Development of Micro JP-8 Fuel Injection S
Post# of 183
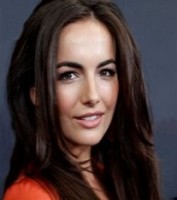
Development of Micro JP-8 Fuel Injection System for Small Unmanned Aerial Army SBIR 2014.1 - Topic A14-019 Opens: December 20, 2013 - Closes: January 22, 2014 A14-019 TITLE: Development of Micro JP-8 Fuel Injection System for Small Unmanned Aerial and Ground Engines
TECHNOLOGY AREAS: Air Platform
ACQUISITION PROGRAM: PEO Aviation
OBJECTIVE: To develop and demonstrate a €˜novel €™ direct fuel injection system for small unmanned compression-ignition heavy-fuel (primarily Jet Propellant-8) engines (3-70 horsepower)
DESCRIPTION: The Army is in need of efficient heavy-fuel small engines (3 to 70 horsepower) for unmanned aerial and ground systems. The success of these engines requires efficient and reliable micro direct fuel injection systems. Currently, there is no reliable direct fuel injection system for small engines due to various reasons. One of them is manufacturing capability of micro nozzles.
Use of direct fuel injection into a combustion chamber can achieve much higher engine efficiency than that of carburetor or port fuel injection. Direct fuel injection also provides flexibility to control combustion processes to improve engine performance and efficiency by using injection strategies such as multiple injections and rate shaping which shall be compared with the current Shadow Unmanned Aerial Vehicle (UAV) engine (i.e. a 38-horsepower rotary engine with aviation gasoline). Since much higher fuel injection pressure can be applied for direct fuel injection, engine power can be increased significantly higher than the old fuel injection systems. Direct fuel injection system has been predominantly developed for low- to heavy-duty engines. Therefore, while the demand for the small engines is increasing, there has been no reliable direct fuel injection system for small engines. Furthermore, in contrast to low- to heavy-duty engine classes for which significant amounts of research have been done by large companies, no noticeable research on small engines have been done until now. One of the main challenges in developing a direct fuel injection system for small engines is preparing combustible fuel-air mixture within the confined space of the small engine combustion chamber. The current off-the-shelf fuel injectors provide excessive liquid fuel penetration and high cycle-to-cycle variations in small fuel quantities. Smaller injector nozzle (< 75 micrometers) can achieve shorter penetration length; however, the current manufacturing capabilities such as electrical discharge machining (EDM) are limited for nozzle sizes smaller than 75 micrometers. The lower side of the nozzle sizes shall be as low as 40 micrometers, while the upper side being up to 150 micrometers. Therefore, the drilling method should be able to machine from 40 to 150 micrometers with the tolerances of less than +/-2.5 micrometers. The material shall have good thermal shock resistance, high hardenability, excellent wear resistance, and hot toughness such as AISI (American Iron and Steel Institute) Type H13. The material shall be heat treated with a method such as Rockwell Hardness Scale €œC € with the hardness scale between 51 and 53 (air or oil quenched above 1000?C), which is the most common heat treatment for nozzle manufacturing. The wear rate of the nozzle internal surface shall be minimized and be equivalent to the current production common-rail diesel injector nozzle wear rates.
The nozzle shall be a stand-alone component with the following requirements: €¢ Houses the needle and provides the needle seat €¢ Accommodates the hydraulic circuitry for needle motion and fuel delivery below the seat €¢ Interfaces with the control valve €¢ Provides a small sack volume below the seat for orifice intersection €¢ Operates up to 15,000 psi (or 1035 bar) €¢ Accommodates 1 to 8 orifices at the nozzle tip €¢ Ability to custom configure the number of orifices, size, spray angles and directions from an undrilled €œBlank € needle/nozzle set €¢ Injection quantity: 0.5 to 45 mm3/cycle €¢ Cycle to cycle variability: less than 2%
PHASE I: Develop €˜novel €™ micro direct fuel injection system concepts which can provide appropriate fuel-air mixture for efficient combustion in small internal combustion engines. The technology shall be evaluated through fluid flow analysis for injection characteristics conducive to small engine environments. Assess the manufacturability of the proposed technology identifying the methods and equipment capable of production. Phase I shall be assessed based on the micro injector design concepts, manufacturing processes and machining capability, and nozzle internal flow and spray analytical analysis in small engine environment (i.e. Shadow UAV engine). The parameters for the analysis shall include nozzle inlet diameter, nozzle outlet diameter, nozzle shaping, sac volume, nozzle orifice orientation, and discharge coefficient among others.
PHASE II: Develop and demonstrate the technology and manufacturing methods. Assess injector fuel charge preparation through experimental spray testing and analysis as well as 3-dimensional computational fluid dynamics (3-D CFD) analysis. Characteristics should include minimum injection quantity, cycle-to-cycle variability, rate of injection, and spray patterns among others at various fuel injection pressures, injection quantities, and multiple injections. Manufacturing assessment shall evaluate the method, repeatability, and tolerance holding capability by measuring nozzle geometries with scanning electron microscope (SEM) or scanning acoustic microscopy. The assessment shall be made according to the requirements in the description section. Deliverables should include the reports, test and analysis results, manufactured prototype injector(s).
PHASE III: Develop and demonstrate a fuel injection system that can be integrated with small engines (3-70 horsepower) for unmanned aerial and ground systems. This system should be available for future Army and commercial unmanned aerial and ground systems. This heavy-fuel (i.e. Jet Propellant-8 (JP-8)) injection system should lead to the development of higher engine performance, higher fuel economy, lower noise, and reliable engines for unmanned systems. The developed fuel system could be implemented as a JP-8 fuel injection system for the Shadow Unmanned Aerial Vehicle (UAV) engine (currently it uses a 38-horsepower rotary engine with aviation gasoline). The demand for small UAVs is projected to grow not only in the military but also in the commercial applications. The developed fuel injection systems could facilitate the development of small UAV engines fueled with heavy fuels such as JP-8, Jet A, diesel, and alternative heavy fuels. Increased demand in the commercial sector would enhance the research and development in small engines. This would lead to more advanced propulsion systems for future DoD UAV systems.
REFERENCES: 1. Tanya J., Gibson, €œARL opens unique combustion research lab, studies in JP-8 fuel could lead to "super engine" development. € U.S. Army Research Laboratory (http://www.arl.army.mil/www/default.cfm?page=1217), October 9, 2012.
2. C-B. M. Kweon, €œA Review of Heavy-Fueled Rotary Engine Combustion Technologies, € ARL-TR-5546, 2011.
3. Mashayek, F., €œSTTR Phase I: Electrostatic Atomizing Fuel Injector for Small Scale Engines, € Report No. EES-DD0010, U.S. Army Research Office: Research Triangle Park, NC, 2008.
4. Hoogterp-Decker, L. and Schihl, P., €œThe Use of Synthetic JP-8 Fuels in Military Engines, € 27th Army Science Conference, Dec. 2, 2010.
5. Schihl, P. and Hoogterp-Decker, L., €œOn the Ignition and Combustion Variances of Jet Propellant-8 and Diesel Fuel in Military Diesel Engines, € TACOM/TARDEC-19172RC, 2008.
6. Pisano, A., Fernandez-Pello, C., McCoy, C., Reville, J., and Limtiaco, J., €œFinal Report: Fuel Flexible Rotary Engine for Portable Power Applications, € Report No. 53049-EG.2, U.S. Army Research Office: Research Triangle Park, NC, 2010.
7. Staley C.S., Morris, C.J., and Currano, L.J., €œDevelopment of Nanoenergetic Micro-fluidic Jet Injectors, € ARL-TR-5872, 2012.
8. Brandt, A.C. and Yost, D.M., €œEvaluation of Military Fuels Using a Ford 6.7L Powerstroke Diesel Engine, € Interim Report TFLRF No. 415, Southwest Research Institute (SwRI), 2011.
9. Chang, C.I., €œFundamentals and Innovations of Army Energy Conversion Systems, € Symposium on Energy Conversion Fundamentals, Istanbul, Turkey, June 21-25, 2004.
KEYWORDS: compression ignition, heavy fuel, fuel injection system, direct injection, small engines, unmanned aerial system, unmanned ground system, Jet Propellant-8, efficiency, performance, injector, spray
TPOC: Dr. Chol-Bum Kweon Phone: 410-278-9319 Email: chol-bum.m.kweon@us.army.mil
Copyright © Zyn Systems 2013, all rights reserved |

