Mining Industry Profile: Iron 1-17 Subsequent fi
Post# of 8059
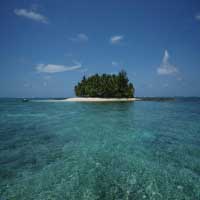
1-17
Subsequent fine grinding further reduces the ore particles to the consistency of fine powder (325 mesh,
0.0017 inches, 0.44 microns). .......
Magnetic Separation
Magnetic separation is most commonly used to separate natural magnetic iron ore (magnetite) from a
variety of less-magnetic or nonmagnetic material. Today, magnetic separation techniques are used to
beneficiate over 90 percent of all domestic iron ore (See Table 1-4) (Ryan 1991). Between 20 and 35
percent of all the iron units being beneficiated in the United States today are lost to tailings because
hematite is only weakly magnetic. According to the Bureau of Mines, techniques used-to-date to try to
recover the hematite have proven uneconomic.
Magnetic separation may be conducted in either a dry or wet environment, although wet systems are
more common. Magnetic separation operations can also be categorized as either low or high intensity.
Low intensity separators use magnetic fields between 1,000 and 3,000 gauss. Low intensity techniques
are normally used on magnetite ore as an inexpensive and effective separation method. This method is
used to capture only highly magnetic material, such as magnetite. High intensity separators employ
fields as strong as 20,000 gauss. This method is used to separate weakly magnetic iron minerals, such
as hematite, from nonmagnetic or less magnetic gangue material. Other factors important in
determining which type of magnetic separator system is used include particle size and the solids content
of the ore slurry feed (Weiss 1985; United States Steel 1973).
Typically, magnetic separation involves three stages of separation: cobbing, cleaning/roughing, and
finishing. Each stage may employ several drums in a series to increase separation efficiency. Each
successive stage works on finer particles as a result of the removal of oversized particles in earlier
separations. Cobbers work on larger particles (3/8 inch) and reject about 40 percent of the feed as tails.
Mining Industry Profile: Iron
1-18
Cleaners or scavengers work on particles in the range of 48 mesh and remove only 10 to 15 percent of
the feed as tails. Finally, finishers work on ore particles less than 100 mesh and remove the remaining
5 percent of gangue (because of the highly concentrated nature of the feed at this point) (Weiss 1985).

