$MVTG patent chemistry!!!
Post# of 18862
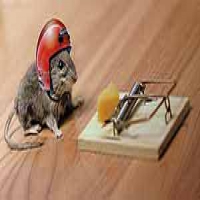
http://www.otcmarkets.com/edgar/GetFilingHtml...ID=9621266
For a full description of the ERC technology and associated IP, see the patent application WO/2007/041872, “Continuous Co-current Electrochemical Reduction of Carbon Dioxide”.
The ERC (“Electro-Reduction of Carbon Dioxide”) technology employs an electrochemical reactor to convert carbon dioxide (CO 2 ) into [b]formate ions (HCO 2 -[/b]), and subsequently a [b]formate salt[/b] (e.g. [b]NaHCO 2[/b] , [b]KHCO 2 [/b], or [b]NH 4 CO 2[/b] ) or [b]formic acid (H 2 CO 2 )[/b]. In general the process involves the mixing of a CO 2 -containing gas stream with an aqueous liquid electrolyte, their co-current two-phase flow through and over a porous three-dimensional (3D) cathode at which the reduction reaction takes place, and the separation of the product. The process also involves a complementary oxidation reaction at the counter electrode, or anode, and the corresponding electrolyte handling.
The ERC reactor is generally composed of a number of compartments, or cells, each of which contains two electrodes spaced apart and separated into two chambers by an ionically conductive but electronically insulating layer that prevents mixing of the fluids in each compartment. The negatively charged electrode (cathode) is in the form of a fluid permeable conductive mass, such as a bed of particles or a fixed porous matrix, which is composed of an electronically conductive material, the surface of which is a good electro-catalyst for the desired reaction. CO 2 -containing gas and an ionically conductive liquid (cathode electrolyte, or catholyte) flow co-currently into the cathode chamber via an inlet, through and over this cathode where the desired reduction reaction takes place, and out of the cathode chamber via an outlet. A complementary oxidation reaction occurs at the counter-electrode (positively-charged terminal or anode), where an ionically conductive liquid (anode electrolyte, or anolyte) flows over or through this electrode, which can be flat or 3D. The operating parameters of this reactor are selected such that advantageous mass transfer characteristics are obtained.
While there are a wide variety of setups, reactants, products, and operating parameters through which ERC can be used, an example is provided below based on one of these embodiments. This example represents a small range of the ways in which ERC can be implemented, but is nonetheless illustrative.
In this example [b]ERC is employed to convert CO 2 to sodium formate (NaHCO 2 ). An aqueous solution of a sodium salt such as sodium bicarbonate (NaHCO 3 ) would be used as the catholyte,[/b] generally in concentrations of greater than 1 M to provide sufficient ionic conductivity. Additives such as sodium chloride (NaCl) may be included to further promote conductivity. This catholyte is mixed with a CO 2 -containing gas stream, which, depending on its composition, may be pretreated to remove particulates or other impurities. The mixture flows co-currently in two-phase flow into the cathode chamber(s) and over and through the 3D cathode. Employing a 3D structure for the cathode greatly increases the surface area available for reaction and reduces CO 2 mass transfer constraint . An imposed potential difference between the two electrodes causes the following “primary” reaction to occur:
[b]It is important to note that the active species in this reaction is aqueous carbon dioxide [CO 2 (aq) ], as opposed to gaseous CO 2 or bicarbonate.[/b]
[b]This fact necessitates the presence of CO 2 -containing gas in the reactor, as the solubility of CO 2 in water is low. The presence of the gas provides the driving force for maintaining the concentration of CO 2 (aq) in the electrolyte[/b]. The gas/liquid holdup ratio in the reactor is an important operating parameter, and is optimized where enough gas is available to maintain CO 2 (aq) concentrations and enough liquid is available to provide sufficient conductivity.
CO 2 solubility increases with increasing CO 2 partial pressure and decreasing temperature, and as a result the reactor may be run at super-atmospheric pressure (or, in the case of an impure gas stream, enriching its CO 2 volume fraction) and at ambient temperatures.
The speciation between CO 2 (g) /CO 2 (aq) /HCO3-/CO 3 2-, and thus the pH upon which this speciation is dependent, is critical to the efficacy of the process. High pH values will result in much of the aqueous CO 2 being sequestered as carbonate, while low values will contribute to an undesirable side reaction that also occurs at the cathode:
Although Reaction 2 is thermodynamically favored over Reaction 1, the selection of an electro-catalyst with a high hydrogen overpotential (e.g. Pb, Sn, In, or Hg) for the cathode surface will promote Reaction 1 over Reaction 2. [b][color=red]Operation above pH 7 and below pH 10 is preferred, to suppress both Reaction 2 and the sequestration of CO 2 in carbonic species.[/color][/b]
The occurrence of Reaction 2 makes the direct formation of formic acid difficult, as this would require operation in acidic conditions. Other side reactions may occur to a small extent, such as the reduction of CO 2 to CO or hydrocarbons. The “current efficiency” is an important indicator of performance, and represents the fraction of the current that is consumed in the primary desired reaction (CO2 reduction to formate).
At the anode a complementary oxidation reaction occurs. The function of the anolyte is both to provide electrons for reduction and provide cations to balance the charge. In the instance of producing NaHCO 2 , the anolyte would thus need to contain sodium ions, and would likely be sodium hydroxide (NaOH) or a sodium salt such as NaCl. The corresponding oxidation reactions are:
[b]As a result of the oxidation, a co-product is formed.[/b] In the instances of hydroxide and chloride, [b]the co-product would be oxygen gas[/b] and chlorine gas, respectively.
Both catholyte and anolyte leave the reactor through their respective outlets and are directed to phase separators. The CO 2 -containing cathode gas is separated, any hydrogen present removed or recovered, and the remaining gas vented or recycled. Product-containing catholyte liquid may be recycled to the reactor to increase product concentrations, and may undergo further concentration stages. Byproduct gas from the anode is vented or recovered and the anolyte is recycled to the reactor.

