(Total Views: 675)
Posted On: 04/12/2017 11:22:25 PM
Post# of 43068
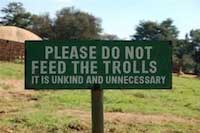
A different process, but. . .
Sonoma County startup Resynergi seeks to recycle plastic trash into diesel fuel
GARY QUACKENBUSH
FOR NORTH BAY BUSINESS JOURNAL | April 12, 2017, 9:35AM
Resynergi LLC has developed what the Rohnert Park company states is a proprietary system using microwaves to transform unrecycled waste plastic into oil. By mid-year the company plans to announce orders from initial customers with equipment deliveries scheduled during the second half.
The technology, called continuous microwave-assisted pyrolysis (CMAP), can recover 250 gallons of clean, reliable diesel fuel from 1 ton of low and high-density polyethylene, polypropylene and polystyrene plastics, also known as plastics Nos. 2, 4, 5 and 6. In addition to its unique heat source, the company says its unit is small, expanding its customer pool to smaller plastic producers.
Those potential customers include carting companies, grocery chains, nonprofits, municipalities, the military, trucking firms and other sectors, according to an American Chemical Council study in 2014.
Plastic waste is mostly free today, as firms wish to offset tipping fees (from $60 to $130/ton) at landfill sites and save transportation expense. These zero-to-low material costs can help customers scale up operations.
“Today’s plastics contain a lot of stored energy in long hydrocarbon chains that can be reclaimed, while also eliminating problems associated with disposal and pollution,” said CEO Brian Bauer, who together with Jason Tanne co-founded Resynergi in April 2015. “However, today we throw most of that latent energy locked up in plastics into the trash. Our mission is to develop evolutionary energy recovery systems designed to change that.”
Some 33.5 million tons of plastic waste are produced annually in the U.S., but only 7 percent is recycled, with most being sent to municipal landfills or shipped overseas, according to the ACC. This mountain of plastic could be worth $29 billion if converted to oil.
The U.S. alone could support 600 plastic-to-oil facilities processing 20 tons of plastic per day while creating 40,000 new jobs, according to EPA, EIA and ACC data sources.
“The recycling landscape is changing,” Bauer said. “Zero-waste initiatives by many municipalities, and the fact that China is no longer taking the world’s plastic waste, means that we must find a better way to recycle and utilize this virtually untapped resource.”
“Resynergi is focused on alternative energy production to eliminate plastic waste — a goal that addresses environmental responsibility while presenting profitable business opportunities.”
He said the per system capital investment in this energy conversion technology is about $350,000 for the equipment, with a 1.5- to three-year simple payback, given an operating energy cost of 25 cents per gallon of diesel fuel that has a market value of $2.75 or more per gallon at the pump.
The new technology reverse engineers plastics through a unique form of pyrolysis — the thermal decomposition of plastic waste without oxygen — providing up to 75 percent conversion of plastic into diesel fuel. Off gases produced during this stage can be recycled to fuel a co-generation system providing up to 50% of the energy needed to power the equipment.
This process also results in zero sulphur, good lubricity and high cetane, properties comparable to those found in commercial diesel fuels. Lubricity is a measure of the reduction in friction and/or wear by a lubricant. Cetane shortens the delay in ignition.
Resynergi designed a compact, portable unit, with higher and faster operating efficiency and low overhead requirements, capable of processing up to five tons of plastic waste per day.
“Our proprietary reactor uses microwaves to gasify melted plastic in a thermal chamber that is 10 times smaller than other systems on the market,” Bauer said. “These gases travel to a condenser where oil precipitates out and where off-gases are channeled to an oxidizer, producing water and traces of [carbon dioxide]. The entire system could fit easily into a 9-by-20-foot shipping container.”
The company completed its fourth beta test of its pilot prototype, dubbed “The Evolucient CMAP 1 Rapid Continuous Pyrolysis System,” that achieves high temperatures required for the combustion and gasification process leading to condensation of high-grade diesel fuel Nos. 1 and 2.
Angel investors have provided almost $1 million in R&D development funds to date. The company will seek series A venture capital funding during 2017.
Other sources of capital include grants from universities supporting intellectual property innovations, along with backing from the construction industry, real estate firms, asphalt companies, biomass (woodchip) producers and recycling companies.
According to Bauer, economics of scale associated with the Resynergi system can produce an 11-to-1 return on investment, given an average energy input cost and a diesel output cost. In addition, more than 11.1 kilowatt-hours of equivalent energy output are derived from this process, versus 1 kilowatt-hour on the input side.
Bauer earned a bachelor of science degree in mechanical engineering from Stanford University and attended the UCLA Anderson School of Business Management. He was vice president for sales and marketing at Santa Rosa’s TriAccess Technologies, which was acquired by TriQuint Semiconductor. Prior positions included serving as a director for telecommunications equipment marketing with Raychem, Advanced Fibre Communications (a former Petaluma company acquired by Tellabs), ADC, ALU and Motorola.
Co-founder Tanne, a former AFC country manager for Japan, discovered that this nation had several plastic-to-oil plants and wanted to bring this technology back to the U.S. He also worked with the United Nations on a video titled “Clean Up The World” that highlighted ways to reduce waste.
www.northbaybusinessjournal.com/northbay/sonomacounty/6858004-181/sonoma-resynergi-plastics-recycle-petroleum?artslide=0
Sonoma County startup Resynergi seeks to recycle plastic trash into diesel fuel
GARY QUACKENBUSH
FOR NORTH BAY BUSINESS JOURNAL | April 12, 2017, 9:35AM
Resynergi LLC has developed what the Rohnert Park company states is a proprietary system using microwaves to transform unrecycled waste plastic into oil. By mid-year the company plans to announce orders from initial customers with equipment deliveries scheduled during the second half.
The technology, called continuous microwave-assisted pyrolysis (CMAP), can recover 250 gallons of clean, reliable diesel fuel from 1 ton of low and high-density polyethylene, polypropylene and polystyrene plastics, also known as plastics Nos. 2, 4, 5 and 6. In addition to its unique heat source, the company says its unit is small, expanding its customer pool to smaller plastic producers.
Those potential customers include carting companies, grocery chains, nonprofits, municipalities, the military, trucking firms and other sectors, according to an American Chemical Council study in 2014.
Plastic waste is mostly free today, as firms wish to offset tipping fees (from $60 to $130/ton) at landfill sites and save transportation expense. These zero-to-low material costs can help customers scale up operations.
“Today’s plastics contain a lot of stored energy in long hydrocarbon chains that can be reclaimed, while also eliminating problems associated with disposal and pollution,” said CEO Brian Bauer, who together with Jason Tanne co-founded Resynergi in April 2015. “However, today we throw most of that latent energy locked up in plastics into the trash. Our mission is to develop evolutionary energy recovery systems designed to change that.”
Some 33.5 million tons of plastic waste are produced annually in the U.S., but only 7 percent is recycled, with most being sent to municipal landfills or shipped overseas, according to the ACC. This mountain of plastic could be worth $29 billion if converted to oil.
The U.S. alone could support 600 plastic-to-oil facilities processing 20 tons of plastic per day while creating 40,000 new jobs, according to EPA, EIA and ACC data sources.
“The recycling landscape is changing,” Bauer said. “Zero-waste initiatives by many municipalities, and the fact that China is no longer taking the world’s plastic waste, means that we must find a better way to recycle and utilize this virtually untapped resource.”
“Resynergi is focused on alternative energy production to eliminate plastic waste — a goal that addresses environmental responsibility while presenting profitable business opportunities.”
He said the per system capital investment in this energy conversion technology is about $350,000 for the equipment, with a 1.5- to three-year simple payback, given an operating energy cost of 25 cents per gallon of diesel fuel that has a market value of $2.75 or more per gallon at the pump.
The new technology reverse engineers plastics through a unique form of pyrolysis — the thermal decomposition of plastic waste without oxygen — providing up to 75 percent conversion of plastic into diesel fuel. Off gases produced during this stage can be recycled to fuel a co-generation system providing up to 50% of the energy needed to power the equipment.
This process also results in zero sulphur, good lubricity and high cetane, properties comparable to those found in commercial diesel fuels. Lubricity is a measure of the reduction in friction and/or wear by a lubricant. Cetane shortens the delay in ignition.
Resynergi designed a compact, portable unit, with higher and faster operating efficiency and low overhead requirements, capable of processing up to five tons of plastic waste per day.
“Our proprietary reactor uses microwaves to gasify melted plastic in a thermal chamber that is 10 times smaller than other systems on the market,” Bauer said. “These gases travel to a condenser where oil precipitates out and where off-gases are channeled to an oxidizer, producing water and traces of [carbon dioxide]. The entire system could fit easily into a 9-by-20-foot shipping container.”
The company completed its fourth beta test of its pilot prototype, dubbed “The Evolucient CMAP 1 Rapid Continuous Pyrolysis System,” that achieves high temperatures required for the combustion and gasification process leading to condensation of high-grade diesel fuel Nos. 1 and 2.
Angel investors have provided almost $1 million in R&D development funds to date. The company will seek series A venture capital funding during 2017.
Other sources of capital include grants from universities supporting intellectual property innovations, along with backing from the construction industry, real estate firms, asphalt companies, biomass (woodchip) producers and recycling companies.
According to Bauer, economics of scale associated with the Resynergi system can produce an 11-to-1 return on investment, given an average energy input cost and a diesel output cost. In addition, more than 11.1 kilowatt-hours of equivalent energy output are derived from this process, versus 1 kilowatt-hour on the input side.
Bauer earned a bachelor of science degree in mechanical engineering from Stanford University and attended the UCLA Anderson School of Business Management. He was vice president for sales and marketing at Santa Rosa’s TriAccess Technologies, which was acquired by TriQuint Semiconductor. Prior positions included serving as a director for telecommunications equipment marketing with Raychem, Advanced Fibre Communications (a former Petaluma company acquired by Tellabs), ADC, ALU and Motorola.
Co-founder Tanne, a former AFC country manager for Japan, discovered that this nation had several plastic-to-oil plants and wanted to bring this technology back to the U.S. He also worked with the United Nations on a video titled “Clean Up The World” that highlighted ways to reduce waste.
www.northbaybusinessjournal.com/northbay/sonomacounty/6858004-181/sonoma-resynergi-plastics-recycle-petroleum?artslide=0

