Posted On: 07/18/2013 7:43:01 AM
Post# of 1508
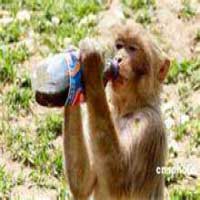
Here is an article with all kinds of information about gasification.
http://www.clean-energy.us/facts/gasification.htm
About Gasification
Proven in the United States and around the world, gasification produces fuel, chemicals, fertilizer, and other products from coal.
Bookmarks
Gasification: The Logical Hydrocarbon Alternative
What is Gasification?
How does gasification differ from combustion?
What are the primary gasification technologies?
What is the history of gasification?
Where is gasification in use at present?
What is the future of gasification?
Why is gasification so important?
How serious is America's natural gas crisis?
Can syngas really replace natural gas in the industrial sector?
Under what conditions could such substitution occur?
Gasification: The Logical Hydrocarbon Alternative
Modern life depends upon energy and with each passing day it becomes more evident that clean, climate-friendly, and affordable energy technologies must be deployed as rapidly as possible. To that end, the United States and other nations are striving to make wind, solar, geothermal, hydrogen, and other “green” technologies a larger part of their overall energy mix.
However, for technical and economic reasons, it will be many decades before these resources can meet more than a fraction of the world’s energy demand. In the meantime, developed countries such as the United States and developing nations such as China and India will continue to rely upon hydrocarbons (natural gas, petroleum, and coal) for electricity generation and transportation fuel. So, it is fair to ask: What are our hydrocarbon options?
Natural Gas. This clean-burning hydrocarbon is in great demand both as a fuel to heat homes and run powerplants and as a raw material for the manufacture of chemicals and fertilizer. As a result, a supply/demand imbalance exists in the United States and many other countries. Because of this imbalance, the price of natural gas is (and is projected to remain) too expensive for use in baseload (24-7) electric powerplants or as a substitute for gasoline or diesel fuel.
Petroleum. This hydrocarbon is also in high demand around the world and there is a corresponding supply/demand disparity. But even if the demand for petroleum were to decline or the supply to increase, we would not want – for environmental reasons – to boost global consumption of gasoline, diesel, and other petroleum-based fuels. Also, like natural gas, petroleum is an important raw material for the production of chemicals and other high-value products. A strong case can be made that at least some of the world’s finite oil and gas resources ought to be conserved for such uses.
Coal. Unlike oil and natural gas, coal is plentiful and inexpensive. The problem with coal – like one of the fundamental problems with petroleum – is that the combustion of coal creates air pollutants and carbon dioxide (CO2). Although government and industry have cooperatively developed new “clean coal” technologies over the last three decades, there is still significant public opposition to the construction of coal-fired powerplants. Such opposition arises because even the newest coal-fired plants emit criteria air pollutants (albeit at greatly reduced levels), airborne mercury, and millions of tons per year of CO2 (which many scientists believe to be a major force in global climate change).
Gasification. There is another hydrocarbon option, however, and it is gaining momentum. This alternative is gasification, a process by which coal or other low-value hydrocarbons are gasified in a large chemical reactor. The resulting synthesis gas is cleansed and then used to fire an electric powerplant and/or converted into high-value products such as synthetic fuels, chemicals, and fertilizers. What makes gasification a “breakthrough” technology is that it combines the economic advantages of coal with the environmental benefits of natural gas.
What is gasification?
Gasification is a term that describes a chemical process by which carbonaceous (hydrocarbon) materials (coal, petroleum coke, biomass, etc.) are converted to a synthesis gas (syngas) by means of partial oxidation with air, oxygen, and/or steam.
Modern gasification technologies generally operate as follows:
A hydrocarbon feedstock is fed into a high-pressure, high-temperature chemical reactor (gasifier) containing steam and a limited amount of oxygen.
Under these “reducing” conditions, the chemical bonds in the feedstock are severed by the extreme heat and pressure and a syngas is formed. This syngas is primarily a mixture of hydrogen and carbon monoxide.
The syngas is then cleansed using commercially available and proven systems that remove particulates, sulfur, and trace metals (e.g. mercury).
Gasification is truly a breakthrough technology. Although syngas has lower heating value than natural gas, it can still be used in highly-efficient combined cycle electric powerplants or to make many products presently made from natural gas, including ammonia fertilizers, methanol-derived chemicals, and clean-burning synthetic fuels.
How does gasification differ from combustion?
Combustion (or burning) is an exothermic (heat releasing) reaction between a fuel and an oxidizer and (for a carbonaceous fuel) may be expressed:
Fuel + Oxygen ? Heat + Water + Carbon Dioxide
Gasification is an exothermic reaction between a carbonaceous fuel and an oxidizer in a reactor where the oxygen supply is limited (generally from 20 to 70 percent of the oxygen for complete combustion). The reaction may be expressed:
Fuel + Oxygen (limited) ? Hydrogen + Carbon Monoxide (+ some Water & Carbon Dioxide)
What are the primary gasification technologies?
Although many designs have been developed, modern gasification technologies generally fall into three categories depending upon the flow conditions in the gasifier: (1) moving bed; (2) entrained flow; and (3) fluidized bed. These basic gasifier designs – originally developed in the 1950s – were all reengineered in the 1970s and 1980s to operate under greater pressure. (Greater pressure increases the productive capacity of the gasifier and makes possible a broader range of syngas applications.)
Moving bed. The carbonaceous fuel is dry-fed through the top of the reactor. As the fuel slowly descends, it reacts with the gasifying agents (steam and oxygen) flowing in a counter-current through the bed. The fuel goes through the various stages of gasification until it is ultimately consumed, leaving only syngas and a dry or molten ash. The syngas has a low temperature (400-500ºC) and contains significant quantities of tars and oils.
Entrained flow. The fuel and gasifying agents flow in the same direction (and at rates in excess of other gasifier types). The feedstock – which may be dry-fed (mixed with nitrogen) or wet-fed (mixed with water) – goes through the various stages of gasification as it moves with the steam/oxygen flow. The syngas exits through the top of the reactor and the ashes flow down the sides as a molten slag, which is removed from the bottom. Operating temperatures are very high (1200-1600ºC).
Fluidized bed. The fuel, introduced into an upward flow of steam/oxygen, remains suspended in the gasifying agents while the gasification process takes place. Since the operating temperature of the reactor (800-1050ºC) is less than the temperature at which the ashes from the fuel melt, these can be removed either in dry form or as agglomerate.
What is the history of gasification?
Although gasification was invented in the early-1800s, the technology has undergone a complete transformation in the last 50 years (with the most rapid changes in the last two decades). Gasification has gone through five stages:
1850 to 1940. Gasification was first used to produce “town gas” for light and heat. And –until development of natural gas supplies and transmission lines in the 1940s and 1950s –virtually all gas for fuel and light was manufactured from the gasification of coal.
1940 to 1975. The second stage of gasification began during World War II when German engineers used gasification to produce synthetic fuel. This technology was exported to South Africa in the 1950s, where it was further developed to produce liquid fuels and chemicals.
1975 to 1990. The next stage in the evolution of gasification began after the Arab Oil Embargo of 1973. In reaction to that event and the ensuing “energy crisis,” the U.S. government provided financial support for several proof-of-concept gasification projects, including the world’s first Integrated Gasification Combined Cycle (IGCC) electric powerplant. Another seminal event during this period was conversion of Eastman Chemical’s flagship manufacturing plant from petroleum to syngas from coal.
1990 to 2000. The fourth stage of gasification’s development began in the early 1990s when government agencies in the United States and Europe provided financial support to four medium-sized (˜ 250 MWe) projects to further “demonstrate” the feasibility of the IGCC process.
2000 to present. The current stage in the evolution of gasification began when commercial developers started building IGCC powerplants without government subsidies. These new IGCC facilities (all outside the United States) are adjacent to refineries where petroleum coke and other residual hydrocarbons are readily available.
Where is gasification in use at present?
In 2004, The Gasification Technologies Council conducted a survey of global gasifier use and projected development. The GTC survey identified 385 gasifiers in use at some 177 projects in 27 nations. Major projects are operating successfully on four continents:
Africa. The world’s larges concentration of gasifiers is in South Africa where synthetic fuels and chemicals have been produced from coal since 1955. The gasification projects at Sasol and Secunda use some 100 gasifiers to produce more than 40 percent of South Africa’s liquid fuels and a variety of chemical products.
Asia. Gasification plants are operating in India, China, and Japan. The Indian projects produce ammonia fertilizer at __ sites, the Chinese projects produce fertilizer or chemicals at __ locations, and the Japanese project produces electricity from petcoke at a refinery in Yokohama.
Europe. There are five large IGCC projects operating in Western Europe, with the greatest concentration in Italy. The three Italian projects produce more than 1,500 MWe of electricity from refinery residuals at Priolo (Sicily), Sarroch (Sardinia), and Sannazzaro (Northern Italy). The other IGCC projects – located at Puertollano (Spain) and Buggenum (Netherlands) – generate electricity from coal and petcoke.
North America. Gasification is used to produce chemicals, fertilizers, and electricity at several sites across the United States. Major projects include a coal-to-chemicals facility in Kingsport, Tennessee; a coal-to-methane (natural gas) project in Buelah, North Dakota; an ammonia fertilizer plant in Coffeeville, Kansas; and IGCC powerplants in Tampa, Florida, and Terra Haute, Indiana.
What is the future of gasification?
Gasification is a technology on the threshold of extraordinary growth. Dozens of projects are under design and construction in the United States and around the globe. Here is one likely scenario based on the 2004 Gasification Technologies Council survey and general industry consensus:
2005 to 2010. During this period the IGCC process will be used to produce electricity at refineries in the United States from petcoke and similar materials. New coal-based projects will greatly expand the production of chemicals in China. And, an entirely new application will be seen in Canada, where syngas from gasification will be used to increase petroleum production in the Alberta oil sand fields.
2010 to 2015. The first generation of large-scale (500 MWe or greater) coal-based IGCC powerplants will come online in the United States. These projects will further demonstrate to regulators and lenders that such projects are technically and financially sound. Gasification use for fertilizer and chemical production will grow dramatically (particularly in China).
2015 to 2025. The second generation of large-scale IGCC plants will be built. They will take advantage of “lessons learned” in prior IGCC installations and may be sited at locations where the carbon dioxide created in the plants can be captured and stored in underground geological formations. Such projects may also be designed with the flexibility to produce power, chemicals, fuels, and other products depending upon prevailing market conditions.
Why is gasification so important?
The world’s hydrocarbon resources are both finite and unevenly distributed. For nations such as the United States – with dwindling reserves of petroleum and natural gas – the only pathway to a future where energy prices are affordable and relatively stable is to conserve energy, improve energy efficiency, and produce electric power, chemicals, fertilizers, and transportation fuels from abundant (and thus relatively low-cost) domestic resources such as coal.
Gasification (especially of coal) is important because the syngas produced by this process could replace natural gas as the “fuel of choice” in the generation of electricity and literally help save America’s fertilizer and chemical industries. In addition, coal gasification can be used – as South Africa has successfully demonstrated for more than 50 years – to create very large volumes of clean-burning synthetic fuels.
The capability of gasification to displace natural gas and petroleum is reason enough to encourage widespread and rapid deployment of this proven technology. There are, however, at least three other reasons why gasification ought to be the technology of choice for these challenging times:
Syngas from gasification is thoroughly cleansed before it is used in an IGCC powerplant. Thus it is possible to virtually eliminate emissions of criteria air pollutants and hazardous pollutants such as volatile mercury from coal-based power projects that employ this technology.
Unlike natural gas or other coal systems, gasification-based powerplants can be cost-effectively configured (or retrofitted) to enable carbon dioxide capture if and when that is required to meet statutory or international treaty obligations.
Because gasification produces a syngas of hydrogen and carbon monoxide, it is the only conventional energy technology (besides nuclear fission) capable of producing the massive quantities of hydrogen that would be required to convert all or a major portion of the world’s transportation fleet from gasoline and diesel fuel to hydrogen.
Despite these other advantages, the primary interest in gasification is as a substitute for natural gas in the power, chemical, and fertilizer industries. The urgency of such substitution is explained below.
How serious is America's natural gas crisis?
Demand for natural gas exceeds supply in all segments of the U.S. economy. As a result, natural gas prices have been at sustained high levels for the past five years and there is no relief in sight. This situation – described as a natural gas “crisis” by many observers – has had many deleterious effects:
The Fertilizer Institute reports that anhydrous ammonia fertilizer production in the United States declined by 35 percent between 1998 and 2004 and that “further domestic fertilizer company bankruptcies, buyouts, and reorganizations” are inevitable.
The American Chemistry Council states that more than 70 percent of the basic chemicals made in the United States are derived from natural gas and that “every $1.00 increase in the cost of natural gas, adds $3.7 billion in costs to the industry.”
A 2004 study by SAIC for the U.S. Department of Energy indicated that: (1) there are nearly 200 natural gas powerplants larger than 250 MWe in the United States; (2) the average capacity factor (usage rate) for those plants from 2000 to 2003 was less than 35 percent; and (3) 24 of these plants “are either for sale or bank owned.”
Can syngas really replace natural gas in the industrial sector?
Syngas produced from the gasification of coal and other carbonaceous materials could completely supplant natural gas in many critical industrial and electric power applications:
To produce fertilizer, the hydrogen fraction of the syngas can be combined with nitrogen distilled from air to produce anhydrous ammonia. This product can either be applied directly to the soil or reformulated to produce other fertilizers.
To make chemicals, the carbon monoxide and hydrogen components of the syngas can be reacted over a catalyst (usually a mixture of copper, zinc oxide, and alumina) to make methanol. The methanol can be further refined into acetic acid and/or formaldehyde, two basic chemical building-blocks.
To create synthetic fuels, the hydrogen and carbon monoxide in the syngas, can be reacted in the presence of an iron or cobalt catalyst to produce such products as methane, synthetic gasoline and waxes, and alcohols. (This is the so-called Fischer-Tropsch process.)
And, to generate electricity, syngas can be used in highly-efficient integrated gasification combined cycle powerplants.
Under what conditions could such substitution occur?
Natural gas price increases in recent years have already destroyed significant demand for natural gas in industrial applications. As discussed above, fertilizer, chemical, and gas-fired electric power producers have been hit particularly hard.
It is uncertain whether the losses in productive capacity in the chemical and fertilizer industries will ever return to pre-2000 levels. Nonetheless, there are significant opportunities to convert many operating (and even some shuttered) methanol and ammonia manufacturing facilities from natural gas to syngas produced from coal. Key factors in determining the viability of such conversions include: (1) natural gas prices; (2) delivered coal prices; and (3) access to the capital (˜$500 million) needed for the conversion from natural gas to coal-derived syngas.
In the electric power sector, on the other hand, there are tremendous opportunities for syngas to replace natural gas in highly-efficient combined cycle powerplants. IGCC Electric Power
$IFTF$
http://www.clean-energy.us/facts/gasification.htm
About Gasification
Proven in the United States and around the world, gasification produces fuel, chemicals, fertilizer, and other products from coal.
Bookmarks
Gasification: The Logical Hydrocarbon Alternative
What is Gasification?
How does gasification differ from combustion?
What are the primary gasification technologies?
What is the history of gasification?
Where is gasification in use at present?
What is the future of gasification?
Why is gasification so important?
How serious is America's natural gas crisis?
Can syngas really replace natural gas in the industrial sector?
Under what conditions could such substitution occur?
Gasification: The Logical Hydrocarbon Alternative
Modern life depends upon energy and with each passing day it becomes more evident that clean, climate-friendly, and affordable energy technologies must be deployed as rapidly as possible. To that end, the United States and other nations are striving to make wind, solar, geothermal, hydrogen, and other “green” technologies a larger part of their overall energy mix.
However, for technical and economic reasons, it will be many decades before these resources can meet more than a fraction of the world’s energy demand. In the meantime, developed countries such as the United States and developing nations such as China and India will continue to rely upon hydrocarbons (natural gas, petroleum, and coal) for electricity generation and transportation fuel. So, it is fair to ask: What are our hydrocarbon options?
Natural Gas. This clean-burning hydrocarbon is in great demand both as a fuel to heat homes and run powerplants and as a raw material for the manufacture of chemicals and fertilizer. As a result, a supply/demand imbalance exists in the United States and many other countries. Because of this imbalance, the price of natural gas is (and is projected to remain) too expensive for use in baseload (24-7) electric powerplants or as a substitute for gasoline or diesel fuel.
Petroleum. This hydrocarbon is also in high demand around the world and there is a corresponding supply/demand disparity. But even if the demand for petroleum were to decline or the supply to increase, we would not want – for environmental reasons – to boost global consumption of gasoline, diesel, and other petroleum-based fuels. Also, like natural gas, petroleum is an important raw material for the production of chemicals and other high-value products. A strong case can be made that at least some of the world’s finite oil and gas resources ought to be conserved for such uses.
Coal. Unlike oil and natural gas, coal is plentiful and inexpensive. The problem with coal – like one of the fundamental problems with petroleum – is that the combustion of coal creates air pollutants and carbon dioxide (CO2). Although government and industry have cooperatively developed new “clean coal” technologies over the last three decades, there is still significant public opposition to the construction of coal-fired powerplants. Such opposition arises because even the newest coal-fired plants emit criteria air pollutants (albeit at greatly reduced levels), airborne mercury, and millions of tons per year of CO2 (which many scientists believe to be a major force in global climate change).
Gasification. There is another hydrocarbon option, however, and it is gaining momentum. This alternative is gasification, a process by which coal or other low-value hydrocarbons are gasified in a large chemical reactor. The resulting synthesis gas is cleansed and then used to fire an electric powerplant and/or converted into high-value products such as synthetic fuels, chemicals, and fertilizers. What makes gasification a “breakthrough” technology is that it combines the economic advantages of coal with the environmental benefits of natural gas.
What is gasification?
Gasification is a term that describes a chemical process by which carbonaceous (hydrocarbon) materials (coal, petroleum coke, biomass, etc.) are converted to a synthesis gas (syngas) by means of partial oxidation with air, oxygen, and/or steam.
Modern gasification technologies generally operate as follows:
A hydrocarbon feedstock is fed into a high-pressure, high-temperature chemical reactor (gasifier) containing steam and a limited amount of oxygen.
Under these “reducing” conditions, the chemical bonds in the feedstock are severed by the extreme heat and pressure and a syngas is formed. This syngas is primarily a mixture of hydrogen and carbon monoxide.
The syngas is then cleansed using commercially available and proven systems that remove particulates, sulfur, and trace metals (e.g. mercury).
Gasification is truly a breakthrough technology. Although syngas has lower heating value than natural gas, it can still be used in highly-efficient combined cycle electric powerplants or to make many products presently made from natural gas, including ammonia fertilizers, methanol-derived chemicals, and clean-burning synthetic fuels.
How does gasification differ from combustion?
Combustion (or burning) is an exothermic (heat releasing) reaction between a fuel and an oxidizer and (for a carbonaceous fuel) may be expressed:
Fuel + Oxygen ? Heat + Water + Carbon Dioxide
Gasification is an exothermic reaction between a carbonaceous fuel and an oxidizer in a reactor where the oxygen supply is limited (generally from 20 to 70 percent of the oxygen for complete combustion). The reaction may be expressed:
Fuel + Oxygen (limited) ? Hydrogen + Carbon Monoxide (+ some Water & Carbon Dioxide)
What are the primary gasification technologies?
Although many designs have been developed, modern gasification technologies generally fall into three categories depending upon the flow conditions in the gasifier: (1) moving bed; (2) entrained flow; and (3) fluidized bed. These basic gasifier designs – originally developed in the 1950s – were all reengineered in the 1970s and 1980s to operate under greater pressure. (Greater pressure increases the productive capacity of the gasifier and makes possible a broader range of syngas applications.)
Moving bed. The carbonaceous fuel is dry-fed through the top of the reactor. As the fuel slowly descends, it reacts with the gasifying agents (steam and oxygen) flowing in a counter-current through the bed. The fuel goes through the various stages of gasification until it is ultimately consumed, leaving only syngas and a dry or molten ash. The syngas has a low temperature (400-500ºC) and contains significant quantities of tars and oils.
Entrained flow. The fuel and gasifying agents flow in the same direction (and at rates in excess of other gasifier types). The feedstock – which may be dry-fed (mixed with nitrogen) or wet-fed (mixed with water) – goes through the various stages of gasification as it moves with the steam/oxygen flow. The syngas exits through the top of the reactor and the ashes flow down the sides as a molten slag, which is removed from the bottom. Operating temperatures are very high (1200-1600ºC).
Fluidized bed. The fuel, introduced into an upward flow of steam/oxygen, remains suspended in the gasifying agents while the gasification process takes place. Since the operating temperature of the reactor (800-1050ºC) is less than the temperature at which the ashes from the fuel melt, these can be removed either in dry form or as agglomerate.
What is the history of gasification?
Although gasification was invented in the early-1800s, the technology has undergone a complete transformation in the last 50 years (with the most rapid changes in the last two decades). Gasification has gone through five stages:
1850 to 1940. Gasification was first used to produce “town gas” for light and heat. And –until development of natural gas supplies and transmission lines in the 1940s and 1950s –virtually all gas for fuel and light was manufactured from the gasification of coal.
1940 to 1975. The second stage of gasification began during World War II when German engineers used gasification to produce synthetic fuel. This technology was exported to South Africa in the 1950s, where it was further developed to produce liquid fuels and chemicals.
1975 to 1990. The next stage in the evolution of gasification began after the Arab Oil Embargo of 1973. In reaction to that event and the ensuing “energy crisis,” the U.S. government provided financial support for several proof-of-concept gasification projects, including the world’s first Integrated Gasification Combined Cycle (IGCC) electric powerplant. Another seminal event during this period was conversion of Eastman Chemical’s flagship manufacturing plant from petroleum to syngas from coal.
1990 to 2000. The fourth stage of gasification’s development began in the early 1990s when government agencies in the United States and Europe provided financial support to four medium-sized (˜ 250 MWe) projects to further “demonstrate” the feasibility of the IGCC process.
2000 to present. The current stage in the evolution of gasification began when commercial developers started building IGCC powerplants without government subsidies. These new IGCC facilities (all outside the United States) are adjacent to refineries where petroleum coke and other residual hydrocarbons are readily available.
Where is gasification in use at present?
In 2004, The Gasification Technologies Council conducted a survey of global gasifier use and projected development. The GTC survey identified 385 gasifiers in use at some 177 projects in 27 nations. Major projects are operating successfully on four continents:
Africa. The world’s larges concentration of gasifiers is in South Africa where synthetic fuels and chemicals have been produced from coal since 1955. The gasification projects at Sasol and Secunda use some 100 gasifiers to produce more than 40 percent of South Africa’s liquid fuels and a variety of chemical products.
Asia. Gasification plants are operating in India, China, and Japan. The Indian projects produce ammonia fertilizer at __ sites, the Chinese projects produce fertilizer or chemicals at __ locations, and the Japanese project produces electricity from petcoke at a refinery in Yokohama.
Europe. There are five large IGCC projects operating in Western Europe, with the greatest concentration in Italy. The three Italian projects produce more than 1,500 MWe of electricity from refinery residuals at Priolo (Sicily), Sarroch (Sardinia), and Sannazzaro (Northern Italy). The other IGCC projects – located at Puertollano (Spain) and Buggenum (Netherlands) – generate electricity from coal and petcoke.
North America. Gasification is used to produce chemicals, fertilizers, and electricity at several sites across the United States. Major projects include a coal-to-chemicals facility in Kingsport, Tennessee; a coal-to-methane (natural gas) project in Buelah, North Dakota; an ammonia fertilizer plant in Coffeeville, Kansas; and IGCC powerplants in Tampa, Florida, and Terra Haute, Indiana.
What is the future of gasification?
Gasification is a technology on the threshold of extraordinary growth. Dozens of projects are under design and construction in the United States and around the globe. Here is one likely scenario based on the 2004 Gasification Technologies Council survey and general industry consensus:
2005 to 2010. During this period the IGCC process will be used to produce electricity at refineries in the United States from petcoke and similar materials. New coal-based projects will greatly expand the production of chemicals in China. And, an entirely new application will be seen in Canada, where syngas from gasification will be used to increase petroleum production in the Alberta oil sand fields.
2010 to 2015. The first generation of large-scale (500 MWe or greater) coal-based IGCC powerplants will come online in the United States. These projects will further demonstrate to regulators and lenders that such projects are technically and financially sound. Gasification use for fertilizer and chemical production will grow dramatically (particularly in China).
2015 to 2025. The second generation of large-scale IGCC plants will be built. They will take advantage of “lessons learned” in prior IGCC installations and may be sited at locations where the carbon dioxide created in the plants can be captured and stored in underground geological formations. Such projects may also be designed with the flexibility to produce power, chemicals, fuels, and other products depending upon prevailing market conditions.
Why is gasification so important?
The world’s hydrocarbon resources are both finite and unevenly distributed. For nations such as the United States – with dwindling reserves of petroleum and natural gas – the only pathway to a future where energy prices are affordable and relatively stable is to conserve energy, improve energy efficiency, and produce electric power, chemicals, fertilizers, and transportation fuels from abundant (and thus relatively low-cost) domestic resources such as coal.
Gasification (especially of coal) is important because the syngas produced by this process could replace natural gas as the “fuel of choice” in the generation of electricity and literally help save America’s fertilizer and chemical industries. In addition, coal gasification can be used – as South Africa has successfully demonstrated for more than 50 years – to create very large volumes of clean-burning synthetic fuels.
The capability of gasification to displace natural gas and petroleum is reason enough to encourage widespread and rapid deployment of this proven technology. There are, however, at least three other reasons why gasification ought to be the technology of choice for these challenging times:
Syngas from gasification is thoroughly cleansed before it is used in an IGCC powerplant. Thus it is possible to virtually eliminate emissions of criteria air pollutants and hazardous pollutants such as volatile mercury from coal-based power projects that employ this technology.
Unlike natural gas or other coal systems, gasification-based powerplants can be cost-effectively configured (or retrofitted) to enable carbon dioxide capture if and when that is required to meet statutory or international treaty obligations.
Because gasification produces a syngas of hydrogen and carbon monoxide, it is the only conventional energy technology (besides nuclear fission) capable of producing the massive quantities of hydrogen that would be required to convert all or a major portion of the world’s transportation fleet from gasoline and diesel fuel to hydrogen.
Despite these other advantages, the primary interest in gasification is as a substitute for natural gas in the power, chemical, and fertilizer industries. The urgency of such substitution is explained below.
How serious is America's natural gas crisis?
Demand for natural gas exceeds supply in all segments of the U.S. economy. As a result, natural gas prices have been at sustained high levels for the past five years and there is no relief in sight. This situation – described as a natural gas “crisis” by many observers – has had many deleterious effects:
The Fertilizer Institute reports that anhydrous ammonia fertilizer production in the United States declined by 35 percent between 1998 and 2004 and that “further domestic fertilizer company bankruptcies, buyouts, and reorganizations” are inevitable.
The American Chemistry Council states that more than 70 percent of the basic chemicals made in the United States are derived from natural gas and that “every $1.00 increase in the cost of natural gas, adds $3.7 billion in costs to the industry.”
A 2004 study by SAIC for the U.S. Department of Energy indicated that: (1) there are nearly 200 natural gas powerplants larger than 250 MWe in the United States; (2) the average capacity factor (usage rate) for those plants from 2000 to 2003 was less than 35 percent; and (3) 24 of these plants “are either for sale or bank owned.”
Can syngas really replace natural gas in the industrial sector?
Syngas produced from the gasification of coal and other carbonaceous materials could completely supplant natural gas in many critical industrial and electric power applications:
To produce fertilizer, the hydrogen fraction of the syngas can be combined with nitrogen distilled from air to produce anhydrous ammonia. This product can either be applied directly to the soil or reformulated to produce other fertilizers.
To make chemicals, the carbon monoxide and hydrogen components of the syngas can be reacted over a catalyst (usually a mixture of copper, zinc oxide, and alumina) to make methanol. The methanol can be further refined into acetic acid and/or formaldehyde, two basic chemical building-blocks.
To create synthetic fuels, the hydrogen and carbon monoxide in the syngas, can be reacted in the presence of an iron or cobalt catalyst to produce such products as methane, synthetic gasoline and waxes, and alcohols. (This is the so-called Fischer-Tropsch process.)
And, to generate electricity, syngas can be used in highly-efficient integrated gasification combined cycle powerplants.
Under what conditions could such substitution occur?
Natural gas price increases in recent years have already destroyed significant demand for natural gas in industrial applications. As discussed above, fertilizer, chemical, and gas-fired electric power producers have been hit particularly hard.
It is uncertain whether the losses in productive capacity in the chemical and fertilizer industries will ever return to pre-2000 levels. Nonetheless, there are significant opportunities to convert many operating (and even some shuttered) methanol and ammonia manufacturing facilities from natural gas to syngas produced from coal. Key factors in determining the viability of such conversions include: (1) natural gas prices; (2) delivered coal prices; and (3) access to the capital (˜$500 million) needed for the conversion from natural gas to coal-derived syngas.
In the electric power sector, on the other hand, there are tremendous opportunities for syngas to replace natural gas in highly-efficient combined cycle powerplants. IGCC Electric Power
$IFTF$

