icity+2016
....surface browse seems to indicate parylene layer has to do w/hole transport/block depending on materials used and effects on hardness wrt UV

