....excerpts from Quantum Dot Ink Formulation for
Post# of 22465
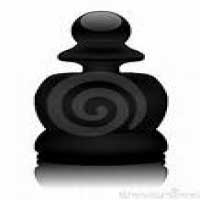
Inventors: Nathalie Gresty (Chester), Nigel Pickett (Manchester)
As-synthesized QDs are traditionally intolerant to high-temperature processing conditions, since increased temperatures can lead to thermal population of excited states by charge carriers, which then recombine non-radiatively. Processing at elevated temperatures is advantageous for display applications, thus methods to enhance the thermal stability of QDs have been developed to assist their processability.
Other approaches are centered on enhancing the inherent thermal stability of the QD by confining the excitons within the core, such that they become largely insensitive to environmental factors such as temperature and atmosphere. Htoon et al. reported the synthesis of “giant” CdSe/CdS QDs with optical characteristics that were largely insensitive to high temperature processing conditions [H. Htoon, A. V. Malko, D. Bussian, J. Vela, Y. Chen, J. A. Hollingsworth & V. I. Klimov, J. Am. Chem. Soc., 2008, 130, 5026]. In these so-called “giant” QDs a thick shell (ten or more monolayers) of a wider bandgap material is grown epitaxially on a standard, narrower bandgap QD core. To alleviate strain effects that are typically induced due to the lattice mismatch between the core and shell materials, the shell is typically composed of a compositionally graded alloy. Alloying further serves to randomise the energy levels between the core and shell, increasing the confinement of electron and hole wavefunctions within the middle layers of the nanoparticle.
The QD ink described herein is optimally formulated using core/shell (including multi-shell and/or compositionally graded alloy shell architectures) semiconductor nanoparticles.
QD microbeads exhibit superior robustness, and longer lifetimes than bare QDs, and are more stable to the mechanical and thermal processing protocols of the heat transfer process. By incorporating the QD material into polymer microbeads, the nanoparticles become more resistant to air, moisture and photo-oxidation, opening up the possibility for processing in air that would vastly reduce the manufacturing cost. The bead size can be tuned from 20 nm to 0.5 mm, enabling control over the ink viscosity without changing the inherent optical properties of the QDs. The viscosity dictates how the QD bead ink flows through a mesh, dries, and adheres to a substrate, so thinners are not required to alter the viscosity, reducing the cost of the ink formulation. By incorporating the QDs into microbeads, the detrimental effect of particle agglomeration on the optical performance of bare encapsulated QDs is eliminated
A preferred method is suspension polymerization, involving thermal curing of one or more polymerizable monomers from which the optically transparent medium is to be formed. Said polymerizable monomers may comprise methyl (meth)acrylate, ethylene glycol dimethacrylate and vinyl acetate. This combination of monomers has been shown to exhibit excellent compatibility with existing commercially available encapsulants (e.g. those used for LED manufacture) and has been used to fabricate a light emitting device exhibiting significantly improved performance compared to a device prepared using essentially prior art methodology. Other examples of polymerizable monomers are epoxy or polyepoxide monomers, which may be polymerized using any appropriate mechanism, such as curing with ultraviolet irradiation
By incorporating QDs into beads in the presence of materials that act as stability-enhancing additives, and optionally providing the beads with a protective surface coating, migration of deleterious species, such as moisture, oxygen and/or free radicals, is reduced if not entirely eliminated, with the result of enhancing the physical, chemical and/or photo-stability of the semiconductor nanoparticles.
Further stability to high temperature processing conditions can be achieved using an atomic layer deposition (ALD) process to shell the QD beads, as described in U.S. patent application Ser. No. 14/208,311, filed Mar. 13, 2014, the entire contents of which are incorporated herein by reference. The ALD process can be used to coat QD beads with a moisture barrier such as, but not restricted, to Al2O3. The process is intended to enhance the lifetime of the QD beads without negatively impacting on their optical properties
To formulate the ink, the QDs or QD beads are first dispersed in an appropriate solvent. The solvent boiling point should be below the thermal transfer temperature. Optimally, the boiling point should be <170° C., more preferably <150° C.
Typically, temperatures in the region of 160-220° C. are employed. In some embodiments, temperatures below 200° C. are employed to preserve the optical properties of the QDs. The heat and pressure are applied for typically 60-120 seconds.
http://patents.justia.com/patent/20150075397
http://patents.com/us-20150075397.html
.....just a fun read
QMC product: QDX tm 260 deg C.

