Here is what I would like to see, an agreement bet
Post# of 43066
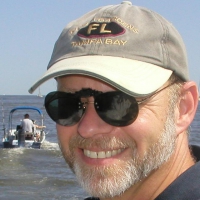
http://www.mitsubishielectric.com/company/env...eparation/
Separating Plastics at High Levels of Purity and High Recovery Rates
To make closed-loop recycling a reality, it is first necessary to separate out usable plastics from the used home appliances that have been collected. Mixed, shredded plastic used to be exceedingly difficult to separate, but Mitsubishi Electric has developed a proprietary method for separating plastics based on their respective characteristics. This method enables plastics to be separated at high levels of purity and high recovery rates.
http://actioninternationalinc.com/plastic_separation.htm
This technology can be easily used wherever plastics recycling is required. The process is clean and dry, and very low cost using less than 1 kilowatt of power for a one tonne/hour capacity separator.
Because of the low cost of the separation process and the compatibility with current recycling technologies, it is profitable to process even low cost polymers such as polypropylene (PP) and polyvinyl chloride(PVC).
http://www.vecoplanllc.com/products/separating-technologies
Vecoplan also offers total system controls integration. This allows aggregate material to flow from one processing station to another until it reaches its end point without the need for human monitoring of individual machine processing speeds. Wood, metals, plastics, paper, glass, dirt, rock, concrete – Vecoplan can automate the segregation of virtually all fractions within an aggregate through the proper use of the correct separation technology.
http://www.mixed-plastics-sorting.com/?n=56&lang=6
S+S offers a full range of equipment for contaminant separation – from basic sorting through to precision separation applications.
Our systems will sort mixed streams into single fractions, playing a pivotal role in ensuring that highly pure recycled material can be profitably reprocessed in the production cycle.
http://ecopreneurist.com/2011/10/24/mike-bidd...-industry/
Biddle has developed a patented 30-step plastics recycling system that includes magnetically extracting metals, shredding the plastics, sorting them by polymer type and producing graded pellets to be reused in industry – a process that takes less than a tenth of the energy required to make virgin plastic from crude oil. Today, the company he cofounded, MBA Polymers , has facilities in California, China, Austria and the UK can process over 300 million pounds (over 140,000 tons) of waste per year, selling the purified plastics back to some of the largest manufacturers in the world of IT, electronics, appliances, automobiles, office, home and garden products. Moreover, the process is very efficient, saving over 80% of the energy and between 1 and 3 tons of CO? for every ton of virgin plastics replaced.


Plastic2Oil, Inc. (PTOI) Stock Research Links
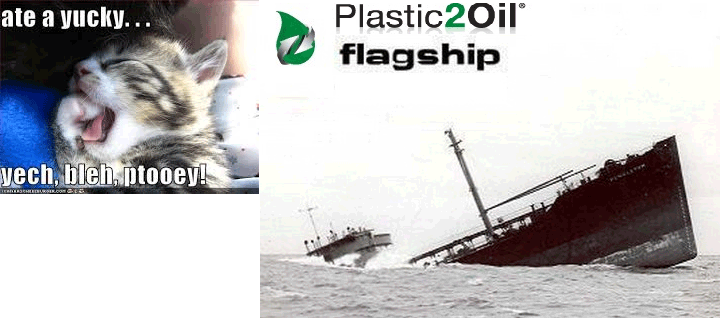