(Total Views: 410)
Posted On: 06/29/2021 12:41:16 AM
Post# of 1425
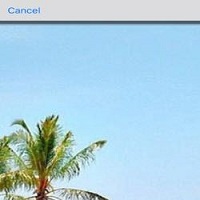
https://twitter.com/thehamsammich3/status/140...85/photo/1
https://pbs.twimg.com/media/E4hIKWkWYAcqoPA?f...name=small
Quote:
PCT has designed and built its own equipment for over 20 years which has evolved into state-of-the-art and highly efficient technology and methodology for preparing the highest concentrations of HOCl available in the market today. Pricing for manufacturing HOCl based oxidants and associated antioxidants is based on providing a System-Service Agreement for example: $5000 per month for a four-cell unit capable of producing 1000 gallons per day of up to 500 ppm anolyte. Larger or smaller requirements can be priced accordingly. The product can be produced for a few cents a gallon and sold at competitive rates compared to existing technology or less. In surface sanitizing and disinfection this quantity and rate usually provides more than is required to disinfect thousands of square feet of affected surface area. Fogging or atomizing room surfaces can require as little as one pint to one quart per room such as in hotels or cruise ship staterooms.
The chemistry for producing these products is relatively simple and uses simple clean brine solutions and electricity in PCT’s automated membrane electrolysis equipment to provide on-demand or stored quantities of the various unique oxidizers or antioxidant cleaner. Saltwater (NaCl+H2O) is input past the cathode ( negative voltage) side of a membrane to produce the antioxidant sodium hydroxide and Hydrogen ions or Catholyte an effective and safe alkaline cleaning solution. The same saltwater ( NaCl+H20) input past the anode ( positive voltage) to produce predominately HOCl (hypochlorous acid), as well as lesser amounts of other nascent oxidants, Cl2 (chlorine) or NaOCl ( sodium hypochlorite or bleach), etc. ORP ( oxidation-reduction potential) is the measure of activity for these products with high positive numbers for the oxidants ( >900) and negative ORP ( -900) for the antioxidants. The pH of the anolyte oxidizers is usually 6.5 -7.5 which is near neutral, and alkaline cleaner antioxidants are pH 12-13. .
From an environmental aspect, the anolyte and other oxidants produced from a solution of high purity salt and water create a powerful antimicrobial, disinfection package that is both biodegradable and non-accumulative. The crucial active ingredient hypochlorous acid (HOCl) is derived from naturally occurring salt minerals and water. PCT oxidizer products achieve industrial performance standards with respect to production efficiency and optimum efficacy while maintaining a minimum FAC ( free available chlorine) of 500 ppm. They are non-flammable and contain no alcohol. They can be transported as a non-chemical with no strict HAZMAT requirements. These oxidizers are composed of 99,5 % water and yet they effectively and rapidly kill viruses and bacteria thus providing better alternatives to harmful chemicals in use today.
Applications of the technology have been made in the hospital, healthcare, food processing, and petroleum markets. In healthcare the ECA oxidizers and antioxidants are available as a commercially ready, patented, integrated product and technology solution for complete facility cleaning and sanitizing. The PCT’s infection control System is designed for use in hospitals, urgent care centers, dental and veterinary practices, nursing homes and other large healthcare facilities. Microbes cannot develop resistance to these cleaning and sanitizing products as they actually penetrate the cell walls of the micro-organisms rendering them unable to shield themselves from the effects of the ECA oxidizer’s (anolyte) effects.
The oil and gas industry has used ECA anolyte solutions to treat sulfate-reducing bacteria ( SRB’s) in several wells for Yates Petroleum (now Anadarko) thereby reducing the losses due to corrosion causing expensive rod and tubing failures in pumping wells at costs up to $100,000 per well in some cases. The corrosion is caused by sulfate-reducing bacteria and subsequent H2S. Anolyte treated wells showed production upticks of up to 20% in many cases. The wellbore remediation/production enhancement from using the ECA anolyte has shown promising results in Utah, North Dakota as well as Texas, Oklahoma, and New Mexico.
>>> Data source: David Holcomb's website: https://www.pentechnologies.net/
Dr. Holcomb is President, Technical Innovation Consulting; Pentechnologies
https://pbs.twimg.com/media/E4hIKWkWYAcqoPA?f...name=small
Quote:
PCT has designed and built its own equipment for over 20 years which has evolved into state-of-the-art and highly efficient technology and methodology for preparing the highest concentrations of HOCl available in the market today. Pricing for manufacturing HOCl based oxidants and associated antioxidants is based on providing a System-Service Agreement for example: $5000 per month for a four-cell unit capable of producing 1000 gallons per day of up to 500 ppm anolyte. Larger or smaller requirements can be priced accordingly. The product can be produced for a few cents a gallon and sold at competitive rates compared to existing technology or less. In surface sanitizing and disinfection this quantity and rate usually provides more than is required to disinfect thousands of square feet of affected surface area. Fogging or atomizing room surfaces can require as little as one pint to one quart per room such as in hotels or cruise ship staterooms.
The chemistry for producing these products is relatively simple and uses simple clean brine solutions and electricity in PCT’s automated membrane electrolysis equipment to provide on-demand or stored quantities of the various unique oxidizers or antioxidant cleaner. Saltwater (NaCl+H2O) is input past the cathode ( negative voltage) side of a membrane to produce the antioxidant sodium hydroxide and Hydrogen ions or Catholyte an effective and safe alkaline cleaning solution. The same saltwater ( NaCl+H20) input past the anode ( positive voltage) to produce predominately HOCl (hypochlorous acid), as well as lesser amounts of other nascent oxidants, Cl2 (chlorine) or NaOCl ( sodium hypochlorite or bleach), etc. ORP ( oxidation-reduction potential) is the measure of activity for these products with high positive numbers for the oxidants ( >900) and negative ORP ( -900) for the antioxidants. The pH of the anolyte oxidizers is usually 6.5 -7.5 which is near neutral, and alkaline cleaner antioxidants are pH 12-13. .
From an environmental aspect, the anolyte and other oxidants produced from a solution of high purity salt and water create a powerful antimicrobial, disinfection package that is both biodegradable and non-accumulative. The crucial active ingredient hypochlorous acid (HOCl) is derived from naturally occurring salt minerals and water. PCT oxidizer products achieve industrial performance standards with respect to production efficiency and optimum efficacy while maintaining a minimum FAC ( free available chlorine) of 500 ppm. They are non-flammable and contain no alcohol. They can be transported as a non-chemical with no strict HAZMAT requirements. These oxidizers are composed of 99,5 % water and yet they effectively and rapidly kill viruses and bacteria thus providing better alternatives to harmful chemicals in use today.
Applications of the technology have been made in the hospital, healthcare, food processing, and petroleum markets. In healthcare the ECA oxidizers and antioxidants are available as a commercially ready, patented, integrated product and technology solution for complete facility cleaning and sanitizing. The PCT’s infection control System is designed for use in hospitals, urgent care centers, dental and veterinary practices, nursing homes and other large healthcare facilities. Microbes cannot develop resistance to these cleaning and sanitizing products as they actually penetrate the cell walls of the micro-organisms rendering them unable to shield themselves from the effects of the ECA oxidizer’s (anolyte) effects.
The oil and gas industry has used ECA anolyte solutions to treat sulfate-reducing bacteria ( SRB’s) in several wells for Yates Petroleum (now Anadarko) thereby reducing the losses due to corrosion causing expensive rod and tubing failures in pumping wells at costs up to $100,000 per well in some cases. The corrosion is caused by sulfate-reducing bacteria and subsequent H2S. Anolyte treated wells showed production upticks of up to 20% in many cases. The wellbore remediation/production enhancement from using the ECA anolyte has shown promising results in Utah, North Dakota as well as Texas, Oklahoma, and New Mexico.
>>> Data source: David Holcomb's website: https://www.pentechnologies.net/
Dr. Holcomb is President, Technical Innovation Consulting; Pentechnologies


WORDS TO LIVE BY:
Never argue with stupid people, they will drag you down to their level and then beat you with experience.
Get .... PrivacyLok https://cyberidguard.com/
Try SafeVchat: https://cyberidguard.com/
My comments are only my opinion and are not to be used for investment advice.
Please conduct your own due diligence before choosing to buy or sell any stock.
Never argue with stupid people, they will drag you down to their level and then beat you with experience.
Get .... PrivacyLok https://cyberidguard.com/
Try SafeVchat: https://cyberidguard.com/
My comments are only my opinion and are not to be used for investment advice.
Please conduct your own due diligence before choosing to buy or sell any stock.
